Для управления перерабатывающими станками от СТаТико не нужно специальной подготовки
Промышленная группа «СТаТико» из Подмосковья производит оборудование для переработки отходов — вертикальные и горизонтальные пакетировочные гидравлические прессы, компакторы, различные виды дробильных машин для бумаги, картона, ПЭТ-бутылок, пластика, а также мусоросортировочные заводы.
Оборудование «СТаТико» идеально подходит для утилизации и переработки любых отходов (брак пищевого производства, ТБО, макулатура, отходы полимеров, металла, текстиля, кожи, древесины), а также для компактирования полимерной и бумажной упаковки. Предлагаемая «СТаТико» испытанная технология обращения с отходами позволяет в 15 раз сократить занимаемые ими площади, во столько же раз снизить стоимость вывоза отходов за счет сокращения их объема, продавать прессованные отходы. Получаемые кипы разрешены для хранения пожарной инспекцией, экологами и СЭС. Небольшой утилизационный прибор соответствует всем необходимым техническим и экологическим нормам и может адаптироваться к особенностям любого производства. Станком может легко управлять человек без специальной подготовки. Пресс пакетирует кипу весом 30-500 кг, обвязанную проволокой или капроновым шпагатом, после чего она подготовлена к хранению и транспортировке. Оборудование «СТаТико» изготавливается из импортных
комплектующих.
Прессы для макулатуры, ПЭТ-бутылок, поролона, пленки, пластика, текстиля, кожи, металлических бочек
Пресс «Малыш» (технология PST Group, Канада) с боковой загрузкой (до 30 м3 в смену) используется на предприятиях с небольшим и средним количеством отходов (магазины, рынки, торговые и бизнес-центры, гостиницы, кинотеатры, выставочные и развлекательные комплексы, больницы, станции техобслуживания, типографии, коммунальные службы, дворцы спорта, приемные пункты вторсырья). Серийное производство прессов осуществляется по технологии Press System Technology на современном оборудовании от Amada и Evereising. Движущиеся детали пресса недоступны во время работы, а все открывающиеся люки блокируются до тех пор, пока не завершается рабочий цикл. Большое загрузочное окно позволяет загружать картонные коробки и объемные мешки с мусором. Выгрузка спрессованной кипы механизирована. Быстрая обвязка кипы осуществляется через технологические отверстия специальной лентой или веревкой (промышленная группа поставляет соответствующий обвязочный материал). Пресс работает при низких (до -45оС) температурах воздуха. Для его эксплуатации достаточно навеса от дождя, так как, в отличие от импортных прессов, он не комплектуется электроникой. Пресс устанавливают в небольших помещениях с ограниченной высотой потолка (подвалы, железнодорожные контейнеры) рядом с источником мусора, что значительно сокращает время транспортировки отходов. Для установки пресса с учетом площади его обслуживания требуется 1,5 м2, а для складирования 1 т прессованных отходов — 1,8 м2. При прессовании отходов вес кипы составляет в случае макулатуры до 70 кг, полимерной пленки, пластмассовых ящиков — до 80 кг, ТБО — до 80 кг. Вес можно регулировать, уменьшая или увеличивая высоту кипы. Пресс «Крепыш» с боковой загрузкой (до 50 м3 в смену) изготавливается по той же технологии и предназначен для организаций со средним количеством отходов (супермаркеты, рынки, предприятия пищевой, текстильной и легкой промышленности, типографии, торговые и бизнес-центры, выставочные, развлекательные и гостиничные комплексы, склады, таможенные терминалы, вокзалы, аэропорты, переработчики вторсырья). Работает при температуре до -30°С. Пресс устанавливают рядом с источником мусора, что сокращает время на транспортировку отходов. Для установки пресса с учетом площади его обслуживания требуется 1,5 м2, а для складирования 1 т прессованных отходов — от 1,0 м2 (в зависимости от вида отходов). Вес готовой кипы составляет 30-200 кг, объем — всего 0,34 м3. Кипа макулатуры может весить до 150 кг, полимерной пленки, пластмассовых ящиков — до 160 кг. Вес можно регулировать, уменьшая или увеличивая высоту кипы. В еврофуру объемом 82 м3 (13,6х2,45х2,45 м) загружается 198 кип (при правильной укладке). Все остальные параметры аналогичны таковым пресса «Малыш».
