Заводы и оборудование стран Европы по производству дорожных и строительных изделий
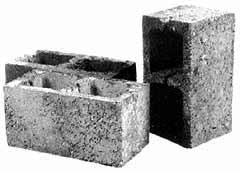
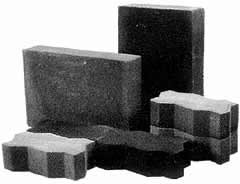
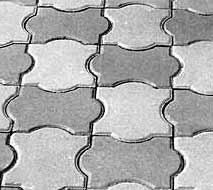
На заводе фирмы "Fries" в г. Эхинге, расположенном на территории в 20 000 м2, занято 30 человек. Продукцией завода являются: фасованные камни, плиты для оформления газонов, плиты с обработанной поверхностью для садов как с обнаженным заполнителем, так и с отшлифованной поверхностью. Для изготовления камней используются две машины и установка с циркуляцией поддонов фирмы "Schlosser". Для каждых двух формовочных линий предусмотрена сушильная с 12 сушильными камерами и каменной кладкой. Перед вывозкой изделий транспортной системой производится их пакетирование посредством обвязочной установки системы Titan.
Тротуарные и садовые плиты изготавливаются на двух прессах системы Henke, оборудованных установкой для циркуляции поддонов, а также на прессе системы Rino. Все три машины работают с одной сушильной линией. Пакеты камней штабелируются и грузятся двумя портальными кранами. Каждая машина для изготовления камней обеспечивается бетонной смесью от "своей" бетономешалки системы Schlosser LB вместимостью 1500 л. Машина для изготовления плит получает бетонную смесь от той же бетономешалки, которая приготавливает бетонную смесь для основания плиток, а также от двух бетономешалок вместимостью по 250 л, которые приготавливают бетонную смесь для облицовки. Высокий бункер вместимостью 500 м3 разделен на 16 камер.
Поверхность садовых плит обрабатывается шлифовальной установкой Shindler, оборудованной системой повторного использования воды, а также ленточным грязевым фильтром. Для обнажения фактурного слоя садовых плит используется пескоструйная установка производства фирмы "Schlik", оборудованная системой подачи и съема изделий, разработанной фирмой "Bauer" (см. рис. 1).
Завод в г. Тегинге фирмы "Linden" площадью 21 000 м2, на котором работают 97 человек, изготавливает мостовые и угловые камни, решетчатые камни для оформления газонов, изделия для укрепления откосов, а также углообразные стены. Кроме того, делают бордюрные камни и камни для обрамления цветочных клумб.
Для изготовления мостовых камней используются машина модели MAS AVP9000 и машина Variant 1-1300 фирмы "Henke", при этом происходит параллельная циркуляция поддонов. Изделия с производственного участка вывозятся грузоподъемными устройствами Vorlift с предварительным подъемом, а также транспортной тележкой, работающей в автоматическом режиме. Используются также пакетирующая установка этой же фирмы, система циркуляции сдвоенных вагонеток фирмы "Dmag" и установка фирмы "Signode" для вертикальной и горизонтальной обвязки готовых изделий. Твердение камней происходит в 12 сушильных камерах емкостью 5000 поддонов. Применяется также упаковочная машина фирмы "Franpack".
Штабелирование и погрузка производятся вилочными погрузчиками системы Linde с использованием поддонов или без них.
Для приготовления бетонной смеси служит смесительная установка MAS AHM 1500 вместимостью 1500 л. Бетонная смесь подается наклонными подъемниками с шестью высокими бункерами вместимостью по 120 м3, загрузка осуществляется с помощью элеватора. В другую машину для изготовления мостовых камней бетонная смесь подается бетономешалкой Remat типа РМ50. Обе бетономешалки можно заполнять добавками пневматическим путем. Смесительные установки размещены непосредственно над машинами для изготовления бетонных камней.
Другой завод фирмы "Linden" в г. Хеберсфельде, занимающий площадь 20 000 м2, с обслуживающим персоналом численностью 97 человек, выпускает мостовые камни с поверхностью, обработанной пескоструйной установкой, решетчатые камни для оформления газонов, изделия для укрепления откосов дорог, улиц, подходов к мостам, развязкам в разных уровнях, а также бордюрные камни и камни для обрамления цветочных клумб, палисадников, перемычки, в том числе для наземного строительства.
Для изготовления камней используется стационарная установка ВН30 производства фирмы "Schlosser", оборудованная системой циркуляции поддонов. При этом тележка для транспортировки камней работает в автоматическом режиме. Твердение изделий происходит в семи сушильных камерах с каменной кладкой и с использованием около 3000 поддонов.
