Вопросы технологии усиления строительных конструкций
Продолжение. Начало в СиН №№ 23, 24, 30, 31, 38
2.3. Восстановление несущей способности и усиление железобетонных конструкций
Усиление может производиться как в случае изменения нагрузок на конструкцию, так и при сохранении нагрузок и расчетной схемы. В последнем случае при усилении фактически необходимо восстановить конструкцию в первоначальном (проектном) виде.
Основными примерами восстановления несильно поврежденных конструкций являются мероприятия:
— по заделке трещин в бетонных и железобетонных конструкциях;
— по восстановлению разрушенных защитных слоев бетона;
— по усилению поврежденных опорных частей балок и прочих элементов, работающих на восприятие поперечной нагрузки.
Предполагается, что указанные нарушения в конструкциях возникли вследствие однократного (случайного) воздействия каких-либо внешних факторов. Причем дальнейшая работа конструкции предполагается при воздействии нагрузок, не превышающих проектные. Трещины в бетонных и железобетонных конструкциях заделываются цементно-песчаным раствором или шпаклюются синтетическим материалом. При ширине трещин более 0,3 мм и глубине не более 50 мм трещины заделывают раствором на расширяющемся цементе с водоцементным отношением В/Ц = 0,6-2,0 или синтетической смолой, которые подаются (нагнетаются) растворонасосом в трещину с помощью поверхностного инъектора. Предварительной обработки (разделки трещин, сверления скважин и т.п.) в этом случае не требуется. Единственное, что необходимо сделать перед нагнетанием раствора, — заделать (закрыть) трещину по лицевой поверхности конструкции, оставив промежутки 20-30 см с шагом 0,5-1,5 м незаделанной поверхности. Трещину закрывают лентой или замазывают клеем или бетоном (рис. 2.1).
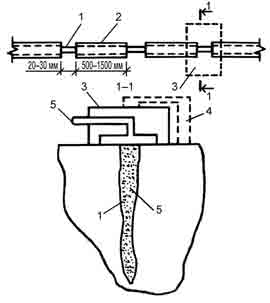
Рис. 2.1. Нагнетание цементно-песчаного раствора при ширине трещин не более 0,3 мм и глубине до 50 мм: 1 — трещина в конструкции; 2 — пространство, заделываемое бетоном, клеем или лентой; 3 — иньектор поверхностного типа; 4 — крепление инъектора (струбцины, болты и др.); 5 — раствор.
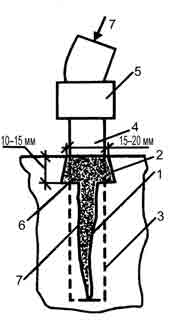
Рис. 2.2. Нагнетание цементно-песчаного раствора при ширине раскрытия трещин менее 0,3 мм: 1 — трещина в конструкции; 2 — расшитая трещина; 3 — просверленное отверстие для постановки и заделки инъекционной трубки; 4 — инъекционная трубка; 5 — штуцер с гайкой для подключения шланга к инъекционной трубке; 6 — цементно-песчаный раствор; 7 — раствор с В/Ц = 0,7-2,0 на расширяющемся цементе.
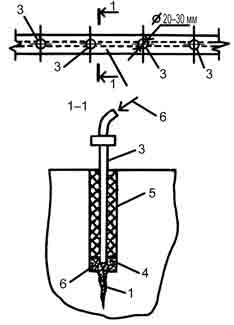
Рис. 2.3. Нагнетание цементно-песчаного раствора при ширине трещин более 0,3 мм и глубине более 50 мм: 1 — трещина в конструкции (глубиной более 50 мм); 2 — пространство, заделываемое бетоном, клеем или лентой; 3 — напорная инъекционная трубка; 4 — просверленная скважина; 5 — резиновый уплотнитель; 6 — раствор с В/Ц = 0,6-2,0 на расширяющемся цементе или синтетические смолы (от растворонасоса).
