Некоторые особенности влияния добавок водных дисперсий полимеров на стойкость цементных систем в химически агрессивных средах
Некоторые особенности влияния добавок водных дисперсий полимеров на стойкость цементных систем в химически агрессивных средах
Распространенность природных и промышленных сред, содержащих высокие концентрации хлоридов и сульфатов, приводящих к коррозии строительных конструкций и изделий на основе портландцемента, обусловила необходимость разработки способов получения бетонов, максимально стойких в таких средах без применения вторичной защиты.
Выбор того или иного способа предотвращения коррозии бетона и железобетона в конструкциях и изделиях, гарантирующего требуемую долговечность сооружения в целом, обусловлен в первую очередь требованиями технико-экономической целесообразности и техническими возможностями строительства. Это позволяет, как правило, существенно сократить объем и стоимость ремонтно-восстановительных ра-бот, а в отдельных случаях полностью исключить их и обеспечить проектные сроки долговечности сооружений.
Возросшая за последние десятилетия потребность в бетонах, отвечающих специфическим требованиям по морозостойкости, стойкости к различным агрессивным средам, плотности привела к тому, что наиболее актуальным направлением на современном этапе развития строительного производства стала химизация этой отрасли. Использование различных органических и неорганических соединений в качестве специальных добавок к бетону приводит к существенному изменению химических процессов твердения бетона, обеспечивающих улучшение его механических и физико-химических свойств. Этими добавками являются модификаторы бетона, воздействие которых существенно изменяет структуру и свойства материала за счет введения определенных веществ при практически неизменном количестве основных составляющих.
Основываясь на современных представлениях о физико-химических поверхностных явлениях и теории контактных взаимодействий, введением химических специфических добавок (модификаторов) в цементные системы можно изменить в нужном направлении свойства цементного теста, бетонной смеси и самого бетона. Наиболее полно проблемы модифицированных бетонов с учетом отечественного и зарубежного опыта изложены в монографии В.Г. Батракова "Модифицированные бетоны. Теория и практика" (изд. 2-е, перераб. и дополн. — М.: “Стройиздат”, 1998). Основным в теоретическом и практическом плане вопросом модифицирования цементных систем представляется установление взаимосвязи между составом, строением модификаторов и их ролью в процессах гидратации и формирования структуры вяжущих различного минералогического и вещественного состава. Принципы классификации модификаторов могут быть следующими: по механизму действия на основные составляющие цемента, по химическому составу модификаторов, а также по функциональным признакам (основной технологический эффект действия в цементных системах).
Отечественная классификация модификаторов (ГОСТ 24211-91 “Добавки для бетонов. Общие технические требования”) основана на учете преимущественного технологического эффекта.
Поиски путей повышения прочности, плотности, химической стойкости и долговечности бетона привели к созданию обширной группы бетонов с добавками и на основе полимеров, которые получили общее название П-бетоны.
В соответствии с общепринятой классификацией специальные бетоны с добавками или на основе полимеров по составу и способу приготовления делятся на четыре основные категории: бетоны на основе полимерных связующих — полимербетоны (ПБ); цементные бетоны, модифицированные полимерами, — полимерцементные бетоны (ПЦБ); серные бетоны, модифицированные полимерами, — полимерсерные бетоны (ПСБ); цементные бетоны, пропитанные мономерами или олигомерами, — бетонополимеры (БП) (рис.1).
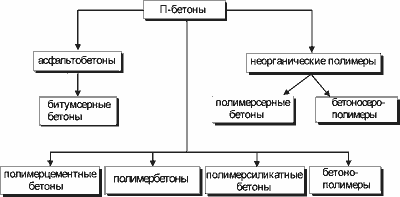
Рис.1. Классификация П-бетонов
Так как бетон и железобетон на цементной основе в настоящее время являются основными конструкционными материалами в строительстве, то наибольший интерес с точки зрения повышения их долговечности представляют полимерцементные бетоны, то есть бетоны на цементном вяжущем, модифицированные полимерами. Наиболее перспективными для промышленного применения модификаторами такого вида являются водные дисперсии полимеров, объем и ассортимент выпуска которых постоянно возрастает в химической промышленности как в России, так и за рубежом.
Исследование процессов модификации цементных систем различными химическими добавками достаточно детально изложено в вышеупомянутой монографии Батракова, а их применение — в книге "Добавки в бетон. Справочное пособие" (М.: “Стройиздат”, 1988).
Долговечность строительного материала может быть определена как способность материала или конструкции из него противостоять воздействию агрессивной среды и сохранять эксплуатационную пригодность в течение определенного заданного в проекте срока службы. При этом долговечность будет определяться свойствами бетона конструкции, химическим составом среды и условиями взаимодействия среды с конструкцией.
На свойства модифицированных водными дисперсиями полимеров растворов и бетонов и их особенности в процессе изготовления влияет множество факторов, в том числе тип полимера, полимерцементное отношение, водоцементное отношение, содержание вовлеченного воздуха и условия выдержки.
Направленная модификация бетонов и растворов на основе портландцемента за счет введения водной дисперсии происходит вследствие изменения процесса гидратации цемента и процессов образования полимерной пленки в связывающей их фазе. Причем процесс гидратации цемента обычно предшествует процессу образования полимерной пленки.

