Технологии и оборудование фирм Европы для изготовления бетонных изделий для дорожного строительства
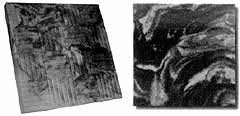
Рис. 1. Образцы плиток типа Reolit Optima.
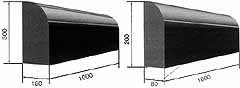
Рис. 2. Образцы дорожного и тротуарного бордюрных камней.
НОВЫЙ СПОСОБ ИЗГОТОВЛЕНИЯ БЕТОННЫХ ПЛИТ REOLIT OPTIMA ФИРМЫ "FEREINIGE REOLIT OPTIMA" (ФРГ)
Фирма "Fereinige Reolit Optima" изготовляет новым способом бетонные блоки, которые разрезаются на плиты типа Reolit Optima толщиной 1,3, 2 и 3 см. Получаемые плитки можно использовать для покрытия полов, стен и лестниц, а также для обрамления окон, для крышек столов, обеспечивая дизайнеру различные возможности для улучшения комфорта в помещениях (см. рис. 1). Наряду с небольшой толщиной и удобством придания определенной формы, а также повышенной точностью получаемых размеров, плиты бетонных блоков обладают увеличенной плотностью материала до 2,5 г/см3, прочностью при сжатии - до 90 Н/мм2 и прочностью на растяжение при изгибе - 6,6 Н/мм2. Благодаря небольшому износу этот материал относится к классу твердости I.
Использование вакуумной техники в сочетании со специальным способом виброуплотнения позволило получать качественное уплотнение изделий, в которых почти не имеется воздушных пор.
Технологический процесс изготовления плиток включает в себя следующие производства: подготовку материалов, изготовление блоков и их обработку. Производство блоков состоит из операций: подготовка смеси, формование, вакуумное уплотнение, твердение, обработка водой и складирование. В обработку блоков входит подготовка поверхностей, шлифование, распиловка, калибрование и упаковка.
Смесь, приготовленная на основе белого цемента с очень низким водоцементным отношением (по технологии фирмы "Dyckerhoff", разливается в формы размерами 3,08х1,25х0,8 м. Для смесителя вместимостью 1500 л требуется три загрузки смеси.
Формы перемещаются по направляющим к смесителю, от него возвращаются в вакуумный барабан и здесь закрепляются.
Вакуумный барабан вращается в течение 10 минут вокруг продольной оси. При этом указанные три загрузки превращаются в гомогенную смесь, а 90%-ный вакуум почти полностью устраняет воздушные поры.
По окончании процесса вращения вакуумный барабан опускается на вибрационный стол и соединяется с ним с помощью шести гидроцилиндров усилием 10 т в единый блок.
Для лучшего уплотнения такого большого количества бетона с низким водоцементным отношением при сохранении вакуума в камере, чтобы практически были устранены все воздушные поры, необходима очень высокая интенсивная вибрация.
Вибрационный стол, вакуумный барабан (камера), форма и бетон образуют 15-тонную тяжелую массу, которая колеблется с ускорением 4g. Вибрационная установка фирмы "Knauler" подвергает указанную массу воздействию вертикальных колебаний под действием центробежной силы величиной в 60 т.
При изменении амплитуды частота вибрации установки с гидравлическим приводом может максимально изменяться до 36 Гц.
В настоящее время такая установка является самым крупным уплотнителем бетона в мире. Время уплотнения составляет 4-5 мин. Затем барабан снова поднимается и открывается, направляющие обеспечивают выход тележки с формой к месту твердения бетонных плиток, где бетонный блок и форма орошаются водой, и через сутки устраняется опалубка. Подготовленный блок помещается в резервуар с водой и находится там в течение 20 суток, затем складируется во влажном состоянии. Только после этого блок обрабатывается.
Первой операцией обработки является подготовка поверхности. В зависимости от требуемой толщины блок разрезается на плитки толщиной 1,3, 2 и 3 см. Для этого предусмотрены три установки фирмы "Breton". До последующей операции нарезанные плитки хранятся на промежуточном накопителе в вертикальном положении.