И самый большой пресс — «Профи PST 20» (с верхней загрузкой для любых отходов объемом до 150 м3 в смену) — предназначен для организаций с любым количеством отходов (торгово-развлекательные и бизнес-центры, гипермаркеты, предприятия пищевой, текстильной и легкой промышленности, производители тары и упаковки, полиграфические и складские комплексы, выставки, гостиницы, вокзалы, аэропорты, переработчики вторсырья). Вместо объемных контейнеров или других форм хранения отходы загружаются непосредственно в пакетировочный пресс. Для установки пресса с учетом площади его обслуживания требуется 3,5 м2, а для складирования 1 т прессованных отходов — от 0,8 м2 (в зависимости от вида отходов). Объем кипы — 0,62 м3, вес кипы макулатуры составляет до 400 кг, полимерной пленки, пластмассовых ящиков, ПЭТ-бутылок — до 350 кг, поролона — до 200 кг. Вес можно регулировать, уменьшая или увеличивая высоту кипы. При правильной укладке в еврофуру объемом 82 м3 (13,6х2,45х2,45 м) загружается 96 кип.
Дробилки «Бобер»
Дробилки для пластиковых бутылок, полимерной пленки, плетеных мешков (big bags), пластика производительностью 250-650 кг/ч оснащаются роторами и ножами из высококачественной стали, имеющими большой срок службы. Особая конструкция роторов (ножи v-образной формы) обеспечивает высокую эффективность переработки любых эластичных и объемных материалов, а также полимерной пленки. Сетка-фильтр легко устанавливается и снимается для очистки или замены. Диаметр ячеек подбирается индивидуально и зависит от требований заказчика. Двигательный отсек дробилки закрывается звукоизолирующим кожухом. Двойная система уплотнителей и надежно предохраняет механизмы привода от загрязнения, и защищает двигатель от перегрузок. Загрузочная горловина дробилки оборудована защитным устройством для обеспечения безопасности оператора. Дробилки универсальные производительностью от 150 до 1000 кг/ч предназначены для измельчения резины, кожи, дерева и полимеров (ПЭТ-преформ, пластиковой посуды, ведер, тазиков, хозяйственных товаров, ящиков и бутылочек, корпусов аккумуляторов, пищевой упаковки, упаковки продуктов химической промышленности и бытовой химии, детских игрушек, пластиковых медицинских отходов. Ножи этих дробилок изготавливаются из высококачественной инструментальной стали. Они очень прочные, имеют большой срок службы, их расположение можно регулировать, а сами ножи при необходимости многократно затачивать. Основание для ножей изготавливается из стали, позволяющей избежать износа и разломов. Зазоры между двумя соседними лезвиями — менее 0,05 мм, что предотвращает попадание пыли от измельчаемого сырья на дно основания подшипника и не приводит к перегрузке электродвигателя. Такая дробилка оснащается подшипниками, воспринимающими большую нагрузку, и камерой дробления с двойным слоем шумопоглощающей изоляции. Корпус дробилки не изнашивается из-за вибрации и воздействия обрабатываемого сырья даже после очень длительного срока эксплуатации. Конструкция дробилки обеспечивает легкий доступ к фильтрующей сетке и ножам ротора. Имеется предохраняющий рычаг для безопасной фиксации лезвий во время чистки или наладки. Электродвигатель оборудуется устройством, предотвращающим его перегрузку, и системой защиты, связанной с электропитанием, что гарантирует безопасность.
Шредеры
Однороторные шредеры (измельчители) предназначены для предварительной переработки древесины (паллеты, шпалы), отходов пластмасс в виде пленки, полипропиленовых и полиэтиленовых мешков, сливов (слитков), получаемых при запусках экструдеров, крупногабаритных отходов (трубы, бочки, короба, ящики), которые невозможно измельчить сразу в дробилке. С помощью гидравлического прессовочного устройства материал измельчается максимально эффективно, нагрузка на измельчающий ротор контролируется автоматически, режим работы пресса зависит от перерабатываемого материала и задается на пульте управления шредером. Ротор оборудуется системой реверсивного движения, что при превышении нагрузки свыше заданной оператором величины позволяет автоматически включить обратный ход, избежав повреждений ножей и двигателя. Ножи изготавливаются из высококачественной стали D2 и имеют 4 рабочие поверхности. При затуплении одной из поверхностей переточка ножа не требуется — его достаточно повернуть на 90°. Таким образом, срок службы ножей увеличивается в 4 раза. Такая конструкция ножей позволяет уменьшить и распределить нагрузку на ротор, уменьшить расход электроэнергии и увеличить производительность. Привод оснащен устройством плавного пуска, что позволяет снизить нагрузку на ножи, ротор и двигатель в момент пуска, если в камере остался непереработанный материал.
