Новая жизнь землебита
На фоне истощения энергетических запасов Земли, все возрастающих потребностей в энергоносителях, их безудержного удорожания вопросы обеспечения энергетической безопасности человечества беспокоят специалистов самых разных отраслей. В основу большинства научных разработок сегодня закладывается принцип энергосбережения. Учет этого принципа при проектировании современных зданий, разработке новых технологий строительства, создании строительных материалов дает весьма ощутимые результаты. Очевидно, что жилье XXI века должно строиться из доступных, экологически чистых, экономичных материалов. Одним из методов альтернативных энергосберегающих технологий является землебитное строительство.
Из истории вопроса
Строительство из грунта как способ решения архитектурных и градостроительных задач известно с незапамятных времен. Наши предки широко использовали его не только при возведении городских стен и других оборонительных сооружений, но также и при строительстве жилых домов, общественных и культовых зданий. С древних времен, особенно в безлесных районах, жилье и другие постройки возводили из грунта. Землю набивали в опалубки или блочные формы и добивались плотности трамбованием. Землебитные стены исключительно прочны и долговечны. Они дают небольшую усадку, мало набухают от сырости, почти не образуют трещин и имеют очень низкий коэффициент теплопроводности.
Одним из наиболее известных строений в технике землебита — набойки земли в опалубку с проливкой известью — считается Приоратский дворец в Гатчине. Дворец был построен в 1797-1799 годах архитектором Львовым по приказу императора Павла I. Это единственное подобное сооружение, так хорошо сохранившееся до наших дней. За свою долгую жизнь здание ни разу не реставрировалось. Более того, 100 лет дворец простоял в первозданном виде, и только потом стены здания оштукатурили, набив на них дрань. Во время Великой Отечественной войны здесь шли ожесточенные бои. От снарядов и авиабомб рушились даже более поздние массивные каменные постройки, а землебитный дворец выстоял. Архитектор сумел подобрать такой состав грунта, что он и по сей день по прочности соперничает с сооружениями из железобетона. Из камня выполнена только башня дворца и его цоколь. Стены были возведены в рекордные даже для нашего времени сроки — всего за два месяца. Во время строительства дворца в прочную передвижную опалубку закладывали подготовленную грунтомассу естественной влажности высотой 12-15 см, тщательно утрамбовывали и заливали шестимиллиметровым слоем известкового раствора нормальной жирности, после чего укладывали очередной слой грунта. В составе массы для возведения стен — 58% песка, 20% пыли (мелкой земли), 18% глины, 4% гравия (3-7 мм). Органические примеси не добавлялись. Прочность землебита через 20 лет после возведения здания составила 10-12 МПа, хотя цемент в его состав не вводился. Такие стены можно возводить везде, где они смогут просохнуть за лето.
Возрождение землебита
Период с 1954 по 1985 год характеризуется бурным развитием сборного железобетона. В это время из массового строительства были практически вытеснены все другие материалы включая и такие, казалось бы, традиционные, как кирпич и дерево, не говоря уже о грунте. Однако разразившийся в середине 70-х острый энергетический кризис заставил многих специалистов и политиков по-новому взглянуть на накопленный человечеством опыт. В 1972 г. в Иране собрались архитекторы и инженеры из разных стран мира для обсуждения проблем сохранения и развития многостороннего и глубокого культурного опыта, каковым является архитектура из грунта. В течение последующих лет усилиями этих специалистов была подготовлена организационная, юридическая и научная база для проведения I международной конференции "Архитектура из грунта", которая состоялась в 1980 году в турецкой столице Анкаре.