На трех шлифовальных установках фирмы "Breton" плитки предварительно шлифуются, затем укладываются и сверху подогреваются для ускорения твердения с целью окончательного шлифования и последующего полирования. Подготовленные плитки разрезаются, упаковываются и доставляются на место укладки. Применение дозированных цветных наполнителей позволяет получать плитки различных оттенков.
Оборудование для изготовления бетонных блоков
Завод английской фирмы "Concrete Masonry Ltd." в г. Сент-Хеленс производит легкие и плотные бетонные блоки, плитняк, бордюрный камень и бетонные кирпичи. Для их изготовления используется сырье: пемза фракции 10-0 мм с содержанием влаги до 44%; зола с пода печей фракцией 75-0 мм; зола от сжигания распыленного топлива типа B - BS 3982 и обычный портландцемент. Пемза и зола поступают на завод объемом по 25 м 3 ежедневно и хранятся на открытой территории отдельно друг от друга.
Перед использованием в производственном процессе зола просеивается через сито с размером ячейки 12 мм. Больший по размеру материал дробится и снова просеивается. Мелкая и крупная зола размалываются и хранятся отдельно друг от друга рядом с загрузочным бункером.
Золя от сжигания распыленного топлива (типа от B до BS 3982) и обычный портландцемент доставляются ежедневно автотранспортом в насыпных емкостях и хранятся в трех силосах ирландской фирмы "Tyrone Engineering Ltd." (диаметром 3 м и вместимостью каждый по 52 м 3). Каждый силос представляет собой цельносварную конструкцию из пластин толщиной 5 мм.
При необходимости агрегаты загружаются фронтальным погрузчиком с ковшом вместимостью 3 м 3 в наземный бункер, откуда они перевозятся челночным конвейером в хранилище и дозирующую установку, имеющую четыре бункера. Два бункера отведены для пемзы, один - для мелкой золы с пода печей и еще один - для золы крупных фракций (с пода печей). Выбор бункера осуществляется с панели управления, на которой отображается уровень заполнения каждого силоса.
Дозирование и смешивание осуществляется под управлением компьютера с автономного пульта управления. Компьютер содержит информацию о 50 различных смесях, и после набора на клавиатуре номера требуемой смеси начинается операция дозирования, последовательность которой обычно осуществляется циклами. При необходимости можно задать дозирование одной партии. Схема со светодиодами на панели управления указывает состояние установки и протекание процесса смешивания.
Необходимые материалы подаются на ленточное взвешивающее устройство с автотарированием до предварительно устанавливаемого предела. Три вида материалов из четырех бункеров взвешиваются в определенной последовательности. Взвешивающее устройство тарируется на нуль, соответствующий бункер разгружает на него свое содержимое до тех пор, пока масса материала не достигнет требуемой, причем при приближении к требуемой массе материал индексируется, после этого взвешивающее устройство опять тарируется на нуль для следующей массы материала. После дозирования всех трех компонентов любой перевес или недовес компенсируется при 50%-ной ошибке на следующей партии.
Портландцемент и зола от сжигания распыленного топлива поступают из своих силосов по винтовому транспортеру во взвешивающий бункер, взвешиваются последовательно, как и необходимые компоненты с такой же компенсацией перевеса или недовеса.
После дозирования материалы разгружаются с ленточного взвешивающего устройства в загрузочный ковш мешалки и затем подаются в мешалку вместе с цементом и золой. Добавление воды в смесь контролируется водомерной системой, расположенной также на автономном пульте.
Смешанный бетон разгружается из мешалки и подается по транспортеру сначала в бункер для хранения, а потом в бункер для бетона, расположенный над машиной для изготовления блоков. Конструкция бункера выполнена таким образом, что бетон находится все время в стабильном состоянии, в то же время поддерживается уровень его в бункере и обеспечивается подача необходимого количества бетонной смеси в машину для производства изделий.
Машина для изготовления блоков ирландской фирмы "KVM Type 80/90" имеет форму размером 920х1000 мм и поддоны размерами 940х1200 мм. Она работает в автоматическом режиме, причем ручная переналадка осуществляется с пульта управления или реализуется с малого пульта (дистанционный пульт управления).