Рис.2. Упрощенная модель образования полимерцементной соматрицы: а) сразу после смешивания; б) первая фаза; в) вторая фаза; г) третья фаза (затвердевшая структура); 1) негидратированные цементные частицы; 2) полимерные частицы; 3) заполнители (промежуточное пространство заполнено водой); 4) смеси негидратированных частиц цемента и цементного геля, на которых частично осаждаются полимерные частицы; 5) смеси цементного геля и негидратированных частиц цемента, окруженных плотно упакованным слоем полимерных частиц; 6) гидраты цемента, окруженные полимерными пленками или мембранами; 7) вовлеченный воздух
Многочисленные исследования показали, что соматричная фаза, которая состоит из цементного геля и полимерной пленки, является связующим — в соответствии с упрощенной моделью, показанной на рис.2. Процесс образования полимерной пленки представлен на рис.3.
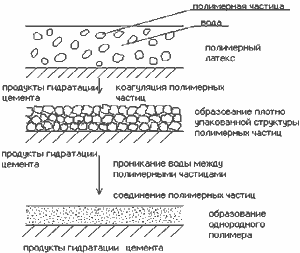
Рис.3. Упрощенная модель процесса образования полимерной пленки на продуктах гидратации цемента
Основной критерий полимерцементов — полимерцементное отношение (П/Ц), или в общем виде полимервяжущее (П/В) отношение, определяемое как отношение масс исходных полимера (в расчете на сухое вещество) и цемента (неорганического вяжущего вещества), взятых для изготовления полимерцементного материала, изделия или конструкции. Значение полимерцементного отношения характеризует состав смешанного органо-минерального вяжущего. Качество и количество заполнителя определяются дополнительными требованиями к материалу.
Изменение отношения П/Ц приводит к качественному изменению структуры полимерцемента (рис.4). Полимерная фаза в отвердевшем полимерцементе может образоваться при П/Ц больше 0,02-0,04, и, следовательно, от такого количества полимерной добавки получается полимерцемент, в отличие от цементного бетона, в том числе бетона с органическими пластифицирующими добавками.
При П/Ц менее 0,2 (при применении водных дисперсий полимеров) сросшиеся цементные новообразования создают кристаллизационно-коагуляци-онную структуру. Образовавшийся жесткий пространственный неогранический скелет укрепляется в ослабленных дефектных точках (поры, трещины) со скопившимся в них полимером, что приводит к созданию композиционного материала с повышенными прочностью и эластичностью благодаря шарнирному соединению блоков сросшихся гидратных новообразований более гибкими частицами, сетками и пленками прочных и эластичных органических полимеров, обладающих, к тому же, адгезионными свойствами.
Полимерцементы с П/Ц до 0,2-0,25 являются полимерцементами первого рода (собственно полимерцементами). В случае большого полимерцементного отношения полимер создает непрерывную пространственную конденсационную структуру, которая имеет тем большую жесткость, чем больше и чем лучше там развиты местные блоки гидратных новообразований (см. рис.4б). Это — полимерцементы второго рода. Полимерцементное отношение, при котором изменяется структура полимерцемента, определяется величиной полимерцементных частиц. Для каждой формы полимерной добавки существует своя оптимальная величина П/Ц.
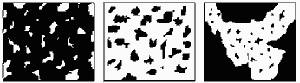
Рис.4. Схематическое строение отвердевшей системы органический полимер — неорганическое вяжущее вещество; темное поле — неорганическое вяжущее, светлое — органический полимер; а) и б) — макростроение системы: а) с преобладанием неорганического вяжущего вещества при П/Ц < 0,2; б) с преобладанием полимера при П/Ц >0,2; в) микростроение полимерной фазы с субмикроскопическими включениями аморфных гидратных новообразований
Известно, что химическая стойкость модифицированных растворов и бетонов зависит от природы полимеров, полимерцементного отношения и свойств агрессивных химических веществ. Большинство модифицированных растворов и бетонов чувствительно к действию неорганических или органических кислот и сульфатов, так как они содержат гидратированный цемент, который не обладает стойкостью к этим веществам, но стоек к щелочам и различным солям, кроме сульфатов. Модифицированные растворы и бетоны отличаются химической стойкостью по отношению к эфирам и маслам, но они не устойчивы к действию органических растворителей.
Химическая стойкость некоторых растворов, содержащих синтетические и природные каучуковые латексы, приведена в работе Y. Ohama "Durability Performance of Polymer-Modified Mortars" (Proceedings of the Second International Conference on Durability of Building Materials and Components, Gaitherburg, USA, 242-248, 1981).
Анализ приведенных результатов позволил выделить два основных требования к водным дисперсиям, удовлетворение которым позволит обеспечить высокую химическую стойкость полимерцементных растворов в агрессивных средах. Это возможность совмещения с цементными системами (в том числе агрегативная устойчивость и стойкость полимера к воздействию щелочей) и стойкость полимера дисперсии к воздействию солей, кислот, органических растворителей и масел.
