Эффективные технологии ремонта дорожных одежд автомагистралей в США
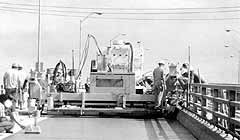
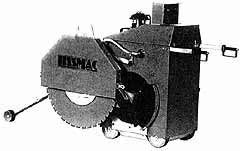
Усиление дорожных одежд методом скоростного бетонирования
В США система межштатных и главных дорог создавалась в 50-60 годах нашего столетия. В настоящее время главной задачей является не строительство новых, а содержание и реконструкция существующих дорог. Поэтому дорожные проекты включают реконструкцию подходов к мостам, укладку небольших участков дорожного покрытия для увеличения горизонтального или вертикального расстояния видимости, устройство дополнительных полос для увеличения пропускной способности, строительство коротких объездных дорог. Строительство новых дорог осуществляется довольно редко. Однако в связи с увеличением количества автомобилей возникает необходимость частого ремонта дорожных покрытий, что влияет на безопасность движения транспорта и создает неудобства при пользовании дорогами.
Новый метод строительства и восстановления дорожных покрытий, разработанный в штате Айова, позволяет открывать движение менее чем через 12 ч после проведения ремонтных работ и сводит эти проблемы к минимуму. Такой метод разработан на основе опыта ремонта мостовых покрытий, применяемого в штате Айова в течение ряда лет. Было установлено, что укладка слоя цементобетона толщиной 5-7,5 см на существующее дорожное покрытие из цементобетона целесообразна с точки зрения экономики и долговечности по сравнению с укладкой асфальтобетонного слоя.
Данный метод предусматривает следующие процессы: удаление слоя непрочного бетона, очистку поверхности, распределение по очищенной поверхности цементoneсчаного раствора для обеспечения сцепления, укладку нового цементобетонного слоя толщиной 5 см.
Опыт усиления дорожных покрытий этим методом показал, что продолжительность ухода за бетоном составляет 5-10 суток. Для сокращения этого периода департамент транспорта штата разработал метод, известный как метод скоростного бетонирования дорожных покрытий штата Айова. Применение специально приготовленного цемента, введение добавки, ускоряющей набор прочности, и использование специальных методов ухода сделало возможным открывать движение транспорта через несколько часов после укладки смеси.
В штате Айова были проведены лабораторные испытания на смесях, для приготовления которых использовался быстросхватывающийся цемент, крупно- и мелкозернистый минеральный заполнитель и тонкая зола-уноса, способствующая твердению. Прочность сцепления с существующим дорожным покрытием каждой смеси с введением различного количества водоуменьшающих и ускоряющих добавок и хлористого кальция определялась в возрасте 6, 8, 12, 18 и 24 ч. После получения состава с требуемыми свойствами были проведены полевые испытания, давшие удовлетворительные результаты.
В штате Айова началось осуществление крупного проекта с применением разработанного метода. Проект включал укладку слоя усиления толщиной 10 см на старое покрытие в возрасте 49 лет, а также его уширение на 60 см с толщиной слоя 25,4 см. Цель проекта заключалась в проверке возможности открытия движения менее чем через сутки при применении новой технологии.
Поскольку применялся цемент с высокой водопотребностью (при применении которого отмечается тенденция к значительной усадке), то водоцементное отношение поддерживалось низким и использовалась водоуменьшающая добавка, а на некоторых участках (на пересечениях дорог и на развязках в разных уровнях) применялась добавка, ускоряющая твердение.
Цементoпeсчаный раствор, образующий промежуточный слой, состоял из равных массовых частей портландцемента и песка, смешиваемых с водой, в количестве, обеспечивающем удобоукладываемость раствора. Время от момента приготовления раствора до его распределения не должно превышать 90 мин.
Подготовка поверхности включала ямочный ремонт на всю толщину покрытия, а затем дробеструйную обработку и обработку сжатым воздухом. Опыт показывает, что наиболее критическим фактором в обеспечении сцепления нового бетона со старым является наличие чистой и сухой поверхности, при которой наблюдается некоторое поглощение влаги из свежеуложенного бетона.
После проведения подготовительных работ в местах, где в старом дорожном покрытии имелись швы, и в местах ямочного ремонта на всю толщину размещались пластмассовые прокладки шириною 15 см. Позже, после укладки слоя усиления, в этих местах пропиливали швы, заполняемые силиконовым герметиком (см. рис. 1).
После такой подготовки поверхности дорожного покрытия распределяли тонкий слой раствора, обеспечивающего сцепление, и до его cxватывания укладывали цементобетонный слой усиления. В случае каких-либо задержек с укладкой нового слоя бетона на высохшую поверхность дорожного покрытия распределяли дополнительное количество раствора для сцепления.