При ширине раскрытия трещин менее 0,3 мм или более 0,3 мм, но глубине более 50 мм поверхностные инъекторы не применяются. Если трещина узкая (ширина менее 0,3 мм), то раствор нагнетается в трещину под давлением 490-1960 кг/см2 через инъекционные трубки, устанавливаемые в специально просверливаемые в конструкции отверстия (скважины). Верх трещины (около поверхности конструкции) разделывается (расшивается): вдоль всей трещины распиливается расширяющийся вовнутрь конструкции паз, заполняемый цементно-песчаным раствором (состав раствора — 1:1) (рис. 2.2.). При трещинах шириной более 0,3 мм и глубиной более 50 мм раствор на расширяющемся цементе нагнетается в трещину через напорные инъекционные скважины, располагаемые по длине трещины с шагом 1-1,5 м. При этом поверхность трещины между скважинами закрывается (заделывается) аналогично тому, как делается в случае трещин глубиной до 50 мм (рис. 2.3). Короткие и неглубокие трещины предварительно разделывается фрезой до ширины более 10 мм. После этого они заполняются раствором на расширяющемся цементе или синтетической смолой. При больших повреждениях (широких трещинах), кроме заделки собственно трещины, рекомендуется усиливать конструкцию обоймой или рубашками из железобетона. Для изготовления раствора во всех случаях заделки трещин рекомендуется применять глиноземистый расширяющийся цемент марок 400, 500 или напрягающий цемент НЦ-20. Расход цемента должен быть не менее 400 кг/м3. После заделки трещин должна быть дана выдержка при положительной температуре или паропрогрев при температуре 50°С на расширяющемся цементе и 50°-60°С — на напрягающем цементе.
Восстановление защитного слоя бетона производится путем:
— оштукатуривания конструкции плотным цементно-песчаным раствором с возможным нанесением по нему трещиностойкого лакокрасочного покрытия;
— обетонирования цементным бетоном или полимербетоном, имеющим прочность не ниже прочности бетона восстанавливаемой конструкции;
— торкретирования плотным цементно-песчаным раствором.
При всех способах восстановления защитного слоя бетона предварительно производится подготовка усиливаемых конструкций. Перед работами по обработке поверхности визуально и простукиванием молотком уточняют размеры зон, с которых удаляют низкопрочный бетон. Дефектные участки определяют по отслоению защитного слоя, наличию мелкой сетки трещин на поверхности, коррозии бетона, следов ржавчины, глухому звуку при ударе, отслоению защитного слоя при простукивании и др. Удалять низкопрочный бетон следует оконтуриванием дефектных зон бороздой, постепенно ее затем углубляя внутри дефектной зоны.
Разрушенный по периметру сечения в изгибаемых конструкциях бетон следует обрубать вертикально, в сжатых конструкциях — горизонтально. Для улучшения сцепления с вновь укладываемым бетоном поверхность конструкций должна быть подвержена механической обработке. При малых объемах работ механическая обработка поверхности выполняется при помощи ручного, электрического и пневматического инструментов (щеток, пучковых молотков и т.п.). При больших объемах работ — гидроабразивным способом с использованием оборудования для набрызга бетона (пульпа приготавливается из трех частей песка и семи частей воды), пескоструйным и термоструйным способами с использованием аппаратов ТСА-12 и ТА-12. При необходимости приварки коротышей, соединительных скоб существующая арматура вскрывается в местах их установки не менее чем на половину своего диаметра участками, превышающими длину соединительных деталей на 10-15 мм. Пыль с обрабатываемой поверхности смывается. Поверхность конструкции расчищается на глубину, где бетон имеет водородный показатель рН і 12. После расчистки поверхности конструкций от "слабого" бетона необходимо очистить рабочую арматуру восстанавливаемой конструкции от продуктов коррозии. Это производится в зависимости от объема работ зубилом, стальными щетками, скребками или при помощи пескоструйного аппарата. При восстановлении защитного слоя оштукатуриванием очищенная арматура покрывается казеиновым слоем с замедлителем коррозии. Состав этого покрытия в частях по массе: портландцемент — 100; вода — 30-40; нитрат натрия — 10; казеиновый клей — 5. Состав цементно-песчаного раствора, наносимого в виде штукатурки — 1:2,5-1:3. После оштукатуривания при отсутствии покрытия арматуpы казеиновым клеем поверхность штукатурки покрывается лакокрасочным покрытием, состав которого выбирается в соответствии со степенью агрессивности среды согласно нормам.