С точки зрения повышения коррозионной стойкости цементных систем наибольший интерес представляет изучение влияния добавления водной дисперсии полимера на химическую стойкость образующегося материала в тех или иных химически агрессивных средах. Так как стойкость модифицированной водной дисперсией полимера цементной системы в основном будет предопределяться свойствами полимерцементной матрицы (при условии применения химически инертных к агрессивной среде заполнителей и наполнителей), то наши исследования по созданию полимерцементных бетонов и растворов повышенной коррозионной стойкости были начаты с выбора водной дисперсии, удовлетворяющей указанным выше критериям.
Таким образом, на первом этапе основным критерием отбора дисперсий для проведения исследований стала именно химическая стойкость полимера, образующего дисперсию. Сравнительный анализ данных (Г. М. Кондрашов. "Бетоны повышенной коррозионной стойкости, пропитанные водными дисперсиями", канд. дисс., 1985 г.) показал, что максимальной химической стойкостью обладают сополимеры винилхлорида: ВХВД-65 “А”, ВХВД-65 “Б”, А-15, А-25, СВХ-I, СВХ-II, ВДВХМк-65Е-ВДК. Проведенные эксперименты показали, что из всех вышеперечисленных латексов удовлетворительной агрегативной стойкостью в цементных растворах обладает только водная дисперсия ВДВХМк-65Е-ВДК (введение остальных латексов в цементные растворы приводит к их коагуляции). Поэтому в дальнейших исследованиях использовался латекс ВДВХМк-65Е-ВДК.
Эксперименты по определению влияния полимерцементного соотношения на химическую стойкость полимерцементной матрицы проводились на цементных растворах при варьировании П/Ц от 0,01 до 0,2 и водоцементном отношении 0,25. Концентрацию агрессивной среды во время испытания поддерживали с погрешностью до 1%. Для исключения влияния накапливающихся продуктов разложения агрессивная среда в процессе испытаний заменялась не реже одного раза в двое суток. В качестве наиболее агрессивной среды применяли соляную кислоту 5%-й концентрации. На рис.5-6 представлены полученные зависимости влияния агрессивной среды на изменение массы модифицированных цементных растворов под влиянием 5%-й соляной кислоты для различных значений П/Ц при статическом воздействии соляной кислоты и при сочетании статического воздействия этой кислоты и периодического механического удаления продуктов коррозии с поверхности испытуемых образцов (жирной линией показана зависимость потери массы от времени выдержки в агрессивной среде для контрольных образцов, то есть без добавки дисперсии полимера). Обработка полученных значений с помощью приемов корреляционного анализа на ЭВМ позволила установить, что зависимость потери массы образцов при всех значениях полимерцементного соотношения от времени воздействия агрессивной среды подчиняется линейной зависимости с достоверностью не менее 0,95 как при механическом удалении продуктов коррозии с поверхности образцов, так и без их удаления.
Увеличение абсолютных значений потери массы при механическом удалении продуктов коррозии с поверхности испытуемых образцов по сравнению с образцами, продукты коррозии с которых не удалялись, вполне закономерно. Однако обращает на себя внимание тот факт, что при проведении экспериментов, в которых продукты коррозии не удалялись, увеличение значений П/Ц приводит к снижению потери массы испытуемых образцов (см. рис.5), в то же время механическое удаление продуктов коррозии в процессе проведения экспериментов (см. рис.6) привело к существенному изменению зависимости потери массы образцов от значения П/Ц: при П/Ц=0,1 скорость разрушения полимерцементных образцов оказалась минимальной, при всех остальных значениях П/Ц скорость разрушения образцов мало зависит от П/Ц. По нашему мнению, полученный результат объясняется следующим обстоятельством.
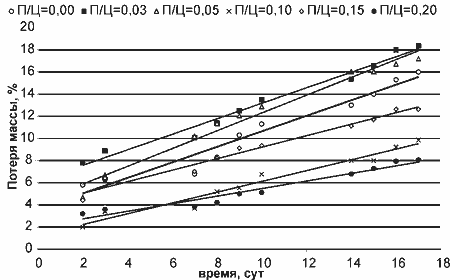
Рис.5. Зависимости потери массы модифицированных цементных растворов под влиянием 5%-й соляной кислоты для различных значений П/Ц при статическом воздействии кислоты
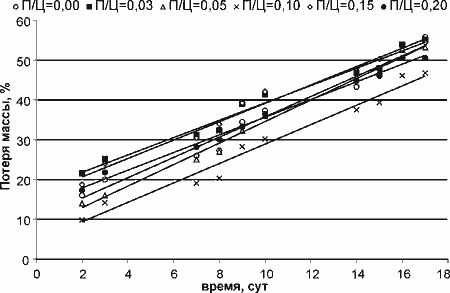
Рис.6. Зависимости потери массы модифицированных цементных растворов под влиянием 5%-й соляной кислоты для различных значений П/Ц при одновременном статическом воздействии кислоты и периодическом механическом удалении продуктов коррозии с поверхности образцов
Поскольку сам полимер стоек к воздействию соляной кислоты, то снижение массы образцов, в которых продукты коррозии не удалялись, обусловлено только растворением компонентов цементного камня. С увеличением содержания полимера в полимерцементе также увеличивается и содержание полимера в образующихся продуктах коррозии, что, в свою очередь, затрудняет массоперенос и доступ агрессивной среды к неразрушенной области полимерцемента, а также прочность сцепления продуктов коррозии с неразрушенным полимерцементом. Наблюдаемое увеличение скорости разложения полимерцементных образцов при П/Ц 0,05 по сравнению с контрольными образцами, по-видимому, связано с увеличением воздухововлечения и количества открытых пор в структуре образовавшегося материала за счет ПАВ, содержащихся в водной дисперсии полимера. Причем при этих значениях П/Ц наиболее вероятной структурой образующего материала является структура, показанная на рис.4 (а). Увеличение П/Ц свыше 0,05, по-видимому, приводит к образованию как непрерывной полимерной фазы (см. рис.3 и рис.4б), так и соматричной фазы (см. рис.2) и как следствие к изменению структуры материала и увеличению количества закрытых пор.