За одну операцию слой бетона укладывали на всю ширину и толщину одной полосы (см. рис. 2). Затем производили отделку бетонного покрытия, нарезку борозд для обеспечения шероховатости, нанесение пигментного состава белого цвета для выдерживания, после чего бетон накрывали легким защитным материалом. Такой материал удаляли после того, как слой бетона набирал минимальную прочность 2,46 МПa. Затем пропиливали поперечные и продольные швы глубиной 3,8 см.
Операции уплотнения, отделки, создания текстуры и нанесение состава для ухода должны выполняться за время не превышающее 45 мин.
Для устройства слоев дорожных покрытий таким методом применяется обычное оборудование, при бетонировании одной полосы дорожного покрытия на смежной полосе сохраняется движение транспорта.
Скоростной метод бетонирования позволяет увеличить безопасность движения транспорта, сократить сроки строительства, уменьшить стоимость и увеличить срок службы покрытия магистрали или дороги.
Использование нововведений при ремонте скоростной магистрали "Long Island" в CШA
Скоростная магистраль "Long Island" является одной из главных магистралей штата Нью-Йорк, поэтому важнейшей проблемой стало определение минимальных сроков ее ремонта и остановки движения транспорта. Над этой проблемой работало Государственное управление транспорта штата Нью-Йорк. Используя и совершенствуя опыт Дорожного управления транспорта штата Мичиган, ремонт дорожного покрытия магистрали "Long Island" произвели за одну ночь. Участок дороги протяженностью 5,5 мили (8,851 км) был закрыт для движения транспорта с 22 ч вечера до 6 ч утра. Стоимость проекта составила 8,3 млн долл.
Ранее ремонт небольших выбоин на магистрали осуществляли, используя битум. Под влиянием перепада температур швы на дорожном покрытии открылись, что привело к значительному ухудшению егто состояния.
Эффективность данного метода обеспечили: применение метода "сухой" установки штырей (штыри с эпоксидным покрытием устанавливались без эпоксидного раствора); быстрое вырезание части плиты без повреждения основания дорожного покрытия; применение скоростных гидравлических сверл, обеспечивающих высокую производительность и точность; использование быстротвердеющего бетона, что позволило возобновить движение транспорта сразу же после ремонта; использование мобильных смесителей с дозирующим устройством, перемешивающих сухие ингредиенты на месте с водой; использование временной деревянной платформы в первые 2 ч работы и в последние 4 ч, что значительно повысило производительность труда.
Ремонт плит осуществлен выборочно. Общая протяженность отремонтированных плит составила 12 футов (3,66 м).
Бетонные плиты толщиной 9 дюймов (22,86 см) вырезались пилой на полную глубину на расстоянии 1 фута (0,304 м) от поперечного шва и параллельно ему. Затем с помощью установки Vermeer CC-135 плиты разбивали на двух- и трехфутовые куски и убирали их погрузчиком на гусеничном ходу с обратной лопатой Dynahoe 490. Такой метод дробления и удаления разбитых кусков эффективнее применения пневматических молотов. Кроме того, основание дорожной одежды при этом практически не повреждается.
В местах, где все-таки произошли незначительные повреждения основания, для его восстановления использовали трамбовочную машину K91 Т.
Отверстия для штырей просверливали гидравлическим сверлом Doruel Pak DP3 с тремя насадками (фирмы "Tamrock"), которое монтировалось на стреле экскаватора с обратной лопатой Dynahoe и приводилось в действие его гидравлической системой. Передвижение с одного участка работы на другой осуществлялось без затруднений. Применение такого сверла с тремя насадками позволило оператору просверливать одновременно три отверстия. За 10 мин. просверливали 24 отверстия. Глубина отверстий составляла 9 дюймов (22,86 см).
Работа гидравлических сверл фирмы "Tamrock" характеризуется высокой скоростью, точностью и возможностью сверлить отверстия круглой формы различных размеров. Последнее обеспечивается независимым вращающим механизмом.
Гидравлические сверла осуществляют 4000 выпусков воздуха в 1 мин. и обеспечивают динамическое воздействие около 30 футов•фунт (40,67 Н•м) на выпуск воздуха. Пневматические сверла в среднем обеспечивают динамическое воздействие 145 футов•фунт (196,59 Н•м) на выпуск воздуха. Применение гидравлических сверл характеризуется значительным уменьшением скалывания краев у просверленного отверстия и меньшим появлением внутренних микротрещин.
