Резервы оптимизации скрыты в малом
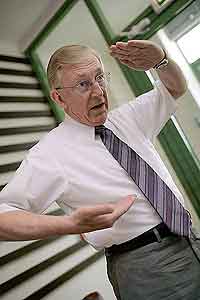
Системы бережливого производства
Принципы «Лин» (от английского lean production - бережливое производство) и раньше были известны многим руководителям, но особую актуальность система приобретает сегодня. Существует немало других аналогичных концепций: например, японская философия непрерывного улучшения «кайдзен». В СССР к таким принципам можно было бы отнести теорию научной организации труда, к сожалению, мало реализованную на практике.
Первопроходцем во внедрении принципов «Лин» стал японский концерн Toyota. Здесь уже на протяжении 40 лет занимаются совершенствованием своей производственной системы. В основе принципа бережливого производства в данном случае находятся улучшения, которые внедряются постоянно, каждый рабочий день, а не только в кризисные времена.
Независимо от определения, суть бережливого производства сводится к оптимизации процессов за счет устранения всех видов потерь. К их числу относят: лишние материально-производственные запасы, лишние движения, перепроизводство, ожидание в очередях, нерациональное транспортирование и расходы, связанные с исправлением брака. Постепенно «Лин» укрепляется в России и на всем постсоветском пространстве.
Однако переход на систему бережливого производства – дело далеко не простое. Процесс состоит из двух направлений. Первое нацелено на понижение себестоимости продукции и увеличение производительности труда. Второе представляет собой так называемую философию совершенствования, которая заключается в том, чтобы сотрудники постоянно развивались и применяли в своей работе новые подходы и технологии.
Использовать любые возможности для улучшений
Переход организации к бережливому производству на Западе часто поддерживает государство, создавая, например, специализированные образовательные центры. В России и СНГ подобная практика пока отсутствует. Зато в Москве, Санкт-Петербурге, Владивостоке и других городах работают японские центры, где слушатели могут пройти курс по основам внедрения «Лин».
Отечественные компании также готовы помочь свои партнерам. Так, в компании Проплекс запустили широкомасштабную программу, призванную помочь снизить расходы производителей светопрозрачных конструкций. Ее специалисты готовы выехать на производство, чтобы на месте определить внутренние резервы экономии, рассказать о практике оптимизации аналогичных производственных мощностей. Проплекс накопил богатый опыт проведения производственного аудита заводов-переработчиков и разработки уникальных рекомендаций по уменьшению затрат.
Специалисты по оптимизации производства рекомендуют идти от простого к сложному. Особенно впечатляет то, что подобные меры часто не требуют вообще никаких затрат – нужно лишь навести порядок. Компании необходимо разложить все свое производство на составляющие «детали» и рассмотреть каждую из них на предмет улучшения.
Замечательный пример приводит известный Лин-эксперт Майкл Вейдер. На одном предприятии стоял пресс весом в 20 тонн, который делал кругляши из квадратных заготовок. При производстве продукции определенного типа этот пресс необходимо было убрать и поставить новый. Замена занимала 30 минут. И считалось, что это очень быстро, ведь пресс, который необходимо было переоснастить, - тяжеленный. После недельной работы над оптимизацией процесса операция стала занимать только пять минут. Почему? Потому что компания ранее недооценивала свои возможности. Эксперты же считают, что их нужно постоянно пересматривать и выискивать малейшие возможности для улучшений.
Совершенный коллектив
Даже если изначально были предприняты огромные усилия по оптимизации производства, вновь следует вспомнить об опыте Toyota и других японских компаний: нет предела улучшениям. Там эта концепция становится философией всей компании и каждого ее сотрудника. Действует этот принцип и в России.
Как правило, чтобы «процесс пошел», устанавливается система поощрений – как материальных, так и нематериальных. Например, в цехах «Челябинского тракторного завода» регулярно проводятся смотры-конкурсы «Самый чистый» и «Самый грязный участок». Как бы наивно не выглядели эти инициативы, они дают свой положительный результат: больше порядка – легче найти резервы для снижения затрат.
Свои плоды приносит и материальная мотивация. Например, на «КАМАЗе» за подачу рацпредложения и его внедрение рабочий получает небольшую премию. Такой подход очень неплохо стимулирует сотрудников искать возможности для совершенствования производства. Помимо этого, согласно приказу президента «КАМАЗа», сотрудник не может быть уволен, если он активный участник системы улучшений.
Система материальных и нематериальных стимулов действует и в компании «Русские краски». В результате многие ее сотрудники уже озвучили свои рационализаторские идеи. Пример предложения – асбестовый шнур хранился в мотке в бачке и постоянно запутывался. Простое предложение установить деревянный барабан позволило значительно сэкономить время.
Как и в случае с производством, помочь работе с персоналом могут партнеры компании. Им вполне по силам обучить коллег всем тонкостям эксплуатации оборудования, его настройки и обслуживания. Оптимизировать все этапы от создания продукта до его продажи, повысить квалификацию исполнителей помогают также обучающие семинары для представителей производств, монтажников, а также продавцов конечной продукции.
Очень важно, чтобы в процессе улучшений приняли участие все – он не может быть выборочным для отдельных категорий сотрудников. И особенно необходимо, чтобы первые лица компании инициировали и поддерживали все начинания.
Чтобы предприятие работало с максимальной эффективностью, придется руководителю самому «запачкать руки». Нужно идти на производство, в цеха, к рабочим, считает Майкл Вейдер. Нужно считать количество выпускаемой продукции, а не довольствоваться тем, что сотрудники заняты в течение всего рабочего дня. Важно, чем они заняты. К примеру, 60 процентов рабочего времени сотрудник производит изделия, 20 процентов тратит, чтобы починить то, что сломалось. Остальные 20 ничего не делает, он ждет инструкций. Очевидно, что, несмотря на стопроцентную занятость, это неэффективно. Только когда руководство компании готово к постоянным улучшениям, производство действительно станет бережливым. В противном случае все ограничится разовыми акциями, дающими лишь кратковременный эффект.
Экономический кризис – не только испытание, но и шанс для многих предприятий сделать свое производство более эффективным, снизить себестоимость продукции, сделав ее более конкурентоспособной. Конечно, скептики могут сказать, что у нас японские и европейские методики не работают. Но ряд отечественных компаний уже доказали обратное. Более того, у нас есть преимущество перед иностранцами: наши резервы экономии гораздо больше, чем в тех странах, где бережливое производство внедряется уже много лет.
Юрий СТРОЕВ
Строительство и недвижимость. Статья была опубликована в номере 01 за 2010 год в рубрике мат. и тех.