Этот международный форум положил основу официальному признанию, уже на современном уровне развития архитектурной и строительной мысли, архитектуры из грунта. В развитых странах мира стали создаваться центры и научные лаборатории по изучению проблем строительства из грунта, возрождению древних традиций такого строительства. Популярность землебитной архитектуры в мире растет с каждым годом. Сейчас в Испании, Италии, Франции, Англии, Японии, США, многих других странах подобный вид строительства приобретает все большую популярность. Необходимо заметить также, что в благополучных высокоразвитых странах популярность эта обусловлена не столько экономичностью, сколько превосходными строительными качествами, благоприятными условиями для проживания, высокой комфортабельностью таких строений. Здания из земли гигиеничны, сухи, кроме того, они значительно теплее кирпичных. Расход топлива для поддержания в них нормальной комнатной температуры меньше, чем при аналогичных условиях в каменных и даже деревянных зданиях. Постройки из земли не только не горят, но от действия огня становятся еще прочнее. Использование земли для строительства способствует также сбережению леса, снижению энергозатрат на изготовление и транспортировку стройматериалов, ведь для изготовления землеблоков подходит практически любая земля, за исключением чистого песка.
Теоретические основы современного землебита
Землебитное строительство сегодня опирается на достижения высоких технологий. Основой для их разработки стало использование всеобщего принципа самоорганизации, характеризующего все природные процессы, в результате которых образуются разнообразные структуры. Познать суть явления самоорганизации и использовать ее в собственных интересах оказалось вполне по силам пытливым умам. В окружающем мире при внимательном рассмотрении можно найти примеры, когда материалы, подобные грунту, и сам грунт приобретают предельно плотную структуру без значительных усилий. Один из наиболее ярких примеров — образование плотной дорожки вдоль береговой линии, называемой заплеском. Размеренное движение прибойной волны приводит к образованию плотной структуры независимо от характеристик грунта, образующего берег. Миллионы частичек песка по воле волн занимают наиболее устойчивое компактное положение, образуя между собой максимальное число контактов. И все это происходит без приложения больших давлений к слагающему берег материалу. Изучение и использование процессов, подобных этому, и позволило перевести материальное производство на более высокую качественную ступень.
В 1971 году Н.Е. Королевым был обнаружен неизвестный ранее природный механический эффект, открывший возможность качественного скачка в технике обработки сыпучих сред и названный эффектом текучего клина. На его основе было предложено и осуществлено принципиально новое действие над различными сыпучими материалами, известное теперь как зонное нагнетание. Зонное нагнетание — механический метод получения плотных и сверхплотных структур из сыпучих дисперсных сред. Суть его состоит в перемещении узкой зоны искусственно инициированного процесса самоорганизации вдоль обрабатываемого объема. Эта уникальная по своей простоте, эффективности и незначительному энергопотреблению технология позволяет быстро, дешево и качественно формовать, смешивать и дробить сыпучие порошкообразные и другие материалы. Технология зонного нагнетания позволяет достичь максимальной степени плотности без больших давлений, что коренным образом меняет традиционные представления о процессах уплотнения. Принципиальное отличие технологии зонного нагнетания от всех известных механических технологий и процессов обработки сыпучих материалов заключается именно в том, что она является открытым неравновесным стационарным процессом, в котором происходит постоянный обмен с внешней средой массой и энергией, тогда как все известные процессы осуществляются в закрытых системах, где происходит обмен с внешней средой только энергией. Известно, что самые эффективные природные процессы упорядочения (уплотнения) структуры сыпучих порошкообразных материалов проходят в открытых неравновесных системах и являются образцами, к которым необходимо приблизиться. Зонное нагнетание — это одно непрерывное действие, заменяющее собой при формовании изделий из сыпучих порошкообразных материалов совокупность традиционных действий: дозирование среды, укладку ее в форму или в слой, распределение по форме или слою, формование и уплотнение, калибрование размеров и отделку (заглаживание) поверхностей.
Оборудование
К настоящему времени разработано и создано большое количество разнообразных устройств зонного нагнетания для производства различных строительных изделий и конструкций. Некоторые виды технологического оборудования, использующего эффект текучего клина, показывают прекрасные результаты при получении плотной и особо плотной структуры из любых сыпучих материалов: от грунтов до металлических и металлокерамических порошков. Они имеют промышленную апробацию при производстве строительных блоков из обычного и стабилизированного грунта, арболита и бетонных смесей, а также стоек, столбов, плит и труб всевозможных размеров из разнообразных тяжелых и легких жестких бетонных смесей. Проведенные теоретические и экспериментальные исследования эффекта текучего клина позволяют в настоящее время создавать оборудование для использования метода зонного нагнетания в различных областях. В первую очередь — в промышленности строительных материалов, а также в дорожном строительстве, в порошковой металлургии, в производстве огнеупоров, в литейном производстве и ряде других производств, где требуется получить плотные структуры из сыпучих сред. Эффективность применения технологии зонного нагнетания в перечисленных областях основывается на ее замечательных свойствах.