В гидравлических сверлах используют резцы различных размеров. Так, применение 30-миллиметрового металлического резца дает возможность получить отверстие диаметром 30 мм. Возможная неточность составляет 1/50 дюйма (0,05 см). Штыри с эпоксидным покрытием диаметром 1 и 1/8 дюйма (2,86 см) и длиной 18 дюймов (45,72 см) вставляются в просверленные отверстия. С помощью компрессора, смонтированного на месте ковша, просверленные отверстия прочищаются воздухом. Кроме того, компрессор является добавочным контрвесом к сверлу.
Гидравлические сверла фирмы "Tamrock" легко монтируются и демонтируются на стреле экскаватора.
Приготовление цементобетонной смеси производилось в два этапа. Для быстрого затвердевания цементобетонной смеси в массу добавили хлорид кальция, ускоряющий гидратацию цемента. Дорожное покрытие из такой смеси становится прочным через 30 мин после его укладки.
Каждый кубический ярд (0,765 м 3) цементобетонной смеси состоит из 1449 фунтов (657,26 кг) каменного материала размером в 1 дюйм (2,54 см), 1320 фунтов (598,74 кг) песка, З8,6 галлонов (146,12 л) воды, 826 фунтов (374,66 кг) цемента типа III и 20,65 унций (611,52 см 3) воздухововлекающей добавки W.R. grace`s Daravair. Хлорид кальция представляет собой стандартный раствор, содержащий 29% безводного хлорида кальция.
Сначала для приготовлений смеси предполагалось использовать обычные автобетоносмесители, но их производительность оказалась недостаточной. Поэтому решено было использовать автобетоносмесители барабанного типа. Для этого из дозаторной установки в автобетоносмеситель загружали песок и каменный материал, а затем под наклоном 15% из другого бункера засыпали цемент типа Ill, причем таким образом, что его проникание в каменный материал и песок было минимальньм. Во время перевозки большая часть цемента не увлажнилась за счет влажности каменного материала и песка.
Воду добавляли в смесь на месте. Ее количество определялось с учетом влажности каменного материала и песка, а также раствора хлорида кальция. Соотношение воды и цемента контролировалось смонтированным на грузовике водомером (см. рис. 3). При 50 галлонов/мин (189,27 л/мин) точность водомера составила 1/100 галлонов (0,0378 л).
Используя критическую температуру бетона, решено было также повысить температуру воды затворения, в результате чего более высокая температура бетона сократила сроки его твердения. Бетонная смесь теперь укладывалась при температуре 95-100 град F (35-37°С).
Температура воды варьировалась в зависимости от температуры каменного материала, песка и цемента.
На месте работы барабаны автобетономешалок вращались со скоростью 20 об/мин. В барабан, не останавливая его, добавляли 50 галлонов воды (189,27 л) и хлорид кальция, находящийся в баке вместимостью 42 галлона (158,99 л), смонтированном на грузовике. Смешивание всех ингредиентов осуществляли за 130 оборотов барабана, смесь уложили за 30 мин с момента ее приготовления.
На укладку и отделку каждой плиты уходило 5-10 мин. После окончательной отделки и ухода за свежеуложенным цементобетонным дорожным покрытием на его поверхности стелили пластмассовый лист, на который укладывали двухдюймовую (5,08 см) изоляционную панель Dow Styrofoam, сохраняющую температуру до 180 град F (82°С) и влажность. Ожидаемый предел прочности на сжатие составлял 2000 фунтов/кв. дюйм (609,60 м на 6,45 см 2). Температуру свежеуложенного дорожного покрытия постоянно контролировали, и, когда она достигла 150 град F (65°С), возобновлялось движение транспортных средств.
Основные работы по ремонту плит заканчивали к 2 ч ночи.
Дальнейший ремонт производили с использованием временных деревянных платформ шириной 11 футов (3,35 м), толщиной 9 дюймов (22,86 см), три из них длиной по 6 футов (1,83 см), две - по 4 и 1/2 фута (1,37 м) и две - по 9 футов (2,74 м).
Платформы снабжены подъемными кольцами, убирающимися вовнутрь, они обладают прочностью и обеспечивают невредимость основания дороги. Транспортные средства могут двигаться по ним на высокой скорости. Такие платформы плотно вставляются на место вырезанной плиты. Только одно это нововведение повысило производительность труда на 20%.
К 6 часам утра отремонтированная магистраль была открыта для движения транспорта.
Евгений МАРГАЙЛИК, инженер и патентовед ВОИР
Строительство и недвижимость. Статья была опубликована в номере 22 за 1999 год в рубрике дороги