Между Сциллой и Харибдой
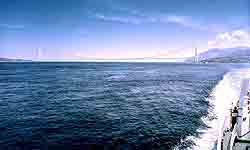
Специальные сварные детали
Так называемые специальные сварные детали представлены краевыми областями продольных коробчатых балок и сварными соединениями между продольными и поперечными балками.
Особенность краевых зон - в необычной геометрической конфигурации наклонных перемычек и в несплошностях, вызванных присоединением стальной решетки. Специфичность соединений между продольными и поперечными балками определяется особой конструкцией и различными статическими функциями конструктивных элементов, которые требуют пересечения двух перпендикулярных систем ортотропных пластин, состоящих из листов настила со значительной разницей в толщине.
Предварительное изучение позволило определить следующие четыре специальных типа соединений, что является особенно примечательным с точки зрения перспектив усталостной проверки.
Во-первых, сварное продольное соединение между наклонными перемычками и верхними листами коробчатых балок.
Во-вторых, поперечное сварное соединение между листами настила коробчатых и поперечных балок.
В-третьих, пересечение между трапецеидальными ребрами жесткости продольной ортотропной платформы и поперечной перемычкой балки.
В-четвертых, пересечение между изогнутой нижней частью коробчатых балок