При обетонировании конструкции цементный бетон должен иметь прочность не ниже прочности конструкции. Перед обетонированием расчищенная поверхность конструкции увлажняется и может быть покрыта слоем цементно-песчаного раствора состава 1:2. Восстанавливаемый защитный слой (наносимый обетонированием или торкретированием) в последнем случае должен быть уложен через 90 мин. после нанесения слоя цементно-песчаного раствора. При применении для восстановления защитного слоя полимербетона возможный его состав (в частях по массе) следующий: эпоксидная смола — 100; каменноугольный лак — 100; жидкий тиокол — 20; отвердитель ПЭПА — 10; цемент — 100-150. В случае коррозии арматуры для компенсации прокорродировавшей ее части применяют накладки из арматурной стали, привариваемые к рабочей арматуре (рис. 2.4). При восстановлении защитного слоя бетона торкретированием плотным цементно-песчаным раствором (рис. 2.5) к рабочей арматуре конструкции приваривается арматурная сетка из проволоки диаметром 2-3 мм и ячейкой »50х50 мм. Применяют цементно-песчаный раствор состава 1:1-1:1,5 на портландцементе марки 400-500 или аналогичном по марке глиноземистом цементе при его расходе не менее 400 кг/м3.
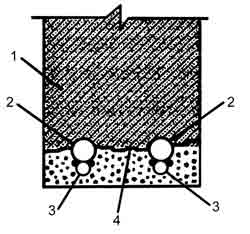
Рис. 2.4. Обетонирование цементным бетоном: 1 — восстанавливаемая конструкция; 2 — рабочая арматура восстанавливаемой конструкции; 3 — накладки из арматурной стали, приваренные к рабочей арматуре; 4 — расчищенная поверхность конструкции; 5 — восстановленный защитный слой бетона, наносимый обетонированием или торкретированием.
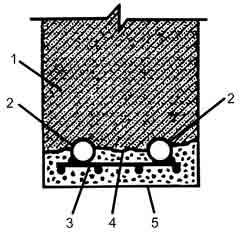
Рис. 2.5. Торкретирование плотным цементно-песчаным раствором: 1 — восстанавливаемая конструкция; 2 — рабочая арматура восстанавливаемой конструкции; 3 — арматурная сетка из проволоки; 4 — расчищенная поверхность конструкции до бетона с рН і 12; 5 — восстановленный защитный слой из плотного цементно-песчаного раствора.
2.3.l. Восстановлениe несущей способности опорных частей изгибаемых элементов
Восстановление несущей способности изгибаемых элементов при разрушении их опорных частей, равно как и вообще усиление указанных элементов на восприятие поперечных сил, целесообразно в основном производить посредством увеличения сечения поперечной и наклонной арматуры. Простым по трудоемкости способом является усиление вертикальными накладными хомутами (рис. 2.6 и 2.7). Для устройства хомутов необходимо предварительно пробить отверстия в перекрытии с обеих сторон балки. Затем снизу балки в отверстия заводятся хомуты, при этом на нижние грани балки под
хомуты устанавливаются прокладки из уголков. Хомуты должны иметь концы с нарезкой. После подведения хомутов сверху балки на их концы надевается подкладка из полосовой стали и закручиваются гайки. При притягивании хомутов гайки должны закручиваться одновременно на двух концах. При этом способе усиления не требуется каких-либо нарушений поверхности бетона усиливаемых балок.
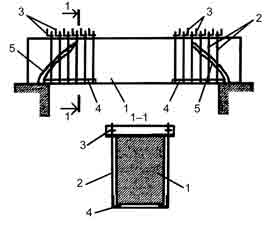
Рис. 2.6. Установка поперечных хомутов: 1 — усиливаемая балка; 2 — хомуты с гайками; 3 — поперечные уголки; 4 — продольные уголки; 5 — трещины в балке.
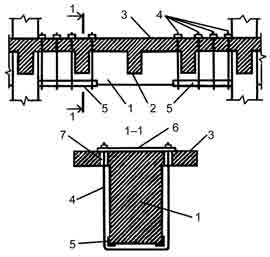
Рис. 2.7. Установка стяжных хомутов у опор: 1 — усиливаемая главная балка; 2 — второстепенные балки; 3 — плита; 4 — металлические стяжные хомуты с гайками; 5 — подкладка из уголка; 6 — прокладка-шайба; 7 — отверстия, просверленные в плите для пропуска хомутов.
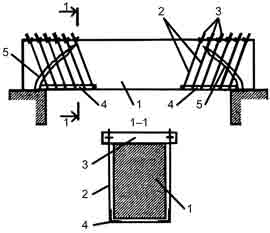
Рис. 2.8. Установка наклонных хомутов: 1 — усиливаемая балка; 2 — наклонные хомуты с гайками; 3 — поперечные уголки; 4 — продольные уголки; 5 — трещины в балке.