В случае механического удаления продуктов коррозии с поверхности испытуемых образцов затруднение доступа агрессивной среды к полимерцементным образцам и массопереноса за счет плотно сцепленного с образцом слоя продуктов коррозии не происходит. Таким образом, химическая стойкость полимерцементного материала обусловлена только свойствами и структурой образующегося материала. По нашему мнению, аномально низкие значения потери массы при П/Ц=0,1 связаны, прежде всего, с формированием в той области значений П/Ц наиболее оптимальной структуры материала, характеризующейся как образованием соматричной фазы (см. рис.2), так и непрерывной полимерной пленки на продуктах гидратации цемента и кольматирующей поры в образующемся материале, что приводит к снижению проницаемости полимерцемента. В области с П/Ц < 0,1, вероятно, конкурируют два процесса — увеличение интегральной пористости за счет воздухововлечения и снижение количества образующихся открытых пор с увеличением значений П/Ц. Причем в результате первого процесса химическая стойкость образующего материала должна снижаться, а в результате второго — повышаться. Очевидно, что количества полимера при П/Ц < 0,1 не хватает для образования непрерывной полимерной фазы и кольматации образующихся открытых пор. Однако, вероятно, полимера хватает для образования соматричной фазы (рис.2), что приводит к увеличению химической стойкости образующегося материала уже при П/Ц >0,05. Снижение химической стойкости полимерцемента при П/Ц=0,15-0,2, по нашему мнению, обусловлено изменением структуры образующегося материала, и, в частности, резким увеличением интегральной пористости за счет увеличения содержания поверхностно-активных веществ. При этом образующейся полимерной пленки, как и в случаях при П/Ц < 0,05, не хватает для формирования закрытопористой структуры, что приводит к увеличению проницаемости материала и облегчению доступа к нему агрессивной среды, хотя, вероятно, химическая стойкость самого материала (скелета) и повышается. В целом такое изменение приводит к тому, что значения химической стойкости модифицированных и контрольных образцов становятся близкими.
С целью определения оптимального содержания полимера, при котором обеспечивается максимальная химическая стойкость образующего материала, исследована зависимость потери массы испытуемых образцов от полимерцементного соотношения в различные сроки испытаний (рис.7).
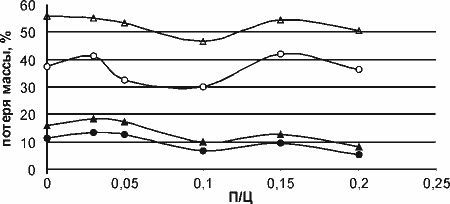
Рис.7. Зависимости потери массы испытуемых образцов от полимерцементного соотношения при продолжительности испытаний 10 сут (а) и б)) и 20 сут (а`) и б`)) под влиянием 5%-й соляной кислоты при статическом воздействии кислоты (а) и а`)) и одновременном статическом воздействии кислоты и периодическом механическом удалении продуктов коррозии с поверхности испытуемых образцов (б) и б`))
Полученные результаты показали, что оптимальное полимерцементное соотношение для исследованного латекса находится в области 0,08-0,10. Причем минимум на кривых зависимости химической стойкости полимерцементных растворов от П/Ц (рис.7) при всех условиях проведения испытаний свидетельствует о формировании в этой области оптимальной полимерцементной структуры первого рода. Некоторое снижение химической стойкости в области с П/Ц=0,10-0,15 свидетельствует о вероятном преобладании воздухововлечения и как следствие снижения проницаемости материала над повышением химической стойкости скелета полимерцемента. Дальнейшее повышение химической стойкости полимерцементных растворов при увеличении П/Ц свыше 0,15, по нашему мнению, связано с изменением структуры образующегося материала, в котором полимер создает непрерывную пространственную конденсационную структуру (рис. 4в). То есть при значениях П/Ц свыше 0,15 речь должна уже идти не о модификации цементных систем водной дисперсией, а о наполнении полимера активным минеральным наполнителем, то есть о композите, в котором основным вяжущим уже является полимер, а не цемент.
Таким образом, проведенные испытания позволили установить принципиальную возможность повышения долговечности цементных систем в агрессивных средах за счет их модификации химически стойким полимером водной дисперсии. Причем увеличение стойкости таких материалов в кислых средах не является характерным для подобных систем, так как обычно полимерцементные растворы в кислых средах обладают меньшей стойкостью, чем даже немодифицированные цементные растворы.
Григорий КОНДРАШОВ, директор филиала ФГУП "Конструкторско-технологи-ческое бюро бетонаи железобетона Госстроя РФ Инженерный центр "Югстрой" (Волгоград), к.т.н.
