Оборудование и технологические линии фирм Европы для изготовления дорожных и строительных изделий
Оборудование для производства бетонных изделий
На заводе фирмы "Fries & Co" в г. Мюнхене установлено новое оборудование для производства бетонных изделий фирмы "Schlosser". Монтаж дополнительной мешалки модели 3D 500 фирмы " Schlosser " для производства облицовочного камня позволил увеличить мощность дозаторно-смесительной установки.
В состав нового оборудования входит универсальный станок SV30 для изготовления различных бетонных блоков, включая 60-миллиметровые замковые дорожные и бордюрные камни. Из-за широкого ассортимента выпускаемых изделий на станке приходится часто менять формы (замена производится за 20 минут, включая регулировку пружин и высоту при съеме форм). Форма устанавливается между двумя резиновыми прижимами, у которых во время вибрации усиливается захватное действие.
Давление прижима регулируется пневматическим устройством, что позволяет очень точно производить регулировку и лучше контролировать интенсивность вибрации в процессе предварительного и основного виброуплотнения.
Станок можно запрограммировать на разную высоту подъема формы и на другие параметры. Данные вводятся на пульт управления, откуда с помощью электроники производится контроль параметров и их регулировка. Для обслуживающего персонала облегчен процесс регулировки операций, производимых при переходе с одного вида изделия на другое (для управления станком требуется один рабочий). При переводе станка на изготовление другого изделия убирается второй питатель. Процесс увязки виброуплотнения с требуемой высотой изделия позволяет производить бетонные блоки и бордюрные камни с более жесткими допусками. Отключение окончательного виброуплотнения производится с помощью электромеханического контакта.
Облицовочные пустотелые блоки изготовляются с точностью 1 мм. Для подачи изделий от станка на стеллажи используются цепные конвейеры, действующие по принципу включения-выключения для создания резервной емкости при полной загрузке. У стеллажей имеется дополнительный (резервный) ярус на уровне съемной тележки, которая получает команду на съем изделий с верхнего и нижнего ярусов. В зависимости от высоты изделий стеллажи можно загружать в 9 и 18 ярусов. На уровне каждой съемной тележки находятся два поддона.
После загрузки стеллажей в пропарочные камеры, последние закрываются створками на роликах с механическим приводом, получая команду от ЭВМ съемной тележки. Для того чтобы свести к минимуму тепловые потери, пропарочная камера открывается только при подходе съемной тележки для загрузки и выгрузки изделий.
После пропарочной камеры изделия поступают на снижатель, оборудованный, как и стеллажи, резервным ярусом.
На выходе со снижателя установлен короткий прямой конвейер, на котором осуществляется контроль качества изделий, а за конвейером следует перегрузочное устройство. Это устройство дает возможность работать пакетировщику в замедленном темпе, в результате чего пакетирование производится более плавно и точно. В состав перегрузочного устройства входит передаточно-перестановочное оборудование, на которое изделия в зависимости от своего характера либо попадают, либо минуют. Здесь же установлен захват, с помощью которого изделия снимаются с одного рабочего поддона (при необходимости с поворотом на 90°) и передаются на параллельный конвейер, либо этот захват держит их до тех пор, пока следующий поддон не займет то же положение. Затем устанавливается первый слой изделий на верх второго поддона, который уже с двойным грузом поступает на пакетировщик. Готовые пакеты изделий загружаются на специальную тележку для подачи на обвязочную станцию.
Если передаточно-перестановочное устройство используется для транспортировки изделий в вертикальном положении (дорожные плиты, бордюрные камни), то изделия с первого конвейера поступают на параллельный конвейер, где находятся блоки, поступающие с разных поддонов. Затем конвейер отделяет партию изделий длиной 1 м с таким расчетом, чтобы следующее далее горизонтальное обвязочное устройство могло эту партию обвязать за один раз. В процессе этой операции "проталкивания" и перестановки для узких и высоких изделий можно использовать захваты и направляющие.
