Производство труб большого диаметра из полиэтилена
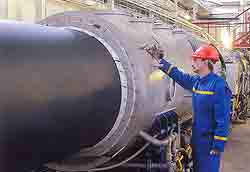
Любая линия производства труб из полиэтилена состоит из следующих основных элементов: экструдера, трубной головки, калибра, вакуумных и (или) охлаждающих ванн, тянущего и отрезного устройств. Процесс получения трубы при ее непрерывном движении по технологической цепочке складывается из следующих стадий: получение расплава полиэтилена в экструдере, формование трубной заготовки в экструзионной трубной головке, калибрование заготовки об охлаждаемую поверхность калибра, охлаждение калиброванной трубы в охлаждающих (вакуумных) ваннах, резка трубы на мерные отрезки. Известны и практикуются два различных способа производства полиэтиленовых труб, отличающихся по способу калибрования: пневмокалибрование и вакуумкалибрование. Какие же трудности на пути освоения производства труб большого диаметра встречали разработчики оборудования и производители труб?
1. Отсутствие экструдеров большой единичной производительности, низкая производительность процесса
Одношнековый экструдер долгое время рассматривали как винтовой насос, в котором давление создавалось в расплаве на последнем этапе в зоне нагнетания. Соответственно, предыдущие зоны рассматривались как вспомогательные: зона питания — для подачи гранул в зону плавления, следующая зона — для плавления материала. От известных с конца позапрошлого века экструдеров для переработки резины экструдер для переработки, например, полиэтилена отличался лишь длиной и геометрией шнека, приспособленной к реологическим и теплофизическим свойствам материала. Такой экструдер был чрезвычайно чувствительным к противодавлению экструзионной головки, величине зазора между гребнем витка шнека и цилиндром, температурному режиму и свойствам материала даже одного и того же вида. Производительность же экструдера с диаметром шнека, например, 160 мм, на котором базировалась линия производства труб большого диаметра Вильнюсского завода, не превышала 200-250 кг/час. С применением в зоне загрузки рифленых охлаждаемых втулок характер работы экструдера революционно изменился. Теперь на длине шнека, равной пяти диаметрам, в зоне втулки еще на твердом материале развивается все действующее в экструдере давление. На всей оставшейся длине шнека идет нагрев, плавление гранул и гомогенизация расплава полимера без функции его транспортирования, то есть шнек вместе с головкой является вынужденным, но необходимым для качественной подготовки расплава сопротивлением движению расплава. Уже первые экструдеры с диаметром шнека 90 мм, снабженные рифленой втулкой, имели производительность 300 кг/час, а экструдер с диаметром шнека 200 мм — 600 кг/час. Именно на базе таких экструдеров было построено производство труб Казанского ПО "Органический синтез". В дальнейшем разработчиками экструдеров эволюционно решались вопросы интенсификации нагрева и перемешивания ламинарных потоков расплава, в том числе с применением барьерных шнеков, а также увеличения питающей способности зоны рифленой втулки, благодаря чему производительность была повышена еще более чем в 2 раза. Для современного экструдера с диаметром шнека 120 мм нормальной является производительность ЭОО 1200 кг/час. При этом расплав полиэтилена имеет высокую температурную однородность.
2. Экструзионная головка
Экструзионная трубная головка предназначена для формования трубной заготовки из цилиндрического потока расплава полимера. Трубная головка крепится на фланцах к корпусу экструдера, имеет дорн, формирующий внутреннюю поверхность трубы, дорнодержатель, внешний корпус, матрицу, формирующую внешнюю поверхность труб. Наличие дорна и дорнодержателя, рассекающего поток расплава, является выпущенной особенностью прямоточных головок для экструзии заготовок полого профиля. Для труб малого диаметра традиционно использовался дорнодержатель в виде четырех-шести перьев обтекаемой формы, связывающих внутренний дорн с внешним корпусом. Рассечение потока расплава преградой (дорнодержателем) приводит к тому, что в потоке расплава за преградой тянется шлейф, имеющий другую деформационную историю и по-другому разбухающий при выходе из головки, чем остальная (по периметру) масса расплава. С увеличением диаметров труб и ростом производительности при такой примитивной конструкции дорнодержателя неизбежно возникает огранка внутренней, не калибруемой поверхности трубы. Так что при освоении процесса производства труб большого диаметра разработчикам пришлось серьезно поработать над конструкцией экструзионной головки. Основная идея борьбы с огранкой — подвергнуть расплав после его прохождения через дорнодержатель новому, интенсивному и по возможности равномерному, деформационному воздействию в специальных выравнивающих зонах головки. К настоящему моменту сложилось в основном два типа конструкции головки, в определенной мере отвечающих этой идее:
1. Дорнодержатель выполнен в виде цилиндрических каналов, практически перпендикулярных к оси головки. Выравнивающая зона — в виде винтовых каналов с уменьшающейся по ходу движения глубиной.