Распространенность природных и промышленных сред, содержащих высокие концентрации хлоридов и сульфатов, приводящих к коррозии строительных конструкций и изделий на основе портландцемента, обусловила необходимость разработки способов получения бетонов, максимально стойких в таких средах без применения вторичной защиты.
Выбор того или иного способа предотвращения коррозии бетона и железобетона в конструкциях и изделиях, гарантирующего требуемую долговечность сооружения в целом, обусловлен в первую очередь требованиями технико-экономической целесообразности и техническими возможностями строительства. Это позволяет, как правило, существенно сократить объем и стоимость ремонтно-восстановительных ра-бот, а в отдельных случаях полностью исключить их и обеспечить проектные сроки долговечности сооружений.
Возросшая за последние десятилетия потребность в бетонах, отвечающих специфическим требованиям по морозостойкости, стойкости к различным агрессивным средам, плотности привела к тому, что наиболее актуальным направлением на современном этапе развития строительного производства стала химизация этой отрасли. Использование различных органических и неорганических соединений в качестве специальных добавок к бетону приводит к существенному изменению химических процессов твердения бетона, обеспечивающих улучшение его механических и физико-химических свойств. Этими добавками являются модификаторы бетона, воздействие которых существенно изменяет структуру и свойства материала за счет введения определенных веществ при практически неизменном количестве основных составляющих.
Основываясь на современных представлениях о физико-химических поверхностных явлениях и теории контактных взаимодействий, введением химических специфических добавок (модификаторов) в цементные системы можно изменить в нужном направлении свойства цементного теста, бетонной смеси и самого бетона. Наиболее полно проблемы модифицированных бетонов с учетом отечественного и зарубежного опыта изложены в монографии В.Г. Батракова "Модифицированные бетоны. Теория и практика" (изд. 2-е, перераб. и дополн. — М.: “Стройиздат”, 1998). Основным в теоретическом и практическом плане вопросом модифицирования цементных систем представляется установление взаимосвязи между составом, строением модификаторов и их ролью в процессах гидратации и формирования структуры вяжущих различного минералогического и вещественного состава. Принципы классификации модификаторов могут быть следующими: по механизму действия на основные составляющие цемента, по химическому составу модификаторов, а также по функциональным признакам (основной технологический эффект действия в цементных системах).
Отечественная классификация модификаторов (ГОСТ 24211-91 “Добавки для бетонов. Общие технические требования”) основана на учете преимущественного технологического эффекта.
Поиски путей повышения прочности, плотности, химической стойкости и долговечности бетона привели к созданию обширной группы бетонов с добавками и на основе полимеров, которые получили общее название П-бетоны.
В соответствии с общепринятой классификацией специальные бетоны с добавками или на основе полимеров по составу и способу приготовления делятся на четыре основные категории: бетоны на основе полимерных связующих — полимербетоны (ПБ); цементные бетоны, модифицированные полимерами, — полимерцементные бетоны (ПЦБ); серные бетоны, модифицированные полимерами, — полимерсерные бетоны (ПСБ); цементные бетоны, пропитанные мономерами или олигомерами, — бетонополимеры (БП) (рис.1).
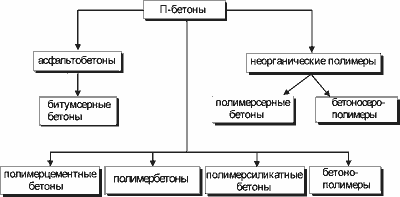
Рис.1. Классификация П-бетонов
Так как бетон и железобетон на цементной основе в настоящее время являются основными конструкционными материалами в строительстве, то наибольший интерес с точки зрения повышения их долговечности представляют полимерцементные бетоны, то есть бетоны на цементном вяжущем, модифицированные полимерами. Наиболее перспективными для промышленного применения модификаторами такого вида являются водные дисперсии полимеров, объем и ассортимент выпуска которых постоянно возрастает в химической промышленности как в России, так и за рубежом.
Исследование процессов модификации цементных систем различными химическими добавками достаточно детально изложено в вышеупомянутой монографии Батракова, а их применение — в книге "Добавки в бетон. Справочное пособие" (М.: “Стройиздат”, 1988).
Долговечность строительного материала может быть определена как способность материала или конструкции из него противостоять воздействию агрессивной среды и сохранять эксплуатационную пригодность в течение определенного заданного в проекте срока службы. При этом долговечность будет определяться свойствами бетона конструкции, химическим составом среды и условиями взаимодействия среды с конструкцией.
На свойства модифицированных водными дисперсиями полимеров растворов и бетонов и их особенности в процессе изготовления влияет множество факторов, в том числе тип полимера, полимерцементное отношение, водоцементное отношение, содержание вовлеченного воздуха и условия выдержки.
Направленная модификация бетонов и растворов на основе портландцемента за счет введения водной дисперсии происходит вследствие изменения процесса гидратации цемента и процессов образования полимерной пленки в связывающей их фазе. Причем процесс гидратации цемента обычно предшествует процессу образования полимерной пленки.