Обвязанные изделия по ленточному конвейеру пакетировщиком подаются к передаточным тележкам, которые поступают на пост вертикальной обвязки, где верхний слой готовых пакетов покрывается пластиком. Устройства горизонтальной и вертикальной обвязки поставляются фирмой "Cuclop International", а обвязочная установка смонтирована фирмой "Schlosser".
Готовые изделия на тележке вывозятся на склад, где штабелируются и оставляются на открытом воздухе до полного выдерживания. После снятия бетонных изделий производственные поддоны очищают и переворачивают. Участок очистки поддонов оборудован пылеулавлявающей установкой.
После очистки и кантования поддоны поступают на так называемый буферный участок, где они укладываются в штабели по 25 штук, и с помощью захвата подаются либо на резервный участок, либо на пост загрузки, откуда поступают к станку для следующего цикла изготовления блоков. Буферный или накопительный участок для поддонов необходим при производстве высоких изделий, когда требуется меньшее количество рабочих поддонов. Резерв поддонов на заводе нужен в случае перехода на выпуск изделий меньшего размера, например, дорожного камня. Всего для производственного процесса предусмотрено четыре буферных или резервных участка: на цепном конвейере между станком для производства блоков и стеллажом, на дополнительных ярусах стеллажей и снижателя и участок резервных поддонов, следующий за пакетировочной машиной. Все эти резервные емкости позволяют всему заводу работать с максимальной гибкостью и легко производить регулировки, необходимые при переходе с одного изделия на другое, даже если эти изделия совершенно разного размера и требуют разной продолжительности цикла их изготовления.
Установка для изготовления бетонных камней
Различные железобетонные камни для мощения покрытий проезжей части и тротуаров улиц, пустотелые блоки из тяжелого бетона для строительства подвалов и блоки "лиопора" для каменной кладки изготовляются на новом оборудовании, в состав которого входит установка Zenith-Hydro-Blitz 860AZ фирмы "UHL" (ФРГ).
Установка представляет собой автомат для производства бетонных камней высотой 50-400 мм. Автомат оснащен электронным свободно программируемым управлением, а также регистратором рабочего времени. Хорошую работу автомата обеспечивают многоконтурная гидросистема среднего давления, гидравлическое приспособление для прижатия форм с направляющей для поддонов, системы гидравлической фиксации нагрузки во время снятия опалубки с дополнительным устройством для подачи облицовочной бетонной смеси, состоящий из трех частей высокопроизводительный вибростол, высокочастотный дисбалансный вибратор для трамбующей головки и вибростол с бесступенчатым регулированием энергии вибрации и направленными колебаниями, вибратор стола с противоточным тормозом и охлаждающий вентилятор. Автомат рассчитан на поддоны размерами 1400х1000 мм.
После выгрузки загруженных поддонов из машины изделия подаются на подъемное устройство. В зависимости от толщины изготавливаемых изделий на поддоны укладывается до 8 слоев. При достижении нужного количества по два поддона устанавливаются на специальную тележку, которая перемещается на различной высоте, а также вдоль и поперек цеха, обеспечивая подачу изделий на склад затвердевания, состоящего из шести линий.
После разгрузки поддонов на линии затвердевания тележка автоматически возвращается обратно, чтобы забрать следующие поддоны.
За счет использования тепла гидратации и способа хранения продукции достигается высокая начальная прочность камней. Затвердевшие изделия вывозятся на тележках, синхронно работающих с первыми тележками, и подаются к штабелировщику. Уложенные штабелями на пластинчатом конвейере изделия попадают на пост упаковки, где вертикально обвязываются стальной проволокой в виде пакетов. Каждый обвязанный пакет затем упаковывается в пластмассовую пленку. После вертикальной упаковки захватом транспортной линии пакеты перемещаются на пост для горизонтальной упаковки, а отсюда - на склад готовой продукции. Освободившиеся поддоны возвращаются обратно к упаковке. Бракованные изделия удаляются с поддонов с помощью вакуумного ручного приспособления.