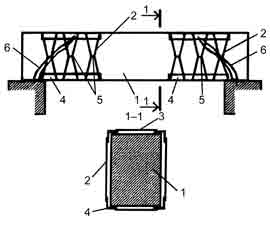
Рис. 2.9. Установка стяжных хомутов: 1 — усиливаемая балка; 2 — поперечные стержни; 3 — соединительные планки; 4 — продольные уголки; 5 — стяжные хомуты; 6 — трещины в балке.
Аналогично производится усиление установкой наклонных хомутов (рис. 2.8). Единственное отличие состоит в том, что нужно предусмотреть мероприятия, исключающие проскальзывание поперечных уголков вдоль балки (например, специальные проточки на поверхности балки или установку конструктивных металлических элементов). Более эффективным способом следует считать усиление предварительно напряженными хомутами, т.к. предварительное напряжение увеличивает нагрузку, воспринимаемую элементами усиления (рис. 2.9 и 2.10). Конструкция предварительно напряженных хомутов состоит из верхних крепежных уголков (в ребристых перекрытиях, подвешиваемых к плите перекрытия на болтах); нижних крепежных уголков, соединенных планками на сварке; четного количества хомутов и стяжных болтов с шайбами-захватами. После приварки хомутов снизу и сверху предварительное напряжение в них создается взаимным стягиванием двух стержней стяжными болтами.
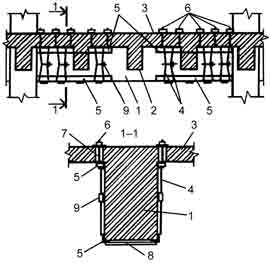
Рис. 2.10. Установка стягиваемых поперечных стержней у опор: 1 — усиливаемая главная балка; 2 — второстепенные балки; 3 — плита; 4 — поперечные стержни, привариваемые к уголкам; 5 — уголки; 6 — крепежные болты; 7 — отверстия, просверленные в плите для установки болтов; 8 — соединительные планки; 9 — стяжные болты.
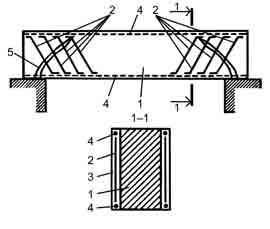
Рис. 2.11. Приварка дополнительных наклонных стержней: 1 — усиливаемая балка; 2 — наклонные стержни, укладываемые в вырубленные борозды и привариваемые к продольной арматуре балок; 3 — цементно-песчаный раствор; 4 — продольная арматура; 5 — трещины в балке.
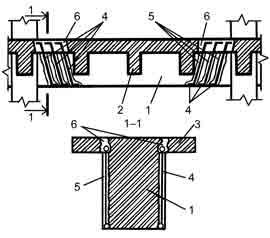
Рис. 2.12. Приварка наклонных стержней у опор: 1 — усиливаемая главная балка; 2 — второстепенные балки; 3 — плита; 4 — наклонные арматурные стержни, привариваемые к оголенной верхней и нижней рабочей арматуре усиливаемой балки; 5 — борозды для установки дополнительных арматурных стержней (после установки стержней заполнить бетоном); 6 — отверстия, пробитые в плите для установки наклонных стержней (после установки стержней заполнить бетоном).
Стягивание стержней необходимо производить одновременно с обеих сторон усиливаемой балки, чтобы избежать кручения последней. По окончании натяжения гайки на болтах рекомендуется заварить. Возможно усиление приваркой дополнительных наклонных арматурных стержней (рис. 2.11 и 2.12.). Этот способ позволяет получить усиление без ухудшения вида балки. Однако при этом способе усиления необходимо предварительно вырубать в боковых гранях балок борозды для установки дополнительных наклонных стержней, которые желательно приваривать к рабочей арматуре балки. Указанные мероприятия нужно проводить при соответствующей разгрузке усиливаемой конструкции, т.к. в процессе работ по установке дополнительных стержней балка ослабляется вследствие разрушения бетона и приварки усиливающих стержней к рабочей арматуре. Указанные обстоятельства существенно осложняют работы по усилению. Известны и другие способы усиления наклонных сечений. Например, установка арматурных стержней на клею в пазы в бетоне, прорезанные фрезой, или наклейка листового металла на боковые грани в местах недостаточной несущей способности.