Наибольший интерес представляют установки зонного нагнетания для мелкосерийного (мелкомасштабного) производства стеновых блоков, в том числе грунтоблоков, тротуарной плитки и камней мощения в подсобных цехах промышленных и сельскохозяйственных производств, непосредственно на строительных площадках, а также в кооперативных и личных хозяйствах. Установки зонного нагнетания имеют конструкцию нагнетателя, которая обеспечивает ему возможность одновременного продольного, бокового и вертикального перемещения. Такой тип нагнетателей получил название «русские качели» из-за схожести движений со всем известным устройством народной забавы. Установки легко вписываются в традиционные схемы производства стеновых блоков как в условиях строительной площадки, так и при промышленном производстве.
Схема установки зонного нагнетания
Установка работает следующим образом. В исходном состоянии форма располагается на основании в одном из крайних положений. При этом две ячейки формы находятся с наружной стороны стабилизирующего устройства с поднятыми в верхнее положение доньями, две другие ячейки с опущенными доньями располагаются внутри, причем крайняя из них находится под нагнетателем. Подготовленную должным образом грунтовую смесь или грунт подают в бункер- течку. Одновременно с этим включают привод рабочего органа. Грунт просыпается через качающийся нагнетатель и заполняет ячейку формы через ее открытую сторону. При качании нагнетатель, периодически отдаляясь и приближаясь к открытой стороне формы, нагнетает в форму порции грунта, которые попадают под него.
После того, как в ячейке под нагнетателем грунт достигнет максимальной плотности и начнет вытесняться вверх через открытую сторону формы, включают привод передвижения формы. При этом продолжают подавать грунт в бункер-течку, следя за тем, чтобы в ней все время был грунт. Установка спроектирована таким образом, что при этом условии, если нет зависания материала на решетке нагнетателя, автоматически соблюдаются условия образования под нагнетателем текучей уплотненной локальной зоны, то есть условия поддержания эффекта текучего клина, на протяжении всего процесса формования. По мере прохождения формы под качающимся нагнетателем ее ячейки заполняются уплотненным грунтом и затем попадают под заглаживающую подошву стабилизирующего устройства, посредством которой осуществляется калибровка отформованных грунтоблоков. После выхода двух грунтоблоков из-под заглаживающей подошвы донья ячеек поднимаются вверх, производя распалубку блоков, и форма останавливается в крайнем положении. Оператор вынимает распалубленные грунтоблоки из формы. Вслед за этим автоматически включается привод передвижения формы, и она начинает двигаться в исходное положение. При этом процесс нагнетания грунта продолжается. При достижении исходного положения происходит распалубка изготовленных блоков из двух других ячеек формы, и она вновь останавливается. После съема этих блоков вновь включается привод передвижения формы, перемещая ее в другое крайнее положение, в котором опять происходит распалубка и съем блоков, изготовленных в двух первых ячейках. И так продолжается, пока длится процесс формовки блоков.
Установки зонного нагнетания по сравнению с традиционным формовочным оборудованием обеспечивают более высокое качество формовок по плотности и точности размеров без приспособлений для дозирования рыхлой массы в форму, контроля давления и размера формуемого изделия. На них полностью устраняются такие виды брака, как трещины, перепрессовка, упругое последействие. При работе на установках зонного нагнетания не требуется переналадки при переходе с одного материала на другой, например, от формования блоков из суглинков на формование блоков из бетонной смеси или арболита. Эксплуатировать и обслуживать эти установки могут рабочие невысокой квалификации ввиду простоты и надежности конструкции установки. При работе установок зонного нагнетания отсутствует вибрация и сверхнормативный шум, износ формообразующих элементов минимален по сравнению с традиционным прессованием. Такие установки позволяют формовать изделия из широкого спектра материалов и их композиций с высокой точностью геометрических размеров изготовляемых изделий. Агрегат обладает малыми габаритами и массой, что позволяет транспортировать ее на любом виде грузового транспорта и использовать небольшие производственные площади. Из-за особенности конструкции установки исключаются подготовительные работы перед запуском в эксплуатацию. Мощность приводов установки невелика, что делает процесс формования малоэнергоемким. Низкое энергопотребление, отсутствие вибраций и сверхнормативного шума, комфортные условия работы обслуживающего персонала, а также легкость управления делают эту установку экологически безопасной.