Съем изделий производится автоматизированным пакетирующим устройством, которое подает изделия на установку с циркуляцией сдвоенных вагонеток. Доставка на склад и погрузка изделий производятся вилочными погрузчиками.
Для поверхностной обработки бетонных камней используется пескоструйная установка системы Schlik.
Элементы палисадников длиной до 1,2 м изготавливаются передвижной установкой Lenith. Перемычки делают вручную.
Завод в г. Таннзхаузене фирмы "Leitenmaier" изготавливает изделия для дорожного строительства, преимущественно бетонные мостовые, бордюрные, а также пустотелые бетонные камни (см. рис. 2).
Производство камней осуществляется двумя управляемыми с помощью компьютера машинами типа Variomatik фирмы "Hans Lingl". При этом применяются поддоны размерами 1400х1050 мм. Толщина изделий составляет от 50 до 100 мм. Для каждой из машин имеется по два запасных силоса: для бетона, предназначенного для основания камней, и для бетона, предназначенного для облицовки этих камней. Снабжение бетонной смесью обеспечивается ковшовым транспортером системы Dudik, одна из машин оборудована работающим в автоматическом режиме скребковым транспортером системы Elba.
Каждая из этих машин имеет свою систему циркуляции поддонов одинаковой конструкции. Установки оснащены обычным оборудованием - элеваторами или передаточными тележками для перемещения и снятия затвердевших изделий с сушильных стеллажей. За ними размещены механизмы для опускания изделий и пакетирующие захваты. Для обвязки изделий используются две установки Acme и Signode.
Бетонная смесь приготавливается и транспортируется различными способами. Одна из двух машин снабжается от центральной установки для подготовки заполнителей посредством установки для приготовления бетонной смеси. Последняя имеет бетономешалку принудительного действия системы Remat вместимостью 1000 л. Другая машина снабжается бетонной смесью от расположенного сборку от производственного цеха звездчатой дозировочной установки системы Elba. В этом случае бетономешалка принудительного действия системы Masa находится непосредственно над машиной (см. рис. 3).
Завод фирмы "Thurner&Sohn" в г. Унтербрунне занимает около 5000 м2 территории гравийного карьера. Он изготавливает бетонные мостовые камни.
Для изготовления камней используется стационарная машина с многослойной укладкой типа 400-5 фирмы "Knauer", управляемая электроникой. Машина оборудована двумя бункерами для бетонной смеси, предназначенной для облицовки камней и для их основания. Поддон с уложенными на него камнями выталкивается на роликовый транспортер. Вилочный погрузчик грузоподъемностью 4 т производства фирмы "Linde" снимает поддон и ставит его на пол для твердения. Дальнейшая транспортировка затвердевших камней, собранных в пакеты, производится также вилочными погрузчиками.
После съема поддона автоматически производится вертикальная и, если необходимо, горизонтальная обвязка пакетов камней. Пакеты бетонных камней на открытую площадку вывозятся пластинчатым транспортером. Операции штабелирования и погрузки пакетов камней на открытой площадке выполняются вилочными погрузчиками с захватами, перемещающимися в горизонтальном положении.
Смесительная установка вместимостью 750 л обеспечивает машину для изготовления камней бетонной смесью, предназначенной как для изготовления бетонного основания камней, так и для прессования облицовочного слоя. Установка оснащена устройством для контроля влажности и автоматикой для подачи воды. По ленточным транспортерам бетонная смесь подается в бункеры машины для изготовления камней. Совместно со смесительной установкой работают четыре бункера для заполнителей, расположенные ниже уровня пола, с полезным объемом по 35 м3. При этом дозировка по объему и по весу производится в подъемной бадье.
Оборудование для нанесения теплоизоляционного покрытия на бетонные блоки
Английская фирма "Product Handling" разработала и изготавливает оборудование для нового способа нанесения покрытия на поверхность бетонных блоков для повышения их теплоизоляционных свойств. В качестве покрытия используется полиуретановая пена, подаваемая в форму под давлением.
При таком способе облицовки поверхности форма для нанесения изоляционного материала образуется самим блоком и частями оборудования, которые вначале занимают рабочее положение для нанесения покрытия литьем под давлением, а затем переходят в открытое положение и освобождают готовый блок для схода с конвейера. Важной особенностью предлагаемого оборудования является возможность сохранения прямоугольной формы облицованных поверхностей блоков, отсутствие необходимости обработки его кромок на конус при высвобождении из формы.
Для нанесения покрытия бетонные блоки пропускаются через облицовочную машину на ленточном транспортере, а формообразующие части машины занимают смежное с блоком положение, блокируются с транспортером и образуют полую форму, в которую под давлением подается изоляционный материал, после чего полость закрывается сверху крышкой. По окончании операции форма открывается, указанные выше части отводятся от транспортера, и бетонный блок с нанесенным на него покрытием освобождается и сходит с транспортера.
