Об оборудовании стеклозаводов
ОАО "Союзстекломаш" (Москва) — ведущий институт российской стекольной отрасли, который на протяжении более чем 50 лет проектирует и внедряет на стекольных заводах современное высокопроизводительное автоматизированное оборудование, позволяющее изготавливать различные изделия из стекла и стеклокристаллических материалов.
ОАО "Союзстекломаш" конструирует, изготавливает и поставляет технологическое и общезаводское оборудование для производства листового флоат-стекла (производительностью от 100 до 800 т/сут), листового прокатного стекла (производительностью от 20 до 120 т/сут, в том числе профилита), листовых стеклокристаллических материалов (ситалла, сиграна, шлакоситалла, в составе линии прокатная машина, кристаллизатор и оборудование для резки ленты), других видов строительного и технического стекла (коврово-мозаичной плитки, стеклотруб, армированного и узорчатого стекла, электроизоляторов).
Кроме того, ОАО "Союзстекломаш" разрабатывает и обеспечивает поставку отдельных видов стекольного оборудования различного назначения — смесителей и широкостольных загрузчиков шихты, машин центробежного формования, дробилок стекла, линий для обработки фацета и кромки стекла, питателей стекломассы для стеклоформующих машин секционного и роторного типов, стеклоформующих автоматов секционного и роторного типов, контрольно-сортировочных автоматов для стеклотары, станков для двустороннего сверления листов стекла.
В составе технологического оборудования, о котором идет речь, применены оригинальные конструкции, защищенные патентами России. На оборудовании, изготовленном по чертежам института, работают линии полированного стекла на Салаватском, Саратовском, Гомельском, Токмакском стекольных заводах.
Оборудование
Линия обработки кромок
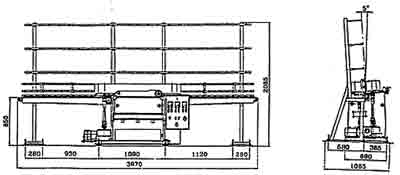
ЛОК (рис. 1) предназначена для получения ровной обработанной кромки с притупленными гранями на прямолинейных участках листового стекла.
Линия состоит из остова рамы неподвижной и рамы прижимной с конвейерными цепями. Под рамами установлены три шлифовальные головки. К остову крепятся транспортеры загрузки и выгрузки стекла и рольные опоры. Лист стекла устанавливается вручную на транспортер загрузки, прижимается к рольной опоре и транспортируется к конвейерным цепям.
Конвейерные цепи зажимают лист стекла и перемещают его вдоль обрабатывающих головок, а после обработки кромки выдают на транспортер выгрузки. Для охлаждения инструмента линия оснащена электронасосом, подающим воду в зону резания. Вода циркулирует в замкнутом цикле. Скорость обработки кромки регулируется изменением числа оборотов электродвигателя главного привода частотным преобразователем.
Обработка кромки производится алмазным инструментом различной зернистости диаметром 150 мм. Притупление острых граней осуществляется вулканитовым кругом. Производительность линии (в зависимости от толщины стекла) — 0,38-3,8 м/мин.
Возможна обработка листов длиной 200-1600 мм, высотой 200-1600 мм, толщиной 2-12 мм. Количество головок с алмазными кругами — 2, с вулканитовым кругом—1.
Транспортирующий орган — замкнутые конвейерные цепи с обрезиненными пластинами. Положение транспортируемых под углом листов стекла — 5° к вертикали. Производительность помпы подачи смазочно-охлаждающей жидкости — 32 л/мин.
Характеристика питающей сети: трехфазный переменный ток частотой 50 Гц, напряжение 380 В, допустимые колебания напряжения — от +10% до -15%, допустимые колебания частоты — плюс-минус 1 Гц. Потребляемая мощность — не более 7 кВт.
Линия обработки фацета
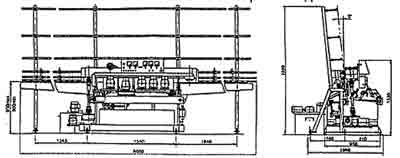
ЛОФ5 (рис. 2) предназначена для получения полированного фацета на прямолинейных участках листового стекла.