Все операции заполнения формы и уплотнения смеси контролируются приборами. Изготовляемые изделия выполняются с отклонением по высоте до 1 мм и являются изделиями высокого качества. Блоки формуются вибрацией и давлением и укладываются на поддоны из твердых пород дерева по 18 штук за цикл. Мимика светодиодов показывает изменяющееся состояние установки, а светодиоды на панели сигнализации могут указывать на отклонения (например, на недостаточное или слишком высокое давление, малую или большую высоту формуемых блоков).
Сырые блоки с машины переносятся по роликовому транспортеру под вращающейся щеткой, которая очищает поверхности. По транспортеру поддоны с блоками поступают к подъемнику, который складывает их в стопы по 7 штук. Движущееся устройство с захватом переносит блоки в предварительно выбранную для обжига печь, работающую по автоматической стендовой системе обработки. На заводе имеются восемь печей, каждая длиной около 28,5 м может принимать 14 поддонов. Во время загрузки в печь сначала устанавливаются семь уровней поддонов (всего 210 поддонов). Затем при последующей загрузке устанавливаются еще семь уровней поддонов (еще 210 поддонов). Управление всеми операциями осуществляется компьютером с автономного пульта управления, обеспечивая установку поддонов с сырыми блоками на одном конце печи и выемку поддонов с обожженными блоками на другом ее конце. Когда загрузочное устройство на одном конце печи устанавливается в положение для загрузки семи поддонов, такое же устройство на другом коне печи готово к принятию семи поддонов обожженных блоков на выходе. Каждый слой поддонов внутри печи движется по боковым роликам, которые позволяют им перемещаться при загрузке на одном конце и удалении - на другом.
Разгрузочное движущееся устройство переносит обожженные блоки к опускающему устройству, которое подает поддоны к роликовому транспортеру. Партии поддонов с обожженными блоками перемещаются к захвату, который удаляет поддоны, берет 18 блоков и помещает их на пластинчатый транспортер. Пустые поддоны очищаются, переворачиваются и укладываются на поддоноприемник, установленный за машиной для изготовления блоков, готовый к следующему циклу производства.
Обожженные блоки перемещаются по пластинчатому транспортеру к карусели для заполнения вспененным материалом. С помощью захвата изделия загружаются в карусель и переносятся на накопительный стол, где укладываются в два ряда по десять блоков. Эти два ряда блоков загружаются захватом на один из 12 формовочных столов карусели. Затем карусель перемещается в следующее положение, где блоки заполняются вспененным материалом, после чего над ними закрывается заслонка, пока они не завершат один круг на карусели. Полиуретановая пена для этой операции производится расположенной здесь же машиной.
Цикл заполнения вспененным материалом производится следующим образом. Блоки перемещаются в первоначальное положение. Машина готовится к подаче вспененного материала, головка мешалки с четырьмя выпускными отверстиями устанавливается над первыми четырьмя блоками, затем вспененный материал впрыскивается в блоки, после чего следует короткий воздушный удар. Головка мешалки перемещается на следующие четыре блока, и цикл повторяется до заполнения всех блоков. Затем головка мешалки возвращается в первоначальное положение, где очищается для следующего цикла.
После заполнения 20 блоков заслонка формовочного стола вплотную прилегает к верху блоков, оставаясь в опущенном положении, пока карусель не повернется на одиннадцать положений. Затем заслонка поднимается, а блоки удаляются и помещаются еще на один накопительный стол, откуда они снимаются по 18 штук и опять укладываются на пластинчатый транспортер, готовые к переносу к куберу.
На посту укладывания в куб блоки устанавливаются на металлические поддоны, а затем в штабели высотой в четыре слоя, состоящие из 72 блоков. Металлический поддон является частью кольцеобразной системы, в которой поддоны могут устанавливаться в нужное положение и накапливаться как со штабелями, так и без, чтобы достичь производственной гибкости. Куб затем перемещается к обвязочной машине, где второй и четвертый ряды блоков обвязываются полипропиленовой лентой. Затем штабели перемещаются за пределы завода и удаляются погрузчиками с захватами для складирования.