Формообразующие части машины монтируются на парных звеньях сдвоенных цепных транспортеров. Каждая пара звеньев имеет на своем "ведущем" конце обращенные вверх вертикальные выступы со шпильками, на которых закреплены гибкие элементы, изготовленные из эластичного водоотталкивающего материала, например, резины. Эти элементы составляют часть литейной формы, в которой происходит нанесение изоляционного материала на поверхность блоков. При установке эластичный формообразующий элемент перекрывает промежуток между прилегающими сбоку сдвоенными транспортерами, причем его толщина выбирается таким образом, чтобы размер блока в направлении движения транспортера и толщины формообразующего элемента был несколько больше расстояния между центрами звеньев цепного конвейера. Формообразующие элементы, между которыми зажимаются блоки, должны находиться как можно ближе друг к другу при горизонтальном (или продольном) движении транспортера (конвейера) и открываться после того, как звенья обогнут звездочку или другие ведущие колеса на концах конвейера. Раскрытие формообразующих элементов обеспечивает возможность подачи необлицованных блоков на вход и удаление уже облицованных блоков на противоположном конце конвейера.
Описанные выше эластичные формообразующие элементы составляют передние и задние кромки формы для каждого обрабатываемого блока. Для ввода в рабочее положение боковых элементов на внутренних поверхностях прилегающих параллельных звеньев устанавливаются продольные пластины на шарнирах, на которых смонтированы подушки, образующие боковые элементы литейной формы. Как и концевые (торцевые) подушки, они выполнены эластичными и надежно фиксируются на боковых элементах (или кромках) торцевых подушек формы и верхней части необлицованного блока.
Перемещение шарнирных боковых пластин и, следовательно, закрывание и открывание боковых частей формы достигается путем установки роликов на "внешней" поверхности каждого бокового элемента и подшипников на кулачке соответствующей конфигурации.
С помощью описанного выше механического устройства необработанный покрытием блок, лежащий боком на отдельном подающем конвейере, устанавливается между параллельными звеньями цепного конвейера, эластичные подушки, перемещаясь, образуют четыре стороны полой формы, а верхняя (лицевая поверхность) бетонного блока образует ее основание.
После установки блока в форму подается под давлением точно дозированная порция теплоизоляционного материала, например, жидкого полиуретана с пенообразователем. Процесс отвердения пенообразной изоляции и сцепления ее с поверхностью блока занимает около 3 минут, причем для ускорения химической реакции твердения имеется устройство, закрывающее верхнюю часть формы.
Закрывание формы сверху происходит за счет прохождения бетонного блока с четырьмя формообразующими элементами под "закрывающим форму" транспортером, оснащенным несколькими нагруженными пружинами подушками, которые обеспечивают герметичное соединение с верхними кромками формообразующих элементов. Подушки имеют обработанную поверхность или покрытие, предотвращающее прилипание пены. Для покрытия можно использовать алюминизированную пленку (или ей подобную), которая в результате прохождения между "закрывающим форму" транспортером и верхними кромками полости формы склеивается с полиуретановой пеной. Продолжительность закрытого состояния формы зависит от длины и скорости движения транспортеров. Когда бетонный блок с нанесенным на него покрытием выходит из-под "закрывающего форму" транспортера, изоляционный материал уже затвердевает и прочно соединяется с поверхностью блока. Пена не приклеивается к закрывающим форму подушкам, которые отходят от обработанного блока в обратной последовательности. Резак гильотинного типа рассекает алюминизированную пленку между блоками и после покрытия теплоизоляционным материалом блоки освобождаются и удаляются с транспортера.
Обработанные блоки сходят с ленточного транспортера торцом вперед и поступают на приемный транспортер, на котором они с помощью пресса закатываются алюминизированной лентой поверх кромок облицованного блока. По мнению специалистов этой английской фирмы, сохранение пленки на облицованном блоке повышает его теплоизоляционные свойства и увеличивает пожарную безопасность.
Так как цепной ленточный транспортер, на котором движется бетонный блок, регулируется относительно цепного конвейера, то создается возможность изменять глубину полости формы в соответствии с конкретными потребностями и наносить изоляционное покрытие на бетонные блоки на различную глубину, что также является одним из преимуществ данного способа по сравнению с существующими.
Механическое устройство регулирует оборудование в соответствии с производственными потребностями.
Евгений МАРГАЙЛИК, инженер и патентовед ВОИР
Строительство и недвижимость. Статья была опубликована в номере 02 за 1999 год в рубрике дороги