Установка зонного нагнетания для изготовления грунтоблоков.
1 — основание, 2 — механизм перемещения формы, 3 — механизм распалубки изделий, 4 — четырехместная форма, 5 — стабилизирующее устройство, 6 — нагнетательное устройство, 7 — решетчатый нагнетатель, 8 — электромеханический привод рабочего органа, 9 — опорный элемент, 10 — бункер-течка.
Людмила АЛЕКСЕЕВА при содействии Сергея АМЕЛИНА, коммерческого директора проекта «Русские качели»
обсуждение статьи
Из истории вопроса
Строительство из грунта как способ решения архитектурных и градостроительных задач известно с незапамятных времен. Наши предки широко использовали его не только при возведении городских стен и других оборонительных сооружений, но также и при строительстве жилых домов, общественных и культовых зданий. С древних времен, особенно в безлесных районах, жилье и другие постройки возводили из грунта. Землю набивали в опалубки или блочные формы и добивались плотности трамбованием. Землебитные стены исключительно прочны и долговечны. Они дают небольшую усадку, мало набухают от сырости, почти не образуют трещин и имеют очень низкий коэффициент теплопроводности.
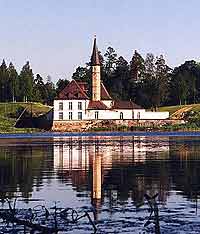
Возрождение землебита
Период с 1954 по 1985 год характеризуется бурным развитием сборного железобетона. В это время из массового строительства были практически вытеснены все другие материалы включая и такие, казалось бы, традиционные, как кирпич и дерево, не говоря уже о грунте. Однако разразившийся в середине 70-х острый энергетический кризис заставил многих специалистов и политиков по-новому взглянуть на накопленный человечеством опыт. В 1972 г. в Иране собрались архитекторы и инженеры из разных стран мира для обсуждения проблем сохранения и развития многостороннего и глубокого культурного опыта, каковым является архитектура из грунта. В течение последующих лет усилиями этих специалистов была подготовлена организационная, юридическая и научная база для проведения I международной конференции "Архитектура из грунта", которая состоялась в 1980 году в турецкой столице Анкаре.
Этот международный форум положил основу официальному признанию, уже на современном уровне развития архитектурной и строительной мысли, архитектуры из грунта. В развитых странах мира стали создаваться центры и научные лаборатории по изучению проблем строительства из грунта, возрождению древних традиций такого строительства. Популярность землебитной архитектуры в мире растет с каждым годом. Сейчас в Испании, Италии, Франции, Англии, Японии, США, многих других странах подобный вид строительства приобретает все большую популярность. Необходимо заметить также, что в благополучных высокоразвитых странах популярность эта обусловлена не столько экономичностью, сколько превосходными строительными качествами, благоприятными условиями для проживания, высокой комфортабельностью таких строений. Здания из земли гигиеничны, сухи, кроме того, они значительно теплее кирпичных. Расход топлива для поддержания в них нормальной комнатной температуры меньше, чем при аналогичных условиях в каменных и даже деревянных зданиях. Постройки из земли не только не горят, но от действия огня становятся еще прочнее. Использование земли для строительства способствует также сбережению леса, снижению энергозатрат на изготовление и транспортировку стройматериалов, ведь для изготовления землеблоков подходит практически любая земля, за исключением чистого песка.