2. Дорнодержатель по существу тот же, а выравнивающая зона — в виде перфорированного стакана-сетки.
Интересно, что такие конструкции головок изначально были разработаны и применены в производстве труб большого диаметра и лишь позднее вернулись в высокопроизводительные линии для производства труб малого диаметра.
3. Способ калибрования
Выходящая из экструзионной головки расплавленная заготовка должна быть откалибрована. Калибрование заготовки осуществляется охлаждаемой металлической поверхностью, к которой она прижимается избыточным внутренним давлением воздуха. На собственно процесс калибрования не влияет способ создания избытка давления: либо мы поднимаем давление внутри трубы больше атмосферного (пневмокалибрование), либо мы создаем разрежение снаружи трубы (вакуумкалибрование). Все различия между пневмо- и вакуумкалиброванием относятся только к аппаратному оформлению и приемам запуска и ведения процесса.
Пневмокалибрование
Для создания избыточного давления внутри трубы методом пневмокалибрования ее свободный передний конец необходимо заглушить. Если труба имеет диаметр 10-40 мм, можно просто перегнуть ее конец и направить на намотку, в других случаях трубу заглушают с помощью плавающей пробки, прикрепленной к дорну экструзионной головки тросом. Казалось бы, ничего страшного, и весь мир десятилетиями так и работал. Однако пробка должна быть установлена на таком расстоянии от головки, на котором труба затвердела насквозь. С увеличением производительности это расстояние увеличивается, увеличивается стрела провиса троса под собственным весом, и трос начинает касаться внутренней еще расплавленной поверхности трубы. Оказалось, что только по этой причине даже трубу диаметром 160 мм SDR 11 нельзя получить с производительностью больше 165 кг/час, а диаметром 225 мм (допустимая стрела провиса чисто геометрически больше) — до 250 кг/час. С ростом производительности экструдеров такие показатели не могли удовлетворить производителей, поэтому первые линии с вакуумным калиброванием и первые вакуумные ванны были созданы для этого диапазона размеров труб, а трубы большого диаметра (315-1200 мм) еще некоторое время выпускали с помощью пневмокалибрования (в Казани, например, они выпускаются так и до сих пор). Но с увеличением диаметра трубы плавающая пробка приобретает все более кошмарный вид. Пробка для трубы, например, диаметром 630 мм имеет длину около 1,5 метра и вес около 500 кг: в 5-6 рядов установлены наборы резиновых диафрагм с подпорными шайбами. Имеются роликовые опоры, разгружающие диафрагмы от собственного веса пробки, и элементы безопасности, так как потенциально при использовании такой пробки мы имеем готовую к выстрелу пневматическую пушку, способную пробить стену здания и забросить пробку на соседнюю территорию. Имеющий фантазию пусть теперь мысленно установит эту пробку внутрь пусковой трубы и протолкнет ее вперед — чтобы предварительно натянуть трос. При ненатянутом тросе пробка автоматически разгерметизируется элементом безопасности или, если его нет, при подаче давления калибрования "прыгнет" вперед на расстояние слабины троса. Остается теперь так ловко запустить процесс, чтобы на стартовом стыке не образовалось заметного внутреннего наплыва, на котором пробка через три-четыре часа может застрять и в лучшем случае остановить тянущее устройство. Если учесть, что запуск процесса происходит вслепую, когда калибр уже состыкован с матрицей, о таких мелочах, как полная переборка комплекта диафрагм при переходе к производству трубы с другим SDR или их замена через две-три недели работы, можно и не вспоминать. Вакуумная ванна для вакуумкалибрования труб большого диаметра сложнее и дороже герметизирующей пробки, но, накопив опыт проектирования, изготовления и эксплуатации вакуумных ванн для труб диаметром до 225 мм, при расширении производства труб большого диаметра промышленность экструзии труб и в этом случае естественным образом пошла по пути применения вакуумного калибрования.