Сергей ЛЕОНОВИЧ, доктор техн. наук, профессор, зав. кафедрой "Технология строительного производства" БНТУ
2.3. Восстановление несущей способности и усиление железобетонных конструкций
Усиление может производиться как в случае изменения нагрузок на конструкцию, так и при сохранении нагрузок и расчетной схемы. В последнем случае при усилении фактически необходимо восстановить конструкцию в первоначальном (проектном) виде.
Основными примерами восстановления несильно поврежденных конструкций являются мероприятия:
— по заделке трещин в бетонных и железобетонных конструкциях;
— по восстановлению разрушенных защитных слоев бетона;
— по усилению поврежденных опорных частей балок и прочих элементов, работающих на восприятие поперечной нагрузки.
Предполагается, что указанные нарушения в конструкциях возникли вследствие однократного (случайного) воздействия каких-либо внешних факторов. Причем дальнейшая работа конструкции предполагается при воздействии нагрузок, не превышающих проектные. Трещины в бетонных и железобетонных конструкциях заделываются цементно-песчаным раствором или шпаклюются синтетическим материалом. При ширине трещин более 0,3 мм и глубине не более 50 мм трещины заделывают раствором на расширяющемся цементе с водоцементным отношением В/Ц = 0,6-2,0 или синтетической смолой, которые подаются (нагнетаются) растворонасосом в трещину с помощью поверхностного инъектора. Предварительной обработки (разделки трещин, сверления скважин и т.п.) в этом случае не требуется. Единственное, что необходимо сделать перед нагнетанием раствора, — заделать (закрыть) трещину по лицевой поверхности конструкции, оставив промежутки 20-30 см с шагом 0,5-1,5 м незаделанной поверхности. Трещину закрывают лентой или замазывают клеем или бетоном (рис. 2.1).
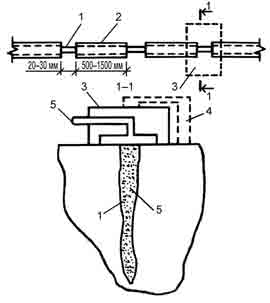
Рис. 2.1. Нагнетание цементно-песчаного раствора при ширине трещин не более 0,3 мм и глубине до 50 мм: 1 — трещина в конструкции; 2 — пространство, заделываемое бетоном, клеем или лентой; 3 — иньектор поверхностного типа; 4 — крепление инъектора (струбцины, болты и др.); 5 — раствор.
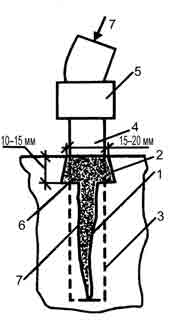
Рис. 2.2. Нагнетание цементно-песчаного раствора при ширине раскрытия трещин менее 0,3 мм: 1 — трещина в конструкции; 2 — расшитая трещина; 3 — просверленное отверстие для постановки и заделки инъекционной трубки; 4 — инъекционная трубка; 5 — штуцер с гайкой для подключения шланга к инъекционной трубке; 6 — цементно-песчаный раствор; 7 — раствор с В/Ц = 0,7-2,0 на расширяющемся цементе.
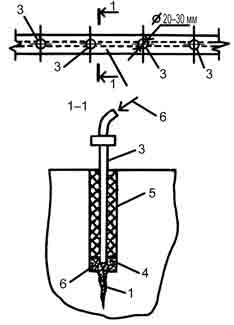
Рис. 2.3. Нагнетание цементно-песчаного раствора при ширине трещин более 0,3 мм и глубине более 50 мм: 1 — трещина в конструкции (глубиной более 50 мм); 2 — пространство, заделываемое бетоном, клеем или лентой; 3 — напорная инъекционная трубка; 4 — просверленная скважина; 5 — резиновый уплотнитель; 6 — раствор с В/Ц = 0,6-2,0 на расширяющемся цементе или синтетические смолы (от растворонасоса).