Рис.2. Упрощенная модель образования полимерцементной соматрицы: а) сразу после смешивания; б) первая фаза; в) вторая фаза; г) третья фаза (затвердевшая структура); 1) негидратированные цементные частицы; 2) полимерные частицы; 3) заполнители (промежуточное пространство заполнено водой); 4) смеси негидратированных частиц цемента и цементного геля, на которых частично осаждаются полимерные частицы; 5) смеси цементного геля и негидратированных частиц цемента, окруженных плотно упакованным слоем полимерных частиц; 6) гидраты цемента, окруженные полимерными пленками или мембранами; 7) вовлеченный воздух
Многочисленные исследования показали, что соматричная фаза, которая состоит из цементного геля и полимерной пленки, является связующим — в соответствии с упрощенной моделью, показанной на рис.2. Процесс образования полимерной пленки представлен на рис.3.
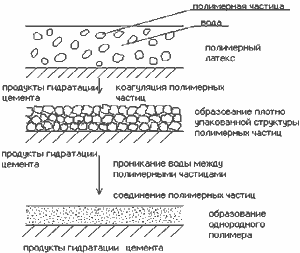
Рис.3. Упрощенная модель процесса образования полимерной пленки на продуктах гидратации цемента
Основной критерий полимерцементов — полимерцементное отношение (П/Ц), или в общем виде полимервяжущее (П/В) отношение, определяемое как отношение масс исходных полимера (в расчете на сухое вещество) и цемента (неорганического вяжущего вещества), взятых для изготовления полимерцементного материала, изделия или конструкции. Значение полимерцементного отношения характеризует состав смешанного органо-минерального вяжущего. Качество и количество заполнителя определяются дополнительными требованиями к материалу.
Изменение отношения П/Ц приводит к качественному изменению структуры полимерцемента (рис.4). Полимерная фаза в отвердевшем полимерцементе может образоваться при П/Ц больше 0,02-0,04, и, следовательно, от такого количества полимерной добавки получается полимерцемент, в отличие от цементного бетона, в том числе бетона с органическими пластифицирующими добавками.
При П/Ц менее 0,2 (при применении водных дисперсий полимеров) сросшиеся цементные новообразования создают кристаллизационно-коагуляци-онную структуру. Образовавшийся жесткий пространственный неогранический скелет укрепляется в ослабленных дефектных точках (поры, трещины) со скопившимся в них полимером, что приводит к созданию композиционного материала с повышенными прочностью и эластичностью благодаря шарнирному соединению блоков сросшихся гидратных новообразований более гибкими частицами, сетками и пленками прочных и эластичных органических полимеров, обладающих, к тому же, адгезионными свойствами.
Полимерцементы с П/Ц до 0,2-0,25 являются полимерцементами первого рода (собственно полимерцементами). В случае большого полимерцементного отношения полимер создает непрерывную пространственную конденсационную структуру, которая имеет тем большую жесткость, чем больше и чем лучше там развиты местные блоки гидратных новообразований (см. рис.4б). Это — полимерцементы второго рода. Полимерцементное отношение, при котором изменяется структура полимерцемента, определяется величиной полимерцементных частиц. Для каждой формы полимерной добавки существует своя оптимальная величина П/Ц.
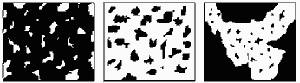
Рис.4. Схематическое строение отвердевшей системы органический полимер — неорганическое вяжущее вещество; темное поле — неорганическое вяжущее, светлое — органический полимер; а) и б) — макростроение системы: а) с преобладанием неорганического вяжущего вещества при П/Ц < 0,2; б) с преобладанием полимера при П/Ц >0,2; в) микростроение полимерной фазы с субмикроскопическими включениями аморфных гидратных новообразований
Известно, что химическая стойкость модифицированных растворов и бетонов зависит от природы полимеров, полимерцементного отношения и свойств агрессивных химических веществ. Большинство модифицированных растворов и бетонов чувствительно к действию неорганических или органических кислот и сульфатов, так как они содержат гидратированный цемент, который не обладает стойкостью к этим веществам, но стоек к щелочам и различным солям, кроме сульфатов. Модифицированные растворы и бетоны отличаются химической стойкостью по отношению к эфирам и маслам, но они не устойчивы к действию органических растворителей.
Химическая стойкость некоторых растворов, содержащих синтетические и природные каучуковые латексы, приведена в работе Y. Ohama "Durability Performance of Polymer-Modified Mortars" (Proceedings of the Second International Conference on Durability of Building Materials and Components, Gaitherburg, USA, 242-248, 1981).
Анализ приведенных результатов позволил выделить два основных требования к водным дисперсиям, удовлетворение которым позволит обеспечить высокую химическую стойкость полимерцементных растворов в агрессивных средах. Это возможность совмещения с цементными системами (в том числе агрегативная устойчивость и стойкость полимера к воздействию щелочей) и стойкость полимера дисперсии к воздействию солей, кислот, органических растворителей и масел.
С точки зрения повышения коррозионной стойкости цементных систем наибольший интерес представляет изучение влияния добавления водной дисперсии полимера на химическую стойкость образующегося материала в тех или иных химически агрессивных средах. Так как стойкость модифицированной водной дисперсией полимера цементной системы в основном будет предопределяться свойствами полимерцементной матрицы (при условии применения химически инертных к агрессивной среде заполнителей и наполнителей), то наши исследования по созданию полимерцементных бетонов и растворов повышенной коррозионной стойкости были начаты с выбора водной дисперсии, удовлетворяющей указанным выше критериям.
