Прогрессивные материалы и технологии для строительства и ремонта мостов в CШA и Великобритании
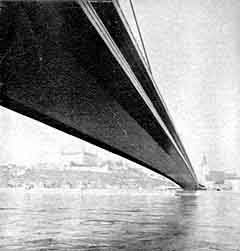
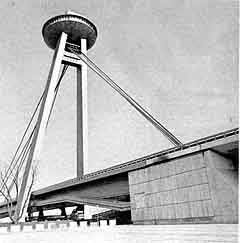
Рис. 1, 2. Общий вид моста в г. Братиславе (Словакия), на металлические элементы и конструкции которого нанесены антикоррозионные покрытия.
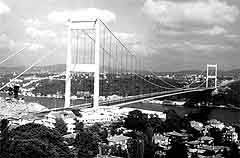
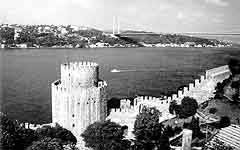
Рис. 3, 4. Общий вид вантового моста в г. Стамбуле (Турция), металлические конструкции которого защищены антикоррозионными покрытиями.
Понтонный мост из гигантских железобетонных понтонов через канал "Hood Canal" (США)
Для замены половины старого понтонного моста длиной 2,1 км, разрушенного штормом, использовано 12 понтонов на участке длиной 1140 м. Каждый понтон несет на себе опоры и пролетное строение и представляет собой полую прямоугольную ячеистую коробку. Между собой понтоны соединены арматурой, напряженной после бетонирования, и крепятся к морскому дну при помощи системы, состоящей из кабелей диаметром 7,6 см, и массивных бетонных анкеров, к которым эти кабели прикреплены.
Каждый понтон имеет длину 109, ширину 18,2 и высоту 5,4 м. Выполненный из сборного и монолитного бетона понтон имеет 36 отсеков, расположенных в три ряда. В средней части размещены две галереи, по которым проходят кабели. Доступ в каждый водонепроницаемый отсек обеспечивается люками.
Вместе с надстройкой (опорами и пролетным строением) масса понтонов составляет от 8000 до 9000 т.
Из 26 крупногабаритных анкеров, имеющих форму бадьи, 24 имеют диаметр 13,8 м и два - 16 м. Высота всех анкеров равна 7,8 м. Мacca незаполненных анкеров составляет 1300 т, а заполненных камнем и погруженных в воду - 3500 т.
Понтоны устраивались в ремонтном доке, специально оборудованном для одновременного бетонирования шести конструкций.
В расположенном в порту Такома (США) доке длиной 174, шириной 143 и глубиной 6 м разработан огромный котлован, при сооружении которого вынуто 228 тыс. м3 грунта. Уровень грунтовых вод поддерживался ниже основания дока.
После устройства шести понтонов рабочая площадка дока была затоплена, эти понтоны доставили на плаву к ближайшему месту стоянки судов, где на понтонах бетонировали опоры и устанавливали пролетные строения. Затем док осушали, в нем бетонировали остальные шесть понтонов, а на них устанавливали опоры и пролетные строения.
Сборные элементы, из которых выполнены понтоны, представлены [-образными панелями для устройства наружных стен и I-образными панелями для внутренних стен. Длина обоих элементов составляет 8,5, толщина 0,25 м, масса 65 т. Элементы изготовляли на строительной площадке рядом с доком. Система электропрогрева ускоряла твердение бетона, что позволило извлечь готовые элементы из опалубки через 16ч.
В док элементы доставляли трейлерами. Сборку производили на бетонных плитах. Две [-образные и две I-образные панели образуют секцию понтона длиной 18 м, разделенную на три отсека. На устройство одного понтона требуется 24 [-образных и 24 I-образных панели. Затем производили бетонирование основания, диафрагменных стен и перекрытия понтона .