Линия переработки и гранулирования окрашенных полиэтиленовых и полипропиленовых пленочных отходов (двухшнековый экструдер)
Двухшнековый (двухкаскадный) гранулятор PST 250 предназначен для переработки и гранулирования поьлиэтиленовой и полипропиленовой пленки и вспененных материалов. Загрузочный бункер объемом 1,75 м3 (нержавеющая сталь) оснащается винтовым загрузчиком (7,5 кВт) с регулируемой скоростью для равномерной загрузки. Первый экструдер оснащается пассивной и активной (вакуумной) системой дегазации, второй имеет пассивную дегазацию. Это очень важно при работе со сложными (влажными, окрашенными) отходами — пары и газы, выделяемые при переработке, активно удаляются. Шнеки и цилиндры изготавливаются из высококачественного материала 38CrMoALA с азотной обработкой (толщина покрытия 0,7 мм) и степенью твердости HV950- 1050. Редукторы приводов изготавливаются с усиленными зубцами с азотной обработкой для интенсивной работы и большим крутящим моментом с низким уровнем шума. Электродвигатели регулируются частотными блоками управления ABB (Германия). Датчики контроля температуры плавления — RKC (Япония). Пульты управления Siemens контролируют величину электротока и напряжения, давление и температуру плавления. Мощность регулируемого нагрева молдинга (головки) первого экструдера — 6-9 кВт, второго — 9-12 кВт. Для обеспечения непрерывности процесса гранулирования и очистки полимерного расплава на каждом экструдере используется автоматическая гидравлическая система смены фильтра. Материал — 38CrMoALA/40Cr с азотной обработкой. Кроме того, хромируется и полируется внутренний канал. Резка на гранулы происходит сразу на молдинге (горячая резка). Используется воздушное охлаждение гранулы, что удобнее и практичнее, чем водяное охлаждение, так как полностью сухая гранула по системе «циклон» загружается в накопительный бункер.
Агломератор АГ200
Агломератор для полимерных отходов предназначен для переработки различных полимерных отходов с эластичными свойствами (пленка, пакеты, волокно, ленты, трубки из ПВХ, ППХ, ПЭНД, линейный ПЭНД) в целях дальнейшего использования в качестве вторичного полимерного сырья. Агломератор осуществляет дробление отходов; перемешивание и окрашивание получившейся полимерной фракции. Процесс агломерации осуществляется при низкой температуре, благодаря чему не происходит изменений молекулярной структуры и физических качеств перерабатываемых полимеров.
Сергей ЗОЛОТОВ
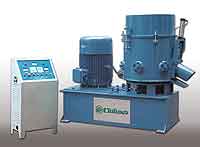
комплектующих.
Прессы для макулатуры, ПЭТ-бутылок, поролона, пленки, пластика, текстиля, кожи, металлических бочек
Пресс «Малыш» (технология PST Group, Канада) с боковой загрузкой (до 30 м3 в смену) используется на предприятиях с небольшим и средним количеством отходов (магазины, рынки, торговые и бизнес-центры, гостиницы, кинотеатры, выставочные и развлекательные комплексы, больницы, станции техобслуживания, типографии, коммунальные службы, дворцы спорта, приемные пункты вторсырья). Серийное производство прессов осуществляется по технологии Press System Technology на современном оборудовании от Amada и Evereising. Движущиеся детали пресса недоступны во время работы, а все открывающиеся люки блокируются до тех пор, пока не завершается рабочий цикл. Большое загрузочное окно позволяет загружать картонные коробки и объемные мешки с мусором. Выгрузка спрессованной кипы механизирована. Быстрая обвязка кипы осуществляется через технологические отверстия специальной лентой или веревкой (промышленная группа поставляет соответствующий обвязочный материал). Пресс работает при низких (до -45оС) температурах воздуха. Для его эксплуатации достаточно навеса от дождя, так как, в отличие от импортных прессов, он не комплектуется электроникой. Пресс устанавливают в небольших помещениях с ограниченной высотой потолка (подвалы, железнодорожные контейнеры) рядом с источником мусора, что значительно сокращает время транспортировки отходов. Для установки пресса с учетом площади его обслуживания требуется 1,5 м2, а для складирования 1 т прессованных отходов — 1,8 м2. При прессовании отходов вес кипы составляет в случае макулатуры до 70 кг, полимерной пленки, пластмассовых ящиков — до 80 кг, ТБО — до 80 кг. Вес можно регулировать, уменьшая или увеличивая высоту кипы. Пресс «Крепыш» с боковой загрузкой (до 50 м3 в смену) изготавливается по той же технологии и предназначен для организаций со средним количеством отходов (супермаркеты, рынки, предприятия пищевой, текстильной и легкой промышленности, типографии, торговые и бизнес-центры, выставочные, развлекательные и гостиничные комплексы, склады, таможенные терминалы, вокзалы, аэропорты, переработчики вторсырья). Работает при температуре до -30°С. Пресс устанавливают рядом с источником мусора, что сокращает время на транспортировку отходов. Для установки пресса с учетом площади его обслуживания требуется 1,5 м2, а для складирования 1 т прессованных отходов — от 1,0 м2 (в зависимости от вида отходов). Вес готовой кипы составляет 30-200 кг, объем — всего 0,34 м3. Кипа макулатуры может весить до 150 кг, полимерной пленки, пластмассовых ящиков — до 160 кг. Вес можно регулировать, уменьшая или увеличивая высоту кипы. В еврофуру объемом 82 м3 (13,6х2,45х2,45 м) загружается 198 кип (при правильной укладке). Все остальные параметры аналогичны таковым пресса «Малыш».