Таким образом, на первом этапе основным критерием отбора дисперсий для проведения исследований стала именно химическая стойкость полимера, образующего дисперсию. Сравнительный анализ данных (Г. М. Кондрашов. "Бетоны повышенной коррозионной стойкости, пропитанные водными дисперсиями", канд. дисс., 1985 г.) показал, что максимальной химической стойкостью обладают сополимеры винилхлорида: ВХВД-65 “А”, ВХВД-65 “Б”, А-15, А-25, СВХ-I, СВХ-II, ВДВХМк-65Е-ВДК. Проведенные эксперименты показали, что из всех вышеперечисленных латексов удовлетворительной агрегативной стойкостью в цементных растворах обладает только водная дисперсия ВДВХМк-65Е-ВДК (введение остальных латексов в цементные растворы приводит к их коагуляции). Поэтому в дальнейших исследованиях использовался латекс ВДВХМк-65Е-ВДК.
Эксперименты по определению влияния полимерцементного соотношения на химическую стойкость полимерцементной матрицы проводились на цементных растворах при варьировании П/Ц от 0,01 до 0,2 и водоцементном отношении 0,25. Концентрацию агрессивной среды во время испытания поддерживали с погрешностью до 1%. Для исключения влияния накапливающихся продуктов разложения агрессивная среда в процессе испытаний заменялась не реже одного раза в двое суток. В качестве наиболее агрессивной среды применяли соляную кислоту 5%-й концентрации. На рис.5-6 представлены полученные зависимости влияния агрессивной среды на изменение массы модифицированных цементных растворов под влиянием 5%-й соляной кислоты для различных значений П/Ц при статическом воздействии соляной кислоты и при сочетании статического воздействия этой кислоты и периодического механического удаления продуктов коррозии с поверхности испытуемых образцов (жирной линией показана зависимость потери массы от времени выдержки в агрессивной среде для контрольных образцов, то есть без добавки дисперсии полимера). Обработка полученных значений с помощью приемов корреляционного анализа на ЭВМ позволила установить, что зависимость потери массы образцов при всех значениях полимерцементного соотношения от времени воздействия агрессивной среды подчиняется линейной зависимости с достоверностью не менее 0,95 как при механическом удалении продуктов коррозии с поверхности образцов, так и без их удаления.
Увеличение абсолютных значений потери массы при механическом удалении продуктов коррозии с поверхности испытуемых образцов по сравнению с образцами, продукты коррозии с которых не удалялись, вполне закономерно. Однако обращает на себя внимание тот факт, что при проведении экспериментов, в которых продукты коррозии не удалялись, увеличение значений П/Ц приводит к снижению потери массы испытуемых образцов (см. рис.5), в то же время механическое удаление продуктов коррозии в процессе проведения экспериментов (см. рис.6) привело к существенному изменению зависимости потери массы образцов от значения П/Ц: при П/Ц=0,1 скорость разрушения полимерцементных образцов оказалась минимальной, при всех остальных значениях П/Ц скорость разрушения образцов мало зависит от П/Ц. По нашему мнению, полученный результат объясняется следующим обстоятельством.
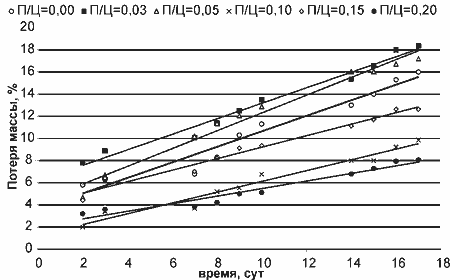
Рис.5. Зависимости потери массы модифицированных цементных растворов под влиянием 5%-й соляной кислоты для различных значений П/Ц при статическом воздействии кислоты
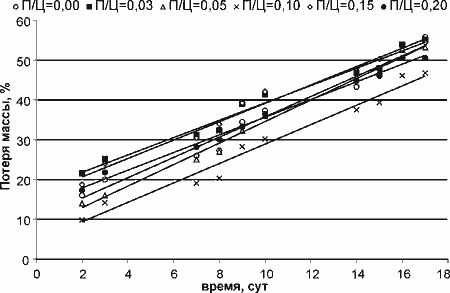
Рис.6. Зависимости потери массы модифицированных цементных растворов под влиянием 5%-й соляной кислоты для различных значений П/Ц при одновременном статическом воздействии кислоты и периодическом механическом удалении продуктов коррозии с поверхности образцов
Поскольку сам полимер стоек к воздействию соляной кислоты, то снижение массы образцов, в которых продукты коррозии не удалялись, обусловлено только растворением компонентов цементного камня. С увеличением содержания полимера в полимерцементе также увеличивается и содержание полимера в образующихся продуктах коррозии, что, в свою очередь, затрудняет массоперенос и доступ агрессивной среды к неразрушенной области полимерцемента, а также прочность сцепления продуктов коррозии с неразрушенным полимерцементом. Наблюдаемое увеличение скорости разложения полимерцементных образцов при П/Ц 0,05 по сравнению с контрольными образцами, по-видимому, связано с увеличением воздухововлечения и количества открытых пор в структуре образовавшегося материала за счет ПАВ, содержащихся в водной дисперсии полимера. Причем при этих значениях П/Ц наиболее вероятной структурой образующего материала является структура, показанная на рис.4 (а). Увеличение П/Ц свыше 0,05, по-видимому, приводит к образованию как непрерывной полимерной фазы (см. рис.3 и рис.4б), так и соматричной фазы (см. рис.2) и как следствие к изменению структуры материала и увеличению количества закрытых пор.