Теоретические основы современного землебита
Землебитное строительство сегодня опирается на достижения высоких технологий. Основой для их разработки стало использование всеобщего принципа самоорганизации, характеризующего все природные процессы, в результате которых образуются разнообразные структуры. Познать суть явления самоорганизации и использовать ее в собственных интересах оказалось вполне по силам пытливым умам. В окружающем мире при внимательном рассмотрении можно найти примеры, когда материалы, подобные грунту, и сам грунт приобретают предельно плотную структуру без значительных усилий. Один из наиболее ярких примеров — образование плотной дорожки вдоль береговой линии, называемой заплеском. Размеренное движение прибойной волны приводит к образованию плотной структуры независимо от характеристик грунта, образующего берег. Миллионы частичек песка по воле волн занимают наиболее устойчивое компактное положение, образуя между собой максимальное число контактов. И все это происходит без приложения больших давлений к слагающему берег материалу. Изучение и использование процессов, подобных этому, и позволило перевести материальное производство на более высокую качественную ступень.
В 1971 году Н.Е. Королевым был обнаружен неизвестный ранее природный механический эффект, открывший возможность качественного скачка в технике обработки сыпучих сред и названный эффектом текучего клина. На его основе было предложено и осуществлено принципиально новое действие над различными сыпучими материалами, известное теперь как зонное нагнетание. Зонное нагнетание — механический метод получения плотных и сверхплотных структур из сыпучих дисперсных сред. Суть его состоит в перемещении узкой зоны искусственно инициированного процесса самоорганизации вдоль обрабатываемого объема. Эта уникальная по своей простоте, эффективности и незначительному энергопотреблению технология позволяет быстро, дешево и качественно формовать, смешивать и дробить сыпучие порошкообразные и другие материалы. Технология зонного нагнетания позволяет достичь максимальной степени плотности без больших давлений, что коренным образом меняет традиционные представления о процессах уплотнения. Принципиальное отличие технологии зонного нагнетания от всех известных механических технологий и процессов обработки сыпучих материалов заключается именно в том, что она является открытым неравновесным стационарным процессом, в котором происходит постоянный обмен с внешней средой массой и энергией, тогда как все известные процессы осуществляются в закрытых системах, где происходит обмен с внешней средой только энергией. Известно, что самые эффективные природные процессы упорядочения (уплотнения) структуры сыпучих порошкообразных материалов проходят в открытых неравновесных системах и являются образцами, к которым необходимо приблизиться. Зонное нагнетание — это одно непрерывное действие, заменяющее собой при формовании изделий из сыпучих порошкообразных материалов совокупность традиционных действий: дозирование среды, укладку ее в форму или в слой, распределение по форме или слою, формование и уплотнение, калибрование размеров и отделку (заглаживание) поверхностей.
Оборудование
К настоящему времени разработано и создано большое количество разнообразных устройств зонного нагнетания для производства различных строительных изделий и конструкций. Некоторые виды технологического оборудования, использующего эффект текучего клина, показывают прекрасные результаты при получении плотной и особо плотной структуры из любых сыпучих материалов: от грунтов до металлических и металлокерамических порошков. Они имеют промышленную апробацию при производстве строительных блоков из обычного и стабилизированного грунта, арболита и бетонных смесей, а также стоек, столбов, плит и труб всевозможных размеров из разнообразных тяжелых и легких жестких бетонных смесей. Проведенные теоретические и экспериментальные исследования эффекта текучего клина позволяют в настоящее время создавать оборудование для использования метода зонного нагнетания в различных областях. В первую очередь — в промышленности строительных материалов, а также в дорожном строительстве, в порошковой металлургии, в производстве огнеупоров, в литейном производстве и ряде других производств, где требуется получить плотные структуры из сыпучих сред. Эффективность применения технологии зонного нагнетания в перечисленных областях основывается на ее замечательных свойствах.