И самый большой пресс — «Профи PST 20» (с верхней загрузкой для любых отходов объемом до 150 м3 в смену) — предназначен для организаций с любым количеством отходов (торгово-развлекательные и бизнес-центры, гипермаркеты, предприятия пищевой, текстильной и легкой промышленности, производители тары и упаковки, полиграфические и складские комплексы, выставки, гостиницы, вокзалы, аэропорты, переработчики вторсырья). Вместо объемных контейнеров или других форм хранения отходы загружаются непосредственно в пакетировочный пресс. Для установки пресса с учетом площади его обслуживания требуется 3,5 м2, а для складирования 1 т прессованных отходов — от 0,8 м2 (в зависимости от вида отходов). Объем кипы — 0,62 м3, вес кипы макулатуры составляет до 400 кг, полимерной пленки, пластмассовых ящиков, ПЭТ-бутылок — до 350 кг, поролона — до 200 кг. Вес можно регулировать, уменьшая или увеличивая высоту кипы. При правильной укладке в еврофуру объемом 82 м3 (13,6х2,45х2,45 м) загружается 96 кип.
Дробилки «Бобер»
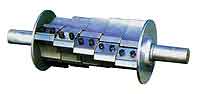
Шредеры
Однороторные шредеры (измельчители) предназначены для предварительной переработки древесины (паллеты, шпалы), отходов пластмасс в виде пленки, полипропиленовых и полиэтиленовых мешков, сливов (слитков), получаемых при запусках экструдеров, крупногабаритных отходов (трубы, бочки, короба, ящики), которые невозможно измельчить сразу в дробилке. С помощью гидравлического прессовочного устройства материал измельчается максимально эффективно, нагрузка на измельчающий ротор контролируется автоматически, режим работы пресса зависит от перерабатываемого материала и задается на пульте управления шредером. Ротор оборудуется системой реверсивного движения, что при превышении нагрузки свыше заданной оператором величины позволяет автоматически включить обратный ход, избежав повреждений ножей и двигателя. Ножи изготавливаются из высококачественной стали D2 и имеют 4 рабочие поверхности. При затуплении одной из поверхностей переточка ножа не требуется — его достаточно повернуть на 90°. Таким образом, срок службы ножей увеличивается в 4 раза. Такая конструкция ножей позволяет уменьшить и распределить нагрузку на ротор, уменьшить расход электроэнергии и увеличить производительность. Привод оснащен устройством плавного пуска, что позволяет снизить нагрузку на ножи, ротор и двигатель в момент пуска, если в камере остался непереработанный материал.
Линия переработки и гранулирования окрашенных полиэтиленовых и полипропиленовых пленочных отходов (двухшнековый экструдер)
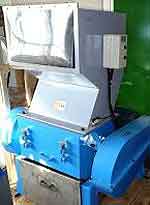
Агломератор АГ200
Агломератор для полимерных отходов предназначен для переработки различных полимерных отходов с эластичными свойствами (пленка, пакеты, волокно, ленты, трубки из ПВХ, ППХ, ПЭНД, линейный ПЭНД) в целях дальнейшего использования в качестве вторичного полимерного сырья. Агломератор осуществляет дробление отходов; перемешивание и окрашивание получившейся полимерной фракции. Процесс агломерации осуществляется при низкой температуре, благодаря чему не происходит изменений молекулярной структуры и физических качеств перерабатываемых полимеров.
Сергей ЗОЛОТОВ
Строительство и недвижимость. Статья была опубликована в номере 40 за 2007 год в рубрике оборудование и инструмент