Торцовые стены понтона образованы крупноразмерными панелями длиной 18, высотой 5,4, толщиной 0,6 м, масса их составляет 135 т. Для первых шести понтонов панели бетонировали в доке. Для остальных понтонов готовые панели доставляли со строительной площадки, где их изготавливали, 14-осными (56 колес) трейлерами фирмы "Shaughnessy" длиной 30, шириной 3 м, грузоподъемностью 380 т с 3-осным (10 колес) трактором-тягачом.
Бетон для изготовления сборных и монолитных конструкций подавали тремя бетононасосами с шарнирно-сочлененными стрелами фирм "Whitmans и Schwing".
На устройство 12 понтонов было израсходовано 28,9 тыс.м3 бетона, 2300 т преднапряженной арматуры, 4000 т арматуры, покрытой эпоксидной смолой, и 184 км каналообразователей для напряженной арматуры.
После изготовления первых шести понтонов, их на плаву доставили к причалу порта Такома, где на них соорудили надстройку в виде опор (колонн), ригелей, балок и плит пролетных строений. Монолитные бетонные колонны имеют диаметр 1, высоту 6 м, ригели в длину 8, ширину 1,2 и высоту 0,8 м.
Для пролетного строения использовано 224 предварительно напряженных железобетонных балок длиной 18, толщиной 1,2 м.
На сооружении понтонов с надстройкой было занято 850 чел.
Бетонирование анкеров вели в три стадии (основание, средняя часть, верхняя часть). Нa первой стадии (бетонирование основания на высоту 1,2 м) 160 м3 бетонной смеси подавали в опалубку круглой формы, установленную по центру рельсовых путей, подходящих к воде.
Специальный портальный кран, выполненный из стальных балок и перемещающийся на железнодорожных тележках, оборудован подъемной системой. Восемь цилиндров системы грузоподъемностью по 200 т приводились в действие насосом с электрогидравлическим приводом.
Пocлe набора бетоном требуемой прочности под действием цилиндров основание анкера поднималось из опалубки и переносилось портальным краном к следующему месту бетонирования.
Каждый готовый анкер оснащен двумя отверстиями, позволяющими связывать его кабелем с понтоном. Форма отверстий позволяла опоясывать анкер по половине его периметра.
Забетонированные анкеры при помощи лебедки перемещали к концу рельсовых путей, подходящих к воде, и спускали на воду.
Нa доставку анкера к мостовому переходу на расстояние 112 км требовалась одна неделя. Здесь анкеры устанавливали в проектное положение при помощи катамарана, состоящего из двух барж, которые отстояли друг от друга на расстоянии 19 м и были соединены двумя стальными балками.
Кабель диаметром 7,5 см пропускали через анкеры до их погружения и присоединяли к буям, плавающим на водной поверхности, для последующей связи с понтонами. Затем анкеры заполняли 12 тыс. т дробленого шлака и погружали их на дно.
Проектное положение каждого анкера определяли при помощи компьютера, расположенного на катамаране. Анкеры размещали на расстоянии 300-600 м от оси новой части моста.
Готовые понтоны с надстройкой были отбуксированы к мостовому переходу (также на расстояние 112 км) и соединены с анкерами. Мост рассчитан на нагрузку от ветра скоростью 132,8 км/ч и шквальные ветры скоростью 176 км/ч.
Восстановление бетонного настила моста в штате Нью-Джерси (США)
При восстановлении настила моста в штате Нью-Джерси, по которому осуществлялось движение тяжеловесных транспортных средств, был использован метод удаления старого бетона струей воды под высоким давлением. После тщательного изучения состояния настила моста специалисты департамента транспорта приняли решение удалить старый бетон на глубину 1 дюйм (2,54 см) ниже верхнего слоя арматуры, а в некоторых местах - на полную глубину.
Специалисты фирмы "Conduit-Frapaul", которым было поручено осуществить данные работы, рассмотрели несколько типов приспособлений для гидроудаления старого бетона с целью достижения наивысшей производительности труда и выбрали передвижную установку с соплами для подачи воды под высоким давлением и возможной шириной обрабатываемой полосы 6 футов (1,82 м). Производительность гидроразрушителя установки 120 кв. футов (11,6 м2) бетона в час. Время работы установки 20 ч в смену, 6 дней в неделю. Заправка резервуара водой осуществлялась из природных источников после фильтрации через специальную систему, работающую с использованием ультрафиолетовых лучей. Куски разрушенного бетона, большинство из которых имело незначительные размеры, промывали горячей водой и высушивали. После прохождения через специальные водоочистительные сооружения вода вновь попадала в реку.
