О внедрении тульских оружейных традиций в вибропрессование
Тульская компания «Гевит» была создана в 1991 г. Основной целью создания компании являлось производство и реализация вибропрессованных бетонных изделий. Рынок сбыта только начинал формироваться. Через 5 лет руководством было принято решение организовать машиностроительную компанию, производящую пресс-формы для всех типов вибропрессов. В 1996 г. началась история «Гевит» как научно-производственной компании.
Сегодня «Гевит» стремится использовать новейшие технологии для проектирования и производства оборудования для формования бетона. Конструкторско- технический отдел полностью переведен на компьютерное проектирование оборудования. Производственные мощности постепенно переходят на новое, более высокопроизводительное, оборудование и инструмент. А в 2007 г. в арсенале разработок компании «Гевит» появилась самая мощная в России автоматическая линия вибропрессования бетона. В конструкции вибропресса «Гевит-блок» применены давно известный принцип вибропрессования бетона и кинематика новейших артиллерийских систем. По существу, это пулемет, производящий тротуарную плитку. Конструктивно вибропресс предназначен для формования камней бетонных стеновых, блоков бетонных для сборно-монолитных перемычек, плит бетонных тротуарных, изделий для обустройства автодорог, элементов бетонных для сборно-монолитных перекрытий, камней бетонных бортовых и других изделий, изготовление которых возможно методом вибропрессования. Так как технология и техника не стоят на месте, конструкторы не стали слепо копировать ни российские, ни зарубежные прессы. Вибропресс оснащен системой облицовочного бетона, позволяющей формовать двухслойные изделия. Из цементно-песчаной смеси данный пресс формует изделия при В/Ц<0,3. При расходе цемента 330 кг на 1 м3 бетона (цемент марки ПЦ400Д20) получена прочность бетона 45 МПа. И это на песке с модулем крупности 2,1. Скорость движения дозатора составляет более 2 м/с. При объеме дозатора 0,3 м3 бетон доставляется в зону формования за 0,5 с. В этот момент укладки смеси (процесс вибродозирования) применяются низкие (30-40 Гц) частоты.
Во второй стадии уплотнения (вибропрессование) частота вибрации доходит до 100 Гц. Можно изменять частоту и амплитуду вибрации, включать в работу любой из четырех вибраторов и любую группу вибраторов. Последнее полезно при формовании разных изделий, отличающихся габаритами, на одном поддоне. Таким образом, достигаются наилучшие условия для уплотнения бетонной смеси. Система управления вибрацией позволяет регулировать частоту вибрации с пульта управления. Пригруз не жестко связан гидроцилиндром и всей рамой станка и не передает вибрацию через раму на фундамент. Давление пуансона на бетонную смесь регулируется в пределах от 0,05 до 0,5 МПа. При формовке пуансон вибропресса движется вниз по мере уплотнения смеси. В определенном положении срабатывает датчик положения пуансона, который формирует системе управления команду на завершение операции уплотнения и начало распалубки. На вибропрессе применен цифровой датчик положения, который формирует цифровой сигнал, что позволяет устанавливать высоту изделия с пульта управления. Кроме того, установлены четыре датчика высоты изделия. Вибропрессование прекратится только тогда, когда сработают три датчика высоты. Плотность отформованного бетона регулируется подбором режимов вибродозирования. В этом режиме можно изменять скорость движения и положение дозатора над матрицей, задавать количество ходов дозатора и ворошителя. Дозатор можно устанавливать над любым участком матрицы. Можно изменять время работы и скорость активного ворошителя. Аналогичный алгоритм работы на отечественных вибропрессах еще не применялся ни разу. Так как при передаче вибрации на бункер бетонная смесь может там уплотняться и в дальнейшем зависать, бункер стоит на виброизоляторах. На одном из заводов России вибропресс работает в составе линии с ямными пропарочными камерами, где транспортные операции выполняются мостовым краном. На другом заводе предусмотрена работа вибропресса в составе автоматической линии с напольными камерами ускоренного твердения бетона. Все транспортные операции выполняются автоматическими передаточными тележками, работающими в соответствии с циклом работы вибропресса. Предусмотрена автоматическая пакетировка изделий на транспортные поддоны.
