Об инструментальном инжиниринге и изготовлении изделий из ПВХ
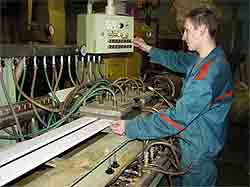
Это отделочные стеновые панели шириной 100 мм и длиной 2,7, 3,0 и 6,0 м, стартовый профиль, плинтус, уголок внутренний и наружный, а также профили для гипсокартонных систем.
Первая, опытная продукция была выпущена в 1998 г., а в 1999 г. начался массовый ее выпуск.
Сегодня основными направлениями деятельности компании являются производство различных профилей из жесткого ПВХ, конструирование и изготовление экструзионного формующего инструмента, поставка экструзионного оборудования - как нового, так и восстановленного, а также выполнение проектов под ключ.
Речь идет о проектировании и монтаже импортных технологических линий под ключ для клиента. При этом специалисты компании осуществляют не только запуск линии, оснащение ее инструментом и последующее обслуживание, но и обучение персонала, а также полный инжиниринг предприятия заказчика.
Основной сбыт осуществляется в российском регионе, так как мощность предприятия достаточно велика, и белорусский рынок просто не в состоянии освоить все производимое ИП "Racoon Plastic".
Предприятие работает, что немаловажно, только на импортном сырье - это корпоративный принцип. Компаунд (поставщик - компания "Solvay") поступает из Бельгии.
С ноября 2001 г. начнется производство отделочных панелей шириной 200-250 мм. Это ламинированные изделия более 10 цветов и оттенков.
КБ фирмы может разработать профиль любой конфигурации в соответствии с заданием клиента, любой экструзионный инструмент, любой группы сложности.
Изготовление собственного экструзионного формующего инструмента и наличие линий большой производительности позволяет компании изготавливать любые профили под заказ.
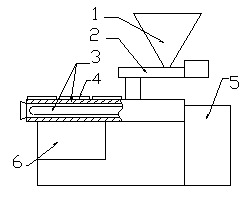
Экструдер - самая сложная и дорогостоящая составляющая экструзионной линии.
Экструдер (рис. 1) состоит из следующих основных частей: загрузочного бункера (1), дозирующего шнека (2), рабочей пары "шнеки-цилиндр" (3), электронагревателей (4), главного редуктора (5) и пульта управления (6).
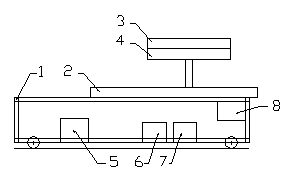
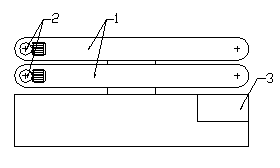
Тянущее устройство (рис. 3) состоит из двух независимых гусениц (1) с укрепленными на них траками или лентой, мотор-редукторов (2) и пульта управления (3).
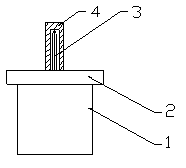
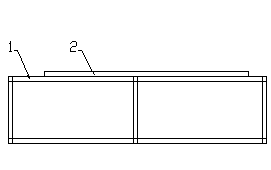
Двухшнековый экструдер с коническими шнеками для производства жестких строительных ПВХ профилей состоит из рабочего цилиндра и шнеков, привода, загрузочного устройства, системы смазки и охлаждения, системы нагрева рабочего цилиндра, системы дегазации рабочего цилиндра, электросилового шкафа, системы защиты от перегрузок и системы автоматического контроля технологического процесса.
Шнеки - основной рабочий орган экструдера. Они забирают непластифицированный ПВХ компаунд от загрузочного отверстия, пластифицируют его и равномерно подают в виде гомогенного расплава к фильере.
Экструзионная фильера - это профилирующий инструмент, придающий расплаву полимера, покидающего рабочий цилиндр экструдера, необходимую форму.
От степени совершенства реологического и теплотехнического расчета (определяются скорость экструзии, коэффициенты разбухания экструдата, вязкоэластичные деформации, сбалансированность отдельных потоков экструдата) зависит точность поперечного сечения профиля, качество его поверхности, а также механические свойства.
Продвигаясь по каналу шнеков, материал разогревается от внутреннего давления, создаваемого шнеками, а также от тепла, подводимого от электронагревателей, расположенных на корпусе рабочего цилиндра. В результате уплотнения из материала удаляется захваченный воздух, и удельный объем пробки уменьшается. Для компенсации уменьшения объема каналы шнеков выполняются с уменьшающимися объемами витков. Поэтому глубина винтового канала шнека на выходе всегда меньше, чем на входе.