В рамках контракта по восстановлению настила моста предусматривалась замена 500 тыс. фунтов (226,8 тыс. кг) стальной арматуры, но так как данный способ разрушения бетона не вызывает повреждения арматуры, заменили только 3 тыс. фунтов (1,36 тыс. кг) арматуры.
Технология производства работ по восстановлению настила моста заключалась в следующем.
Вначале на место удаленного бетона укладывали цементобетонную смесь. Всего уложили 5 тыс. фунтов (2,27 тыс. кг) смеси. К месту производства работ ее доставляли в автомобилях-самосвалах и разгружали по 80 кубических ярдов/ч (62,2 м3/ч) бетононасосами, оборудованными шлангами-рукавами диаметром 6 дюймов (15,2 см), а окончательную отделку производили финишером.
Затем устраивали верхний слой настила толщиной 1,25 дюйма (3,18 см) из цементобетона, модифицированного латексом. Технологический перерыв между устройством нижнего и верхнего слоев настила составлял 3 дня.
Работы по восстановлению настила моста производили на площади 200 тыс. кв. футов (18,58 тыс. м2). С помощью гидроразрушения снят бетон на площади 140 тыс. кв. футов (13,01 тыс. м2). В общей сложности уложено 3200 ярд3 (2446,6 м3) бетона. В результате использования этого метода фирма "Condiut-Frapaul" сэкономила 500 тыс. долл. за 50 дней работы.
Антикоррозионные покрытия
Современным способом защиты стали от коррозии является система Duplex, которая включает метод горячего цинкования и послойное нанесение антикоррозионных покрытий. Эта система отличается простотой выполнения работ, хорошим защитным действием и экономичностью.
Основными предпосылками качественной защиты от коррозии металлических элементов и конструкций дорожного строительства при помощи антикоррозионного покрытия являются: тщательная обработка поверхности, поврежденной коррозией - удаление ржавчины, очистка от окалины; достаточная толщина слоя покрытия; правильный выбор материала покрытия в зависимости от воздействий, вызывающих коррозию; тщательное нанесение нового покрытия; отсутствие неблагоприятных воздействий окружающей среды при нанесении покрытия; соответствие готовой продукции требованиям антикоррозионной защиты.
Несоблюдение одного из перечисленных факторов приводит к повреждению покрытия уже в первые два года.
В настоящее время наблюдается тенденция проведения работ по защите от коррозии конструкций не на строительной площадке, а на заводах в стационарных установках, что дает немало преимуществ, а именно: отсутствие промышленной эмиссии и негативного влияния погодных условий, экономия времени, достижение высоких производительности и качества выполнения работ, усиленный контроль качества работ, решение проблем загрязнения окружающей среды.
Известно множество способов защиты металлических элементов и конструкций от коррозии: консервация, горячее цинкование, вихревое напыление покрытий, порошковая металлизация, нанесение пластмассовых пленок, пластизолей, органозолей, лаков, различных синтетических порошков. В дорожном строительстве металлические элементы мостов, дорожных ограждений, шумозащитных стен, дорожных знаков, водоотводов насыпей изготавливают в основном из горяче-оцинкованной стали.
В настоящее время серьезной проблемой является влияние противогололедных солей на антикоррозионные покрытия металлических элементов и конструкций мостов, снижающее срок службы таких покрытий в 2 раза (с 20 до 10 лет).