Автоматическая линия на базе вибропресса «Гевит-блок» в комплекте с камерами выдержки представляет собой комплекс оборудования, позволяющий производить высококачественную бетонную продукцию в полностью автоматическом режиме. Для управления линией необходимо 3 человека. Система управления на базе промышленного контроллера программируется для производства широкой номенклатуры изделий и позволяет в максимальной степени исключить негативное влияние человеческого фактора. Свежеотформованная продукция из вибропресса поступает на деревянных поддонах по транспортеру в подъемник-накопитель, где накапливается в количестве 32 штук. Далее раздаточная тележка из транспортной группы забирает все поддоны и перевозит в свободную камеру выдержки. На транспортной группе установлен промышленный контроллер, который программируется на порядок размещения свежеотформованной продукции в свободных камерах и вывоза выдержанной продукции из занятых камер. Далее раздаточная тележка по программе вывозит выдержанную продукцию и перегружает в снижатель-накопитель, откуда по транспортеру поддоны по одному поступают на пост распалубки.
Автоматический пакетировщик с помощью гидравлического захвата собирает продукцию с поддона и перегружает на транспортный поддон, где укладывает по программе в нужное количество рядов (если необходимо — с поворотом на 180°). Транспортные поддоны с упакованной продукцией выводятся по транспортеру за пределы цеха для погрузки в транспорт. Технологические поддоны по замкнутому циклу с очисткой и переворотом поступают в вибропресс для повторения процесса формования. В связи с тем, что различная продукция (тротуарная плитка, бордюрный камень) формуется и пакетируется с различной скоростью, в линии предусмотрены буферные устройства для технологических поддонов (магазин-накопитель, магазин подачи, транспортер вывода пакетов поддонов).
Машина для рубки бетонных стеновых камней предназначена для получения одной или нескольких поверхностей стенового камня под рваный камень методом раскалывания между двумя ножами. Она состоит из силовой стойки, гидросистемы, нижнего ножа, верхнего сегментного ножа, упора с линейкой и пульта управления с электросхемой. Длина хода цилиндра — 300 мм, продолжительность одного цикла рубки — 3 секунды, длина верхнего ножа — 450 мм, нижнего — 585 мм. Максимальная высота раскалываемого изделия — 300 мм, минимальная — 60 мм, максимальная ширина раскалываемого изделия — 450 мм, минимальная — 160 мм. Рабочее давление гидростанции — 45 кгс/см2, усилие раскалывания — 90 кН. На силовой стойке рубильной машины установлены ножи и гидросистема, которая включает гидроцилиндр, насос с электродвигателями, масляный бак, фильтр и манометр. Нижний нож установлен неподвижно таким образом, что при раскалывании находится под изделием. Верхний нож перемещается в вертикальной плоскости гидроцилиндром. Конструктивно он выполнен из набора 9 сегментных ножей (по 50 мм), соответственно, 9 цилиндров и верхней полости, заполненной индустриальным машинным маслом. Через верхнюю полость перераспределяется давление раскола. Формируется линия раскола, определяемая неровностью раскалываемого камня. Максимальный перепад неровностей составляет 10 мм от средней линии. Крайние нижнее и верхнее положения ножа контролируются концевыми выключателями. Оба ножа находятся в одной плоскости. С одной стороны от ножа установлен упор с линейкой, предназначенный для фиксации ширины получаемого изделия. Раскалываемое изделие устанавливается вручную на подпружиненный стол и передвигается вплотную к упору. Направляющие, простирающиеся на 25 см по обе стороны от нижнего ножа, представляют собой сварную площадку и установлены на пружинах так, чтобы изделие могло проходить над нижним ножом, не задевая его. При подаче нагрузки через верхний нож (гидроцилиндр) площадка опускается, обеспечивая сближение ножей за счет сжатия пружин. Установка изделий на приемный стол производится вручную.