При ширине раскрытия трещин менее 0,3 мм или более 0,3 мм, но глубине более 50 мм поверхностные инъекторы не применяются. Если трещина узкая (ширина менее 0,3 мм), то раствор нагнетается в трещину под давлением 490-1960 кг/см2 через инъекционные трубки, устанавливаемые в специально просверливаемые в конструкции отверстия (скважины). Верх трещины (около поверхности конструкции) разделывается (расшивается): вдоль всей трещины распиливается расширяющийся вовнутрь конструкции паз, заполняемый цементно-песчаным раствором (состав раствора — 1:1) (рис. 2.2.). При трещинах шириной более 0,3 мм и глубиной более 50 мм раствор на расширяющемся цементе нагнетается в трещину через напорные инъекционные скважины, располагаемые по длине трещины с шагом 1-1,5 м. При этом поверхность трещины между скважинами закрывается (заделывается) аналогично тому, как делается в случае трещин глубиной до 50 мм (рис. 2.3). Короткие и неглубокие трещины предварительно разделывается фрезой до ширины более 10 мм. После этого они заполняются раствором на расширяющемся цементе или синтетической смолой. При больших повреждениях (широких трещинах), кроме заделки собственно трещины, рекомендуется усиливать конструкцию обоймой или рубашками из железобетона. Для изготовления раствора во всех случаях заделки трещин рекомендуется применять глиноземистый расширяющийся цемент марок 400, 500 или напрягающий цемент НЦ-20. Расход цемента должен быть не менее 400 кг/м3. После заделки трещин должна быть дана выдержка при положительной температуре или паропрогрев при температуре 50°С на расширяющемся цементе и 50°-60°С — на напрягающем цементе.
Восстановление защитного слоя бетона производится путем:
— оштукатуривания конструкции плотным цементно-песчаным раствором с возможным нанесением по нему трещиностойкого лакокрасочного покрытия;
— обетонирования цементным бетоном или полимербетоном, имеющим прочность не ниже прочности бетона восстанавливаемой конструкции;
— торкретирования плотным цементно-песчаным раствором.
При всех способах восстановления защитного слоя бетона предварительно производится подготовка усиливаемых конструкций. Перед работами по обработке поверхности визуально и простукиванием молотком уточняют размеры зон, с которых удаляют низкопрочный бетон. Дефектные участки определяют по отслоению защитного слоя, наличию мелкой сетки трещин на поверхности, коррозии бетона, следов ржавчины, глухому звуку при ударе, отслоению защитного слоя при простукивании и др. Удалять низкопрочный бетон следует оконтуриванием дефектных зон бороздой, постепенно ее затем углубляя внутри дефектной зоны.
Разрушенный по периметру сечения в изгибаемых конструкциях бетон следует обрубать вертикально, в сжатых конструкциях — горизонтально. Для улучшения сцепления с вновь укладываемым бетоном поверхность конструкций должна быть подвержена механической обработке. При малых объемах работ механическая обработка поверхности выполняется при помощи ручного, электрического и пневматического инструментов (щеток, пучковых молотков и т.п.). При больших объемах работ — гидроабразивным способом с использованием оборудования для набрызга бетона (пульпа приготавливается из трех частей песка и семи частей воды), пескоструйным и термоструйным способами с использованием аппаратов ТСА-12 и ТА-12. При необходимости приварки коротышей, соединительных скоб существующая арматура вскрывается в местах их установки не менее чем на половину своего диаметра участками, превышающими длину соединительных деталей на 10-15 мм. Пыль с обрабатываемой поверхности смывается. Поверхность конструкции расчищается на глубину, где бетон имеет водородный показатель рН і 12. После расчистки поверхности конструкций от "слабого" бетона необходимо очистить рабочую арматуру восстанавливаемой конструкции от продуктов коррозии. Это производится в зависимости от объема работ зубилом, стальными щетками, скребками или при помощи пескоструйного аппарата. При восстановлении защитного слоя оштукатуриванием очищенная арматура покрывается казеиновым слоем с замедлителем коррозии. Состав этого покрытия в частях по массе: портландцемент — 100; вода — 30-40; нитрат натрия — 10; казеиновый клей — 5. Состав цементно-песчаного раствора, наносимого в виде штукатурки — 1:2,5-1:3. После оштукатуривания при отсутствии покрытия арматуpы казеиновым клеем поверхность штукатурки покрывается лакокрасочным покрытием, состав которого выбирается в соответствии со степенью агрессивности среды согласно нормам.