Пористые блоки производятся таким же образом, за тем исключением, что на поддон укладываются 14 блоков и на карусели накапливается другое число блоков.
Оборудование для изготовления бетонных изделий фирмы "Lingl"
На швейцарском заводе в г. Балстале фирмой "Lingl" пущена в эксплуатацию новая производственная установка для изготовления из легкого бетона бетонных плотных и пустотелых блоков типа Bisoterm, а из тяжелого бетона - бордюрного камня, предназначенных для строительства наземных и подземных сооружений (см. рис. 2).
В состав установки входят формовочная машина модели Variomatic, погрузочные и транспортные устройства и устройства управления, включая и электронные, обеспечивающие автоматизированный процесс производства. Готовая бетонная смесь подается в бункер формовочной машины (высота бункера 50 - 300 мм, вместимость его составляет 3 м 3). У машины имеется регулируемая по высоте направляющая в виде колонны. Виброплощадка установки снабжена качающейся металлической опорой. Мощность вибрации переменная. Виброуплотнение различных изделий осуществляется за счет регулирования частоты колебаний, что обеспечивает равномерное распределение бетонной смеси и хорошее качество изготовляемых изделий, обладающих высокой прочностью на сжатие. Машина снабжена дозирующим устройством.
После виброуплотнения наружная поверхность точно установленных по высоте блоков выравнивается заглаживающим устройством с равномерно вращающимися валками. Форма, устанавливаемая на деревянном поддоне размером 1400х550х45 мм, заполняется бетонной смесью с помощью расположенной над ней бадьи.
Для перехода на изготовление других изделий формовочная машина имеет устройство для быстрой переналадки формы.
Машина снабжена устройством с гидравлическим цилиндром для контроля давления и устройством для контроля за утечкой масла. Быстрое и точное ориентирование стоек формы при сборке осуществляется с помощью специального приспособления.
Весь процесс изготовления изделий формовочной машиной осуществляется в автоматическом режиме с помощью программирующего устройства с памятью компьютера. Оно одновременно контролирует всю технику безопасности и выдает показания о возникающих ошибках на экран дисплея. Все распечатки производства можно воспроизвести на экране и напечатать после окончания работы. Таким образом документируется объем продукции и смеси, а также выпуск дефектных изделий. Обслуживание как ручного, так и автоматического режимов работ сконцентрировано на одном пульте управления. Перестановке вводимых данных препятствует кодовый выключатель. При отключении напряжения в сети программа, заложенная в память компьютера, сохраняется. В конструкцию машины заложены параметры, рассчитанные на большую производительность, длительную работу, на незначительный износ и короткий цикл изготовляемых изделий.
При производстве деталей со сложным профилем подача формы во время наполнения и уплотнения бетонной смеси осуществляется с помощью гидравлики. Вывод формы со свежеотформованными изделиями из машины и подача формы в машину осуществляет кривошипный механизм. Скорость вывода и подача форм регулируются в зависимости от изготовляемых изделий. Поддоны с уложенными на них отформованными изделиями с помощью цепного конвейера подъемником подаются на участок для снятия щетками цементной пленки. Затем каждые два поддона с изделиями устанавливаются в 12 рядов по 450 мм каждый передаточной тележкой на передвижную платформу, которая перемещает их в открытые необогреваемые места для твердения.
Управление всеми процессами транспортирования, включая подачу и вывоз изделий после твердения, производится электронным устройством. После твердения изделия цепным конвейером подаются для очистки. Здесь же встроенное портальное устройство маркирует блоки, которые затем подъемником устанавливаются на конвейер для пакетирования. Для кантования изделий на 90 или 180° применяется интегрированное опрокидывающее устройство. Установленные на палетах, упакованные в пленку пакеты автопогрузчиком транспортируются на склад готовой продукции.
Евгений МАРГАЙЛИК, инженер и патентовед ВОИР
Строительство и недвижимость. Статья была опубликована в номере 05 за 1999 год в рубрике дороги