Кроме того, компания «Гевит» изготавливает пресс-формы для всех типов вибропрессов отечественного и импортного производства — HESS (Multimat RH250, 500, 600, 1000, 1500, 2000), MASA, Eurocompacta, Compacta, Marathon Rosacometta, Schlosser-Pffeifer, Henke, Besser, Omag, Adler, КРМ, БЗЛ, ВИП, Impianto, Poyatos, UF051, «Рифей», Zenith. Для изготовления применяются высококачественные стали и эффективные методы термопластической и термической обработки, что позволяет конкурировать с зарубежными производителями аналогичной продукции по срокам службы пресс-форм и качеству получаемых на них изделий. Компания производит пресс-формы для широкого спектра бетонных изделий (стеновые камни любой модификации, бордюрные камни всех типоразмеров по ГОСТ, в том числе криволинейных, тротуарные плиты любой модификации, дорожные изделия, изделия по чертежам заказчика). На сегодняшний день отлажена технология и производство пресс-форм для линий безопалубочного формования Prensoland S.A. (Tensiland), Echo, Техноспан, X-TEC. Формы изготавливаются из износостойкой стали нового поколения Hardox (Швеция), по свойствам превышающей отечественные марганцевистые стали и практически не имеющей аналогов. Высокие механические свойства металла Hardox потребовали применения современных технологий и импортного оборудования для изготовления данных форм (машина лазерной резки, программные листогибы, программное металлообрабатывающее оборудование, современный инструмент).
Поскольку началось сотрудничество «Гевит» с немецкой фирмой Lammers GmbH & Co KG, заказывая пресс-формы у «Гевит», клиент компании получает вкладыши производства Lammers, изготовленные по технологии производства немецких форм и фрезерованные на пятикоординатном станке. Поэтому высокие стойкость и точность исполнения вкладышей гарантируются.
Сергей ЗОЛОТОВ
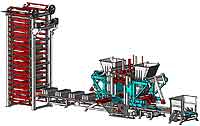
Во второй стадии уплотнения (вибропрессование) частота вибрации доходит до 100 Гц. Можно изменять частоту и амплитуду вибрации, включать в работу любой из четырех вибраторов и любую группу вибраторов. Последнее полезно при формовании разных изделий, отличающихся габаритами, на одном поддоне. Таким образом, достигаются наилучшие условия для уплотнения бетонной смеси. Система управления вибрацией позволяет регулировать частоту вибрации с пульта управления. Пригруз не жестко связан гидроцилиндром и всей рамой станка и не передает вибрацию через раму на фундамент. Давление пуансона на бетонную смесь регулируется в пределах от 0,05 до 0,5 МПа. При формовке пуансон вибропресса движется вниз по мере уплотнения смеси. В определенном положении срабатывает датчик положения пуансона, который формирует системе управления команду на завершение операции уплотнения и начало распалубки. На вибропрессе применен цифровой датчик положения, который формирует цифровой сигнал, что позволяет устанавливать высоту изделия с пульта управления. Кроме того, установлены четыре датчика высоты изделия. Вибропрессование прекратится только тогда, когда сработают три датчика высоты. Плотность отформованного бетона регулируется подбором режимов вибродозирования. В этом режиме можно изменять скорость движения и положение дозатора над матрицей, задавать количество ходов дозатора и ворошителя. Дозатор можно устанавливать над любым участком матрицы. Можно изменять время работы и скорость активного ворошителя. Аналогичный алгоритм работы на отечественных вибропрессах еще не применялся ни разу. Так как при передаче вибрации на бункер бетонная смесь может там уплотняться и в дальнейшем зависать, бункер стоит на виброизоляторах. На одном из заводов России вибропресс работает в составе линии с ямными пропарочными камерами, где транспортные операции выполняются мостовым краном. На другом заводе предусмотрена работа вибропресса в составе автоматической линии с напольными камерами ускоренного твердения бетона. Все транспортные операции выполняются автоматическими передаточными тележками, работающими в соответствии с циклом работы вибропресса. Предусмотрена автоматическая пакетировка изделий на транспортные поддоны.
Автоматическая линия на базе вибропресса «Гевит-блок» в комплекте с камерами выдержки представляет собой комплекс оборудования, позволяющий производить высококачественную бетонную продукцию в полностью автоматическом режиме. Для управления линией необходимо 3 человека. Система управления на базе промышленного контроллера программируется для производства широкой номенклатуры изделий и позволяет в максимальной степени исключить негативное влияние человеческого фактора. Свежеотформованная продукция из вибропресса поступает на деревянных поддонах по транспортеру в подъемник-накопитель, где накапливается в количестве 32 штук. Далее раздаточная тележка из транспортной группы забирает все поддоны и перевозит в свободную камеру выдержки. На транспортной группе установлен промышленный контроллер, который программируется на порядок размещения свежеотформованной продукции в свободных камерах и вывоза выдержанной продукции из занятых камер. Далее раздаточная тележка по программе вывозит выдержанную продукцию и перегружает в снижатель-накопитель, откуда по транспортеру поддоны по одному поступают на пост распалубки.