Вакуумкалибрование
Для создания избыточного давления внутри трубы методом вакуумкалибрования трубная заготовка расплава подается в специальное устройство — вакуумную ванну, в которой поддерживается вакуум от 0,01 до 0,09 МПа. На входе в вакуумную ванну установлен калибр. Внутренний диаметр и длина калибра зависят от многих факторов, которые трудно учесть при проектировании, и, как правило, в состав линии входит целый набор калибров для производства трубы одного диаметра, но различных SDR. При производстве труб большого диаметра это превращается в серьезную техническую и финансовую проблему. Для обеспечения условий вакуумного калибрования заготовка должна входить в калибр с небольшим наплывом, и внутренний диаметр матрицы должен быть больше диаметра калибра. При входе в калибр заготовка трубы вытягивается, следовательно, формующий зазор между матрицей и дорном также больше номинальной толщины стенки трубы. Сказанное автоматически подразумевает применение для производства трубы заданного SDR индивидуального дорна. Инструмент (дорн, матрица) и калибры для производства труб большого диаметра — сложные, тяжелые, дорогостоящие детали. Масса комплекта дорн-матрица для производства труб 1200 мм достигает 3000 кг, масса калибра на 1200 мм — около 1000 кг, стоимость комплекта инструмента и калибров намного выше стоимости трубной головки и может достигать до 25% стоимости всей линии. В связи с этим некоторые фирмы — производители оборудования в целях сокращения стоимости линий рекомендуют использование одного инструмента и калибра не только для производства труб одного диаметра с разным SOR, но даже для производства труб различного диаметра. Использование такого инструмента может привести к увеличению количества некондиционной трубы при выходе на режим и резкому ухудшению качества производимых труб вообще. Разрежение в вакуумной ванне не только обеспечивает плотный контакт поверхности заготовки с калибром, установленным на входе в ванну, но и препятствует ее реализации под действием неизбежных при дальнейшем охлаждении термических напряжений в стенке заготовки. Время действия разрежения (длина вакуумных ванн) должно быть таким, чтобы постоянно увеличивающаяся прочность охлаждаемой заготовки превысила действие внутренних напряжений, искажающих форму. Это время соответствует приблизительно половине длины полного охлаждения и при современном уровне производительности требует установки двух-трех вакуумных ванн длиной не менее 6 метров.
Первая в России линия производства полиэтиленовых труб большого диаметра — от 315 да 1200 мм — методом вакуумкалибрования была создана и освоена в 2003 году на Климовском трубном заводе (холдинг "Евротрубпласт"). Перед созданием линии были изучены технические и коммерческие предложения ведущих западноевропейских и азиатских производителей оборудования (предложения были получены от восьми фирм). Было принято решение не приобретать комплектную линию. Значительная часть технологического оборудования — калибры, вакуумные и охлаждающие ванны — была разработана техническими службами холдинга и изготовлена в России. Экструдер, экструзионная головка, тянущее и отрезное устройства были приобретены у ведущих европейских производителей. В настоящее время на линии освоен выпуск всех видов труб из ПЭ-80 и ПЭ-100 диаметром от 630 до 1200 мм вплоть до диаметра 1200 мм SDR 17,6 (ПЭ 100). Производительность линии по трубам составляет 900-1100 кг/час. В Беларуси продукцию холдинга "Евротрубпласт" представляет завод полимерных труб "КИРАННА", который также использует в производственном процессе экструзионные линии ведущих зарубежных производителей.
Материал предоставлен пресс-службой СП "КИРАННА" ООО
Строительство и недвижимость. Статья была опубликована в номере 04 за 2005 год в рубрике материалы и технологии