В случае механического удаления продуктов коррозии с поверхности испытуемых образцов затруднение доступа агрессивной среды к полимерцементным образцам и массопереноса за счет плотно сцепленного с образцом слоя продуктов коррозии не происходит. Таким образом, химическая стойкость полимерцементного материала обусловлена только свойствами и структурой образующегося материала. По нашему мнению, аномально низкие значения потери массы при П/Ц=0,1 связаны, прежде всего, с формированием в той области значений П/Ц наиболее оптимальной структуры материала, характеризующейся как образованием соматричной фазы (см. рис.2), так и непрерывной полимерной пленки на продуктах гидратации цемента и кольматирующей поры в образующемся материале, что приводит к снижению проницаемости полимерцемента. В области с П/Ц < 0,1, вероятно, конкурируют два процесса — увеличение интегральной пористости за счет воздухововлечения и снижение количества образующихся открытых пор с увеличением значений П/Ц. Причем в результате первого процесса химическая стойкость образующего материала должна снижаться, а в результате второго — повышаться. Очевидно, что количества полимера при П/Ц < 0,1 не хватает для образования непрерывной полимерной фазы и кольматации образующихся открытых пор. Однако, вероятно, полимера хватает для образования соматричной фазы (рис.2), что приводит к увеличению химической стойкости образующегося материала уже при П/Ц >0,05. Снижение химической стойкости полимерцемента при П/Ц=0,15-0,2, по нашему мнению, обусловлено изменением структуры образующегося материала, и, в частности, резким увеличением интегральной пористости за счет увеличения содержания поверхностно-активных веществ. При этом образующейся полимерной пленки, как и в случаях при П/Ц < 0,05, не хватает для формирования закрытопористой структуры, что приводит к увеличению проницаемости материала и облегчению доступа к нему агрессивной среды, хотя, вероятно, химическая стойкость самого материала (скелета) и повышается. В целом такое изменение приводит к тому, что значения химической стойкости модифицированных и контрольных образцов становятся близкими.
С целью определения оптимального содержания полимера, при котором обеспечивается максимальная химическая стойкость образующего материала, исследована зависимость потери массы испытуемых образцов от полимерцементного соотношения в различные сроки испытаний (рис.7).
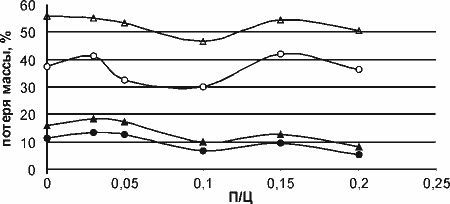
Рис.7. Зависимости потери массы испытуемых образцов от полимерцементного соотношения при продолжительности испытаний 10 сут (а) и б)) и 20 сут (а`) и б`)) под влиянием 5%-й соляной кислоты при статическом воздействии кислоты (а) и а`)) и одновременном статическом воздействии кислоты и периодическом механическом удалении продуктов коррозии с поверхности испытуемых образцов (б) и б`))
Полученные результаты показали, что оптимальное полимерцементное соотношение для исследованного латекса находится в области 0,08-0,10. Причем минимум на кривых зависимости химической стойкости полимерцементных растворов от П/Ц (рис.7) при всех условиях проведения испытаний свидетельствует о формировании в этой области оптимальной полимерцементной структуры первого рода. Некоторое снижение химической стойкости в области с П/Ц=0,10-0,15 свидетельствует о вероятном преобладании воздухововлечения и как следствие снижения проницаемости материала над повышением химической стойкости скелета полимерцемента. Дальнейшее повышение химической стойкости полимерцементных растворов при увеличении П/Ц свыше 0,15, по нашему мнению, связано с изменением структуры образующегося материала, в котором полимер создает непрерывную пространственную конденсационную структуру (рис. 4в). То есть при значениях П/Ц свыше 0,15 речь должна уже идти не о модификации цементных систем водной дисперсией, а о наполнении полимера активным минеральным наполнителем, то есть о композите, в котором основным вяжущим уже является полимер, а не цемент.
Таким образом, проведенные испытания позволили установить принципиальную возможность повышения долговечности цементных систем в агрессивных средах за счет их модификации химически стойким полимером водной дисперсии. Причем увеличение стойкости таких материалов в кислых средах не является характерным для подобных систем, так как обычно полимерцементные растворы в кислых средах обладают меньшей стойкостью, чем даже немодифицированные цементные растворы.
Григорий КОНДРАШОВ, директор филиала ФГУП "Конструкторско-технологи-ческое бюро бетонаи железобетона Госстроя РФ Инженерный центр "Югстрой" (Волгоград), к.т.н.
Строительство и недвижимость. Статья была опубликована в номере 04 за 2003 год в рубрике бетон