При обетонировании конструкции цементный бетон должен иметь прочность не ниже прочности конструкции. Перед обетонированием расчищенная поверхность конструкции увлажняется и может быть покрыта слоем цементно-песчаного раствора состава 1:2. Восстанавливаемый защитный слой (наносимый обетонированием или торкретированием) в последнем случае должен быть уложен через 90 мин. после нанесения слоя цементно-песчаного раствора. При применении для восстановления защитного слоя полимербетона возможный его состав (в частях по массе) следующий: эпоксидная смола — 100; каменноугольный лак — 100; жидкий тиокол — 20; отвердитель ПЭПА — 10; цемент — 100-150. В случае коррозии арматуры для компенсации прокорродировавшей ее части применяют накладки из арматурной стали, привариваемые к рабочей арматуре (рис. 2.4). При восстановлении защитного слоя бетона торкретированием плотным цементно-песчаным раствором (рис. 2.5) к рабочей арматуре конструкции приваривается арматурная сетка из проволоки диаметром 2-3 мм и ячейкой »50х50 мм. Применяют цементно-песчаный раствор состава 1:1-1:1,5 на портландцементе марки 400-500 или аналогичном по марке глиноземистом цементе при его расходе не менее 400 кг/м3.
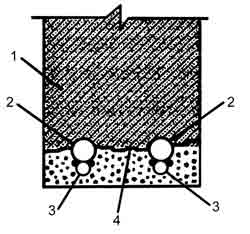
Рис. 2.4. Обетонирование цементным бетоном: 1 — восстанавливаемая конструкция; 2 — рабочая арматура восстанавливаемой конструкции; 3 — накладки из арматурной стали, приваренные к рабочей арматуре; 4 — расчищенная поверхность конструкции; 5 — восстановленный защитный слой бетона, наносимый обетонированием или торкретированием.
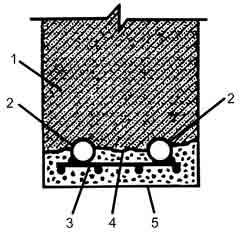
Рис. 2.5. Торкретирование плотным цементно-песчаным раствором: 1 — восстанавливаемая конструкция; 2 — рабочая арматура восстанавливаемой конструкции; 3 — арматурная сетка из проволоки; 4 — расчищенная поверхность конструкции до бетона с рН і 12; 5 — восстановленный защитный слой из плотного цементно-песчаного раствора.
2.3.l. Восстановлениe несущей способности опорных частей изгибаемых элементов
Восстановление несущей способности изгибаемых элементов при разрушении их опорных частей, равно как и вообще усиление указанных элементов на восприятие поперечных сил, целесообразно в основном производить посредством увеличения сечения поперечной и наклонной арматуры. Простым по трудоемкости способом является усиление вертикальными накладными хомутами (рис. 2.6 и 2.7). Для устройства хомутов необходимо предварительно пробить отверстия в перекрытии с обеих сторон балки. Затем снизу балки в отверстия заводятся хомуты, при этом на нижние грани балки под
хомуты устанавливаются прокладки из уголков. Хомуты должны иметь концы с нарезкой. После подведения хомутов сверху балки на их концы надевается подкладка из полосовой стали и закручиваются гайки. При притягивании хомутов гайки должны закручиваться одновременно на двух концах. При этом способе усиления не требуется каких-либо нарушений поверхности бетона усиливаемых балок.
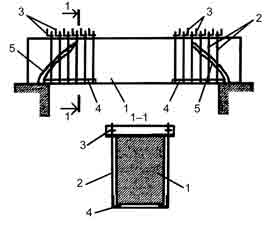
Рис. 2.6. Установка поперечных хомутов: 1 — усиливаемая балка; 2 — хомуты с гайками; 3 — поперечные уголки; 4 — продольные уголки; 5 — трещины в балке.
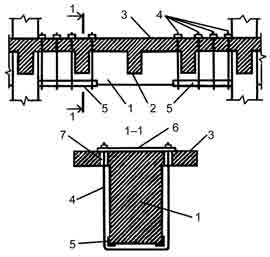
Рис. 2.7. Установка стяжных хомутов у опор: 1 — усиливаемая главная балка; 2 — второстепенные балки; 3 — плита; 4 — металлические стяжные хомуты с гайками; 5 — подкладка из уголка; 6 — прокладка-шайба; 7 — отверстия, просверленные в плите для пропуска хомутов.
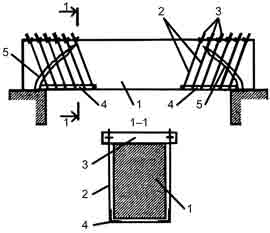
Рис. 2.8. Установка наклонных хомутов: 1 — усиливаемая балка; 2 — наклонные хомуты с гайками; 3 — поперечные уголки; 4 — продольные уголки; 5 — трещины в балке.