Наибольший интерес представляют установки зонного нагнетания для мелкосерийного (мелкомасштабного) производства стеновых блоков, в том числе грунтоблоков, тротуарной плитки и камней мощения в подсобных цехах промышленных и сельскохозяйственных производств, непосредственно на строительных площадках, а также в кооперативных и личных хозяйствах. Установки зонного нагнетания имеют конструкцию нагнетателя, которая обеспечивает ему возможность одновременного продольного, бокового и вертикального перемещения. Такой тип нагнетателей получил название «русские качели» из-за схожести движений со всем известным устройством народной забавы. Установки легко вписываются в традиционные схемы производства стеновых блоков как в условиях строительной площадки, так и при промышленном производстве.
Схема установки зонного нагнетания
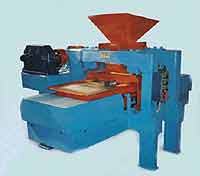
После того, как в ячейке под нагнетателем грунт достигнет максимальной плотности и начнет вытесняться вверх через открытую сторону формы, включают привод передвижения формы. При этом продолжают подавать грунт в бункер-течку, следя за тем, чтобы в ней все время был грунт. Установка спроектирована таким образом, что при этом условии, если нет зависания материала на решетке нагнетателя, автоматически соблюдаются условия образования под нагнетателем текучей уплотненной локальной зоны, то есть условия поддержания эффекта текучего клина, на протяжении всего процесса формования. По мере прохождения формы под качающимся нагнетателем ее ячейки заполняются уплотненным грунтом и затем попадают под заглаживающую подошву стабилизирующего устройства, посредством которой осуществляется калибровка отформованных грунтоблоков. После выхода двух грунтоблоков из-под заглаживающей подошвы донья ячеек поднимаются вверх, производя распалубку блоков, и форма останавливается в крайнем положении. Оператор вынимает распалубленные грунтоблоки из формы. Вслед за этим автоматически включается привод передвижения формы, и она начинает двигаться в исходное положение. При этом процесс нагнетания грунта продолжается. При достижении исходного положения происходит распалубка изготовленных блоков из двух других ячеек формы, и она вновь останавливается. После съема этих блоков вновь включается привод передвижения формы, перемещая ее в другое крайнее положение, в котором опять происходит распалубка и съем блоков, изготовленных в двух первых ячейках. И так продолжается, пока длится процесс формовки блоков.
Установки зонного нагнетания по сравнению с традиционным формовочным оборудованием обеспечивают более высокое качество формовок по плотности и точности размеров без приспособлений для дозирования рыхлой массы в форму, контроля давления и размера формуемого изделия. На них полностью устраняются такие виды брака, как трещины, перепрессовка, упругое последействие. При работе на установках зонного нагнетания не требуется переналадки при переходе с одного материала на другой, например, от формования блоков из суглинков на формование блоков из бетонной смеси или арболита. Эксплуатировать и обслуживать эти установки могут рабочие невысокой квалификации ввиду простоты и надежности конструкции установки. При работе установок зонного нагнетания отсутствует вибрация и сверхнормативный шум, износ формообразующих элементов минимален по сравнению с традиционным прессованием. Такие установки позволяют формовать изделия из широкого спектра материалов и их композиций с высокой точностью геометрических размеров изготовляемых изделий. Агрегат обладает малыми габаритами и массой, что позволяет транспортировать ее на любом виде грузового транспорта и использовать небольшие производственные площади. Из-за особенности конструкции установки исключаются подготовительные работы перед запуском в эксплуатацию. Мощность приводов установки невелика, что делает процесс формования малоэнергоемким. Низкое энергопотребление, отсутствие вибраций и сверхнормативного шума, комфортные условия работы обслуживающего персонала, а также легкость управления делают эту установку экологически безопасной.
Установка зонного нагнетания для изготовления грунтоблоков.
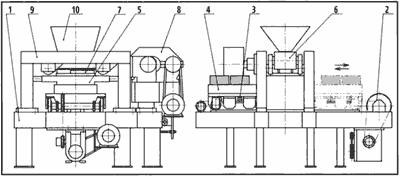
Людмила АЛЕКСЕЕВА при содействии Сергея АМЕЛИНА, коммерческого директора проекта «Русские качели»
обсуждение статьи
Строительство и недвижимость. Статья была опубликована в номере 39 за 2005 год в рубрике материалы и технологии