По характеру процессов, протекающих на каждом участке шнеков, их можно разделить по длине на 3 основные зоны: зону питания (загрузки, то есть участок, на котором перерабатываемый материал находится в твердом состоянии), зону сжатия (плавления, то есть участок, на котором почти полностью происходит плавление материала) и зону дозирования - участок, на котором материал находится в расплавленном вязкотекучем состоянии.
Шнеки экструдера располагаются в рабочем цилиндре. Цилиндр выполняется из высокопрочной стали, внутрь цилиндра вставляются коррозионностойкие биметаллические гильзы.
Корпус цилиндра соединяется с фильерой посредством специального фланца. Обогрев корпуса осуществляется нагревателями сопротивления. Для отвода избыточного тепла и соблюдения нужного температурного режима служит система водяного охлаждения.
Питающее устройство служит для подачи суспензионного или гранулированного ПВХ компаунда в рабочий цилиндр экструдера посредством шнека, имеющего отдельный электропривод. Оборудовано устройствами предварительного уплотнения материала и системой вакуумирования для удаления летучих веществ.
Работа автоматической системы управления и контроля технологического процесса протекает на двух уровнях.
Это, во-первых, управление ходом процессов и координация работы отдельных узлов линии, во-вторых, совмещение функциональных схем контроля (регулировка температуры, частоты вращения шнеков, давления экструдата).
Можно сказать, что на самом деле "Racoon Plastic" развивает одновременно два основных направления - инструментальный инжиниринг и изготовление собственно жестких ПВХ-панелей и всех сопроводительных профилей.
Инструмент конструируется и изготавливается в строгом соответствии cо стандартами ISO и ГОСТ. Экструзионный инструмент, произведенный ИП "Racoon Plastic", не уступает, а по многим показателям превосходит лучшие мировые аналоги. Высокое качество этого инструмента оценили многие фирмы - как в странах СНГ, так и за пределами содружества.
Формующий инструмент для производства ПВХ профиля является "сердцем" экструзионной линии. Именно от его конструкции и технического исполнения зависит качество ПВХ профиля и скорость экструзии. Наличие различных комплектов формующего инструмента позволяет избежать простоев экструзионного оборудования из-за колебаний рыночного спроса на отдельные профили.
Для увеличения ассортимента выпускаемой продукции компанией "Racoon Plastic" был создан проектный центр, который позже стал изготавливать формующий инструмент и для сторонних заказчиков.
При разработке формующего инструмента центр использует современные САПР. Это позволяет с минимальными погрешностями выпускать полный комплект конструкторской документации на формующий инструмент, состоящий из фильеры, калибраторов и 3D-модели. Реализация цикла CAD/CAM/CAE осуществляется в срок от 5 до 15 суток. Значительно ускоряет процесс проектирования использование базовых типоразмеров фильер, охватывающих весь диапазон ходовых ПВХ профилей. Расчеты конструктивно-технологических параметров формующего инструмента (таких, например, как конфигурация канала на различных этапах формования ПВХ профиля, распределение тепловых зон) выполняются на основе эмпирических формул и практического опыта конструкторов и технологов компании. При изготовлении оснастки используется высокотехнологичное металлообрабатывающее оборудование.
Система сопровождения и контроля качества изготовления позволяет свести к минимуму доводку формующего инструмента на месте его эксплуатации. Доводка формующего инструмента под определенную экструзионную линию осуществляется высококлассными специалистами, имеющими большой опыт работы.
Компания "Racoon Plastic" оказывает услуги в приобретении бывших в употреблении экструзионных линий из Европы. Это линии самых различных изготовителей, производительности, технических характеристик, состояния (рекондиционное оборудование или оборудование "как есть") и годов выпуска.
Большая база адресов зарубежных производителей ПВХ профилей и поставщиков бывшего в употреблении оборудования, практический опыт в этой области и личные контакты с многочисленными зарубежными партнерами позволяют компании предоставлять ее клиентам любое необходимое им экструзионное оборудование.
Компания "Racoon Plastic" сотрудничает с организациями всех видов собственности.
Подробности - на Интернет-сайте компании по адресу www.extrusion.by.Подготовил Сергей ЗОЛОТОВ, фото Сергея ШАРУБЫ
Строительство и недвижимость. Статья была опубликована в номере 41 за 2001 год в рубрике менеджмент