Защитные свойства антикоррозионных покрытий зависят от их состава (вяжущего, пигмента) и вида воздействия на металлические элементы и конструкции. Например, в условиях воздействия противогололедных материалов наилучшим антикоррозионным материалом является эпоксидная смола-свинцовый сурик. При воздействии других химических веществ целесообразно применять покрытия из эпоксидной смолы - двуокиси титана. Многообразие видов воздействия на металлические элементы и конструкции, а также требований к защитным покрытиям приводит к тому, что получить универсальное покрытие практически невозможно, поэтому каждая система антикоррозионной защиты является комбинацией различных свойств отдельных слоев наносимых покрытий. Используемые в настоящее время защитные покрытия готовят на основе акриловой и эпоксидной смол с малым содержанием растворителя (или не содержащими его) с добавлением новых видов пигментов, например, фосфата кальция или франклинита. В состав защитных покрытий входят также ингибиторы коррозии - цинковые или свинцово-цинковые соли органических нитросоединений. Система покрытий, как правило, состоит из нескольких слоев подгрунтовки и покрытия. Общая толщина такого четырехслойного покрытия составляет от 140 до 180 мк (от 1,4 до 1,8 мм), то есть толщина одного слоя от 35 до 40 мк. Слои такого покрытия могут иметь большую толщину (см. рис. 1, 2, 3, 4).
Строительство моста через бухту Barking
В настоящее время завершается строительство шестипролетного железобетонного моста "New Roding" через бухту Barking, расположенную в Восточном Лондоне (Великобритания). Он является частью автомобильной дороги A13. По первоначальному проекту мост должен был состоять из предварительно напряженных железобетонных балок и плит, производимых для транспортного управления фирмой "Freeman Fox". Нo главная договорная строительная компания "BalfourBeatty", ответственная не только за строительство моста, но и за строительство вспомогательной автомобильной дороги A13/A406, предложила другой проект, стоимость которого намного ниже, а мостовая конструкция состоит из металлических балок и железобетонных плит толщиной 230 мм, изготавливаемых фирмой "Cass Hayward & Partners".
Монтаж металлической конструкции заключается в установке пяти неразрезных балок длиной 187 м каждая, состоящих из поперечно скрепленных пластин. Сечение балки составляет 1,5 м, а в местах крепления консолей увеличивается до 2,5 м. Балки укладывают на железобетонные устои моста. Все балки, кроме главной, имеют свободные опоры с возможностью перемещения по горизонтали. По прогнозам специалистов, в жаркую погоду длина моста увеличивается на 75 мм. Длина основного пролета (над бухтой) составляет 52 м, стоимость монтажных работ - 450 тыс. фунтов стерлингов.
Использование гидравлического колуна прк реконструкции моста через реку Pompton
Уширение моста с четырехполосным движением через реку Pompton производила строительная компания "Grey Construction Holmdel" (штат Нью-Джерси, США) в три этапа без остановки движения транспортных средств. Этот мост является основным для движения автомобилей с севера на восток в северной части Нью-Джерси. Предполагалось устроить на мосту еще две полосы движения.
Вce опоры моста и два береговых устоя находились в хорошем состоянии. Реконструкции подлежали настил моста и верхняя часть устоев.
Для разрушения верхней части опор и устоев использовали два гидравлических колуна массой 75 фунтов (34 кг) каждый с гидравлическим приводом. Гидравлический насос создавал давление 10 тыс. фунтов на 1 дюйм2 (703,1 кг/см2).
Разрушение этих элементов моста производилось следующим образом. По всей длине опоры - 35 футов (10,67 м) - через интервал 24 дюйма (60,96 см) сверлом высверливали отверстия диаметром 1 и 3/4 дюйма (3,17 см). Затем через интервал 4 фута (1,21 м) в отверстия вставляли два колуна с разрушающим усилием, равным 700 т. Менее чем через 1 мин по всей длине опоры появились трещины. Операция повторялась несколько раз, пока не образовывалась глубокая внутренняя трещина (на это потребовалась 15 мин).
При помощи погрузчика фирмы "Caterpillar" удаляли верхнюю часть разрушенной опоры, причем эта операция была выполнена всего за 30 мин.
Евгений МАРГАЙЛИК, инженер и патентовед ВОИР
Строительство и недвижимость. Статья была опубликована в номере 27 за 1999 год в рубрике дороги