Линия состоит из остова, на верхней части которого установлены балка неподвижная и балка прижимная с конвейерными цепями. Под балками установлены головки: полировальная, кромочная, шлифовальные. К торцам остова крепятся транспортеры загрузки и выгрузки стекла, а также рольные опоры. Обрабатываемый лист стекла устанавливается вручную на транспортер загрузки, прижимается к рольной опоре и транспортируется к конвейерным цепям. Конвейерные цепи зажимают лист стекла и перемещают его вдоль обрабатывающих головок, а после обработки фацета выдают на транспортер выгрузки. Для охлаждения инструмента линия оснащена электронасосом, подающим воду в зону резания, и установкой подачи суспензии в зону полирования фацета. Вода и полирующая жидкость циркулируют в замкнутом цикле. Скорость обработки фацета регулируется изменением числа оборотов электродвигателя главного привода частотным преобразователем. Обработка фацета и кромки производится алмазным инструментом различной зернистости диаметром 150 мм, а полировка — войлочным кругом.
Ширина фацета — до 40 мм. Угол фацетирования — от 5 до 20°. Количество шлифовальных головок — 3, головок обработки кромки — 1, полировальных головок — 1. Производительность помпы подачи смазочно-охлаждающей жидкости, как и производительность помпы подачи суспензии — 32 л/мин. Остальные параметры аналогичны таковым ЛОК.
Смеситель СШ 2250 для приготовления стекольной шихты
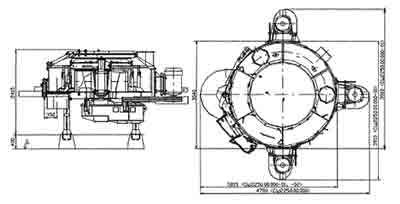
СШ2250 (рис. 3) предназначен для смешивания многокомпонентной шихты различного химического состава.
Привод смесителя снабжен специальным двухступенчатым редуктором с цилиндрическими шестернями в горизонтальном исполнении. Ротор, несущий смешивающие и чистящие лопасти, соединен с приводом посредством шлицевого соединения. Трансмиссия от мотора к редуктору осуществляется клиноременной передачей. Нижнее расположение редуктора обеспечивает свободный доступ к лопастям для замены или ремонта. Стержни, несущие лопасти, свободно закреплены на роторе и имеют возможность поглощать удары, возникающие от случайных частиц большого размера или камней. При износе лопастей их пространственное расположение можно изменить путем регулировки. Смеситель снабжен механизмом для централизованной подачи смазки к подшипникам качения. Смесители используются вместе с автоматической линией взвешивания компонентов.
Производительность при полном цикле смешивания, равном 6 минутам, — 28.000 кг/час. Объем загружаемой шихты — 2.250 л. Мощность электродвигателя — 55 кВт. Частота вращения ротора — 23,7 об/мин. Диаметр чаши — 2.900 мм.
Молотковая дробилка
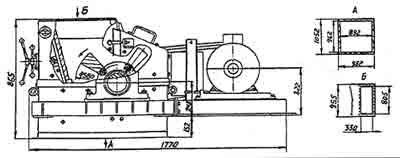
Молотковая дробилка модели ДМ-40 (рис. 4) предназначена для дробления отходов (стеклобоя) при производстве листового стекла и стеклоизделий.