Опрокидывающаяся виброплощадка NUCRI фирмы "Stahlbau Nuspl" (ФРГ)
Фирма "Stahlbau Nuspl" разработала новый тип гидравлической опрокидывающейся наклонной виброплощадки типа Nucri, уровень шума которой при работе не превышает 85 дБ. Основная конструктивная особенность виброплощадки заключается в том, что поверхность ее выполняет определенное заданное колебание. Виброплощадка еще в незагруженном состоянии генерирует сравнительно небольшие колебания, уменьшающиеся по мере загрузки. Необходимая вибрация достигается за счет вибраторов.
В середине стола под каждой поперечной балкой расположен инерционный вибратор. Вибраторы взаимно соединены, благодаря чему даже при неравномерной загрузке обеспечивается смещение по фазе дисбалансов соседних вибраторов на 180°. С учетом плотного размещения генераторов (возбудителей) можно применять маломощные вибраторы.
При частоте колебаний 70 Гц каждый вибратор развивает центробежную силу в 3 кН. Получающиеся при этом амплитуды ускорения на опрокидывающейся виброплощадке в значительной степени зависят от динамических характеристик конструкции. Высокое ускорение достигается при частоте возбуждения, близкой к собственной частоте.
После определения усилия каждой поперечной балки для обеспечения малошумной работы в зависимости от мощности установленных вибраторов размещаются дисбалансы без собственного привода.
К вибростолу фирма "Stahlbau Nuspl" предлагает рамочные конструкции, позволяющие изготовлять ходовые сборные элементы, но одновременно исключающие создающийся шум при контакте с поверхностью виброплощадки.
Оборудование для производства бетонных труб фирмы "Mario Croci & Figli" (Италия)
Итальянская фирма "Mario Croci & Figli" выпускает для бетонной промышленности различное оборудование. В состав оборудования входят станки-автоматы серии MACH 3 четырех моделей - MACH 3/100, MACH 3/120; МАСР 3/122, MACH 3/125, предназначенные для изготовления труб диаметром 100-1200 мм и длиной 1-2,5 м.
Для всех четырех моделей характерны следующие особенности: короткий производственный цикл, полностью автоматизированный режим производства, быстрая и легкая смена оборудования, низкие производственные затраты, высокое качество и широкий ассортимент изделий, а также высокая производительность. Станок-автомат модели МАСН 3/100 с загрузочной воронкой для бетона предназначен для изготовления труб круглого сечения и профильных труб с соединением внакрой или раструбом длиной 1 м и диаметром 100-1000 мм. Общая установленная мощность составляет 26 кВт, из которых потребляется всего 19 кВт.
Станок-автомат модели МАСН 3/120 с подачей бетона ленточным конвейером предназначен также для изготовления труб диаметром 100-1200 мм и длиной до 1 м.
Станок отличается универсальностью. Кроме обычных круглых или профильных труб с соединением внакрой или раструбом, на станке можно изготавливать разные виды бетонных изделий типа бордюрных камней, труб квадратного сечения. При изготовлении раструбных труб можно производить изделия разного диаметра в одном производственном цикле. Это имеет большие преимущества в условиях, когда не требуется много труб одного диаметра и когда желательно снизить первоначальные капиталовложения в производство.
Применение для подачи и распределения бетона ленточного конвейера с приводом от гидромотора позволяет обеспечить более последовательный и точный контроль за работой и дает возможность производить трубы разной толщины. Причем подача бетона в формы в виде непрерывной загрузки и постоянной вибрации способствует лучшему качеству изделий.
Станок управляется одним оператором. Предварительная сборка форм и вибросердечников производится на площадках, стоящих на упругих опорах.
Станок-автомат модели МАСН 3/122 предназначен для производства вибропрессованных раструбных, круглых, овальных и других профильных труб диаметром 200-1200 мм и длиной до 2 м. Станок разработан на основе трубоформовочной машины МАСН 2/2, которая работает на многих дозаторно-смесительных установках. Основными особенностями станка является электронная система контроля и управления. Предварительная сборка сердечников и форм осуществляется на площадке с упругими опорами. Бетон подается ленточным конвейером с электронной системой контроля качества. Управление машиной в течение производственного цикла и транспортировка труб осуществляются одним оператором.