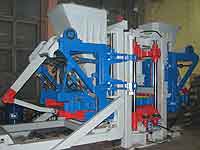
Машина для рубки бетонных стеновых камней предназначена для получения одной или нескольких поверхностей стенового камня под рваный камень методом раскалывания между двумя ножами. Она состоит из силовой стойки, гидросистемы, нижнего ножа, верхнего сегментного ножа, упора с линейкой и пульта управления с электросхемой. Длина хода цилиндра — 300 мм, продолжительность одного цикла рубки — 3 секунды, длина верхнего ножа — 450 мм, нижнего — 585 мм. Максимальная высота раскалываемого изделия — 300 мм, минимальная — 60 мм, максимальная ширина раскалываемого изделия — 450 мм, минимальная — 160 мм. Рабочее давление гидростанции — 45 кгс/см2, усилие раскалывания — 90 кН. На силовой стойке рубильной машины установлены ножи и гидросистема, которая включает гидроцилиндр, насос с электродвигателями, масляный бак, фильтр и манометр. Нижний нож установлен неподвижно таким образом, что при раскалывании находится под изделием. Верхний нож перемещается в вертикальной плоскости гидроцилиндром. Конструктивно он выполнен из набора 9 сегментных ножей (по 50 мм), соответственно, 9 цилиндров и верхней полости, заполненной индустриальным машинным маслом. Через верхнюю полость перераспределяется давление раскола. Формируется линия раскола, определяемая неровностью раскалываемого камня. Максимальный перепад неровностей составляет 10 мм от средней линии. Крайние нижнее и верхнее положения ножа контролируются концевыми выключателями. Оба ножа находятся в одной плоскости. С одной стороны от ножа установлен упор с линейкой, предназначенный для фиксации ширины получаемого изделия. Раскалываемое изделие устанавливается вручную на подпружиненный стол и передвигается вплотную к упору. Направляющие, простирающиеся на 25 см по обе стороны от нижнего ножа, представляют собой сварную площадку и установлены на пружинах так, чтобы изделие могло проходить над нижним ножом, не задевая его. При подаче нагрузки через верхний нож (гидроцилиндр) площадка опускается, обеспечивая сближение ножей за счет сжатия пружин. Установка изделий на приемный стол производится вручную.
Кроме того, компания «Гевит» изготавливает пресс-формы для всех типов вибропрессов отечественного и импортного производства — HESS (Multimat RH250, 500, 600, 1000, 1500, 2000), MASA, Eurocompacta, Compacta, Marathon Rosacometta, Schlosser-Pffeifer, Henke, Besser, Omag, Adler, КРМ, БЗЛ, ВИП, Impianto, Poyatos, UF051, «Рифей», Zenith. Для изготовления применяются высококачественные стали и эффективные методы термопластической и термической обработки, что позволяет конкурировать с зарубежными производителями аналогичной продукции по срокам службы пресс-форм и качеству получаемых на них изделий. Компания производит пресс-формы для широкого спектра бетонных изделий (стеновые камни любой модификации, бордюрные камни всех типоразмеров по ГОСТ, в том числе криволинейных, тротуарные плиты любой модификации, дорожные изделия, изделия по чертежам заказчика). На сегодняшний день отлажена технология и производство пресс-форм для линий безопалубочного формования Prensoland S.A. (Tensiland), Echo, Техноспан, X-TEC. Формы изготавливаются из износостойкой стали нового поколения Hardox (Швеция), по свойствам превышающей отечественные марганцевистые стали и практически не имеющей аналогов. Высокие механические свойства металла Hardox потребовали применения современных технологий и импортного оборудования для изготовления данных форм (машина лазерной резки, программные листогибы, программное металлообрабатывающее оборудование, современный инструмент).
Поскольку началось сотрудничество «Гевит» с немецкой фирмой Lammers GmbH & Co KG, заказывая пресс-формы у «Гевит», клиент компании получает вкладыши производства Lammers, изготовленные по технологии производства немецких форм и фрезерованные на пятикоординатном станке. Поэтому высокие стойкость и точность исполнения вкладышей гарантируются.
Сергей ЗОЛОТОВ
Строительство и недвижимость. Статья была опубликована в номере 48 за 2008 год в рубрике оборудование и инструмент