Размер частиц после дробления — до 15-30 мм. Дробилка состоит из сварного корпуса, в котором расположен горизонтальный ротор, выполненный в виде ряда дисков, насаженных на вал; по периферии дисков пропущены стержни, несущие шарнирно смонтированные на них молотки (била). Вал ротора смонтирован на двух опорах качения, расположенных с наружных сторон корпуса. Привод ротора от электродвигателя постоянного тока через клиноременную передачу. Внутри корпуса расположена отбойная плита, верхний торец которой шарнирно соединен со стенками корпуса, а положение нижнего торца регулируется с помощью двух винтов, чем обеспечивается изменение зазора между плитой и молотками для получения требуемой крупности дробления. Внутренние стенки корпуса и крышек, а также рабочая поверхность отбойной плиты облицованы сменными броневыми листами; молотки и броневые листы выполнены из высокоизносостойкой марганцовистой стали. Дробление стекла происходит при встрече подаваемого в дробилку стекла с вращающимися шарнирно закрепленными молотками. Оптимальный режим дробления — примерно 760 об/мин двигателя, что соответствует 675 об/мин ротора. При этом окружная скорость молотков составляет 20,5 м/сек.
Производительность — до 40 т/час. Номинальная частота вращения ротора — 675 об/мин, максимальная — 1240, минимальная — 417 об/мин. Зазор между вращающимися молотками и отбойной плитой составляет 10-40 мм. Напряжение питания трехфазное (380 В, 50 Гц). Мощность электродвигателя — 18,5 кВт. Размер загрузочного окна — 805х330, разгрузочного — 962х892 мм.
Автомат контроля
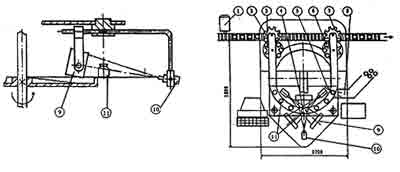
Автомат контроля (рис. 5) предназначен для контроля геометрических параметров стеклоизделий и наличия посечек и сколов на их венчиках.
Принцип работы основан на анализе изображений контролируемых стеклоизделий и сравнивании их параметров с эталоном. На виде 1 показана оптическая схема работы автомата. Три оптических видеокамеры 10 и три экрана 9 установлены на выносных консолях друг напротив друга, и их оптические оси смещены на 120°. При попадании стеклоизделия 11 в зону видимости видеокамер происходит формирование изображения на фоне светящегося экрана.
Источником излучения экранов является матрица светодиодов, работающих в импульсном режиме. Изображение стеклоизделия с видеокамеры через плату ввода подается в ПК, где сравнивается с эталоном — в случае отклонения каких-либо параметров от заданных подается сигнал на пневмоклапан для сброса бракованного изделия. Автомат снабжен автоматической системой синхронизации скорости работы автомата и транспортера подачи банок.
После небольшой переналадки автомат можно использовать для контроля различных по высоте и диаметру стеклоизделий. При поломке автомата устройство легко отстыковывается и откатывается от транспортера. На виде 2 показана схема работы автомата. Стеклоизделие 11 с основного транспорта 1 уводится приемной звездочкой 2 и ставится на делительную звездочку 3, которая разгоняет стеклоизделие до скорости установочного диска 4 и ставит ее на диск с определенным интервалом. Установочный диск в процессе своего вращения подводит стеклоизделие к точке контроля (пересечения оптических осей видеокамеры 10), где происходит снятие параметров изделия и в случае брака подается сигнал на пневмоклапан 5 на сброс бракованного изделия в лоток брака 8. Качественные стеклоизделия снимаются с установочного диска возвратной звездочкой 6, на которой скорость стеклоизделия замедляется до скорости транспортера, и изделие с помощью звездочки сброса возвращается на него.
Размеры стеклоизделия: диаметр — 50-150, высота — 70-250 мм. Контролируемые параметры стеклоизделия — высота, диаметр корпуса, диаметр резьбы венчика, диаметр основания резьбы, отклонение от параллельности плоскости торца венчика, вогнутость торца венчика горловины, сдвиг оси горловины относительно вертикальной оси банки, трещины и посечки.
Абсолютная погрешность измерения — 0,1 мм. Скорость работы автомата — 150 шт./ мин., давление управляющего воздуха — 0,2-0,6 МПа, потребляемая мощность — 300 Вт.
Подготовил Владимир ДАНИЛОВ
Строительство и недвижимость. Статья была опубликована в номере 01 за 2004 год в рубрике энергетика