На станке-автомате этой модели можно также изготовлять одновременно трубы разного диаметра, трубы с арматурой и без нее, специальные бетонные изделия, а также при использовании соответствующего оборудования трубы "промежуточной" длины. Расход электроэнергии составляет 52 кВт. Станок-автомат модели МАСН 3/125 имеет те же технические характеристики, что и станок-автомат модели МАСН 3/122 с той только разницей, что он производит трубы диаметром 200-1200 мм длиной до 2,5 м. Кроме вышеописанных станков фирма "Mario Croci & Figli" выпускает лопастные мешалки, способные в зависимости от размера барабана выдавать от 0,3 до 1,4 м 3 бетонной смеси примерно за 2 минуты, а также многопрограммные объемные и весовые дозаторные устройства для бетона с дозировкой цемента, системой электронного регулирования подачи воды и раздачей отдозированной бетонной смеси с помощью движущейся вверху по рельсам бадьи или с помощью ленточного конвейера.
Управление всеми процессами на дозаторной установке от момента выбора заполнителя до раздачи бетонной смеси в машины производится электронной системой управления, снабженной датчиками и другими приборами, причем нужный состав смеси можно выбрать и без вмешательства оператора. Однако, когда такая сложная система управления не требуется, можно управлять дозаторной установкой вручную или она может работать в полуавтоматическом режиме в зависимости от нужд заказчика.
Автоматизированная технологическая линия для производства декоративных плит Legenda фирмы "Lori" (Италия)
Фирма "Lori" является новым объединением двух фирм - "Longinotti" и "Ricambi". Она создала на базе вибропресса Unimatik 1050-1050>
Вибропресс имеет гидравлическую станцию с двигателем мощностью 15 кВт, два вибратора с установленной мощностью по 7,5 кВт и два - по 5,5 кВт.
На рис. 1 представлена схема технологической линии Legenda. От вибропресса отформованные изделия выталкиваются на ленточный цепной конвейер, который подает их к шаговому подъемнику. Тяговая цепь подъемника, перемещаясь в вертикальном направлении, набирает штабель. Вильчатый погрузчик забирает набранный штабель изделий и отвозит в камеру термопропарки. После термопропарки тот же вильчатый погрузчик возвращает штабель пропаренных плит к снижателю. Снижатель производит действие, обратное штабелированию, выдавая изделия на ленточно-цепной конвейер для пакетирования. Пакет изделий составляется с помощью захвата на рольганге. Кантователь разворачивает пакет вдоль рольганга для удобства съема автопогрузчиком, который отвозит пакеты на склад готовой продукции. При составлении пакета захват приподнимает изделия, освобождая поддон, который возвращается к прессу, очищаясь по пути своего движения скребком. Масса загружается из бетоносмесителя через лоток в бетоноукладчик, а из него в мерный ящик пресса, в нижней части которого лежит поддон. При движении к прессу мерный ящик сдвигает отформованное ранее изделие вперед, а затем после формования возвращается в исходное положение. Сырье хранится в приемных бункерах и цементном силосе. Сырье из расходного бункера в бетоносмеситель подается скипом, а цемент - пневмовинтовым питателем.
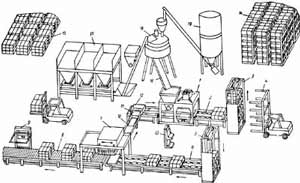
Рис. 1. Автоматизированная технологическая линия для производства декоративных тротуарных плит модели Legenda фирмы "Lori" (Италия): 1 - вибропресс; 2, 6 - ленточно-цепные конвейеры; 3 - шаговый подъемник для набора штабеля; 4 - вильчатый автопогрузчик; 5- шаговый снижатель для разбора штабеля; 7 - захват; 8 - рольганг; 9 - кантователь; 10 - поддон; 11 - скребок; 12 - мерный ящик; 13 - пульт управления; 14 - термопропарочная камера; 15 - склад готовой продукции; 16 - питатель; 17 - приемный бункер; 18 - бетоносмеситель; 19 - цементный силос.
Евгений МАРГАЙЛИК, инженер и патентовед ВОИР
Строительство и недвижимость. Статья была опубликована в номере 07 за 1999 год в рубрике дороги