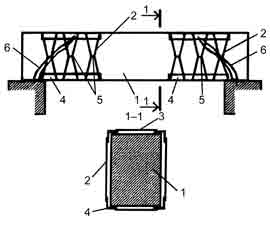
Рис. 2.9. Установка стяжных хомутов: 1 — усиливаемая балка; 2 — поперечные стержни; 3 — соединительные планки; 4 — продольные уголки; 5 — стяжные хомуты; 6 — трещины в балке.
Аналогично производится усиление установкой наклонных хомутов (рис. 2.8). Единственное отличие состоит в том, что нужно предусмотреть мероприятия, исключающие проскальзывание поперечных уголков вдоль балки (например, специальные проточки на поверхности балки или установку конструктивных металлических элементов). Более эффективным способом следует считать усиление предварительно напряженными хомутами, т.к. предварительное напряжение увеличивает нагрузку, воспринимаемую элементами усиления (рис. 2.9 и 2.10). Конструкция предварительно напряженных хомутов состоит из верхних крепежных уголков (в ребристых перекрытиях, подвешиваемых к плите перекрытия на болтах); нижних крепежных уголков, соединенных планками на сварке; четного количества хомутов и стяжных болтов с шайбами-захватами. После приварки хомутов снизу и сверху предварительное напряжение в них создается взаимным стягиванием двух стержней стяжными болтами.
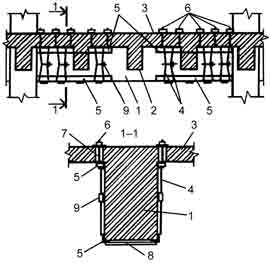
Рис. 2.10. Установка стягиваемых поперечных стержней у опор: 1 — усиливаемая главная балка; 2 — второстепенные балки; 3 — плита; 4 — поперечные стержни, привариваемые к уголкам; 5 — уголки; 6 — крепежные болты; 7 — отверстия, просверленные в плите для установки болтов; 8 — соединительные планки; 9 — стяжные болты.
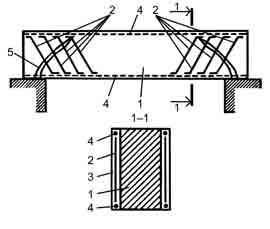
Рис. 2.11. Приварка дополнительных наклонных стержней: 1 — усиливаемая балка; 2 — наклонные стержни, укладываемые в вырубленные борозды и привариваемые к продольной арматуре балок; 3 — цементно-песчаный раствор; 4 — продольная арматура; 5 — трещины в балке.
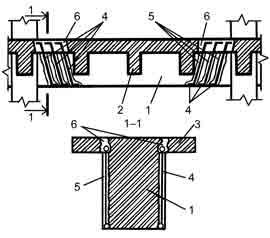
Рис. 2.12. Приварка наклонных стержней у опор: 1 — усиливаемая главная балка; 2 — второстепенные балки; 3 — плита; 4 — наклонные арматурные стержни, привариваемые к оголенной верхней и нижней рабочей арматуре усиливаемой балки; 5 — борозды для установки дополнительных арматурных стержней (после установки стержней заполнить бетоном); 6 — отверстия, пробитые в плите для установки наклонных стержней (после установки стержней заполнить бетоном).
Стягивание стержней необходимо производить одновременно с обеих сторон усиливаемой балки, чтобы избежать кручения последней. По окончании натяжения гайки на болтах рекомендуется заварить. Возможно усиление приваркой дополнительных наклонных арматурных стержней (рис. 2.11 и 2.12.). Этот способ позволяет получить усиление без ухудшения вида балки. Однако при этом способе усиления необходимо предварительно вырубать в боковых гранях балок борозды для установки дополнительных наклонных стержней, которые желательно приваривать к рабочей арматуре балки. Указанные мероприятия нужно проводить при соответствующей разгрузке усиливаемой конструкции, т.к. в процессе работ по установке дополнительных стержней балка ослабляется вследствие разрушения бетона и приварки усиливающих стержней к рабочей арматуре. Указанные обстоятельства существенно осложняют работы по усилению. Известны и другие способы усиления наклонных сечений. Например, установка арматурных стержней на клею в пазы в бетоне, прорезанные фрезой, или наклейка листового металла на боковые грани в местах недостаточной несущей способности.
Сергей ЛЕОНОВИЧ, доктор техн. наук, профессор, зав. кафедрой "Технология строительного производства" БНТУ
Строительство и недвижимость. Статья была опубликована в номере 39 за 2004 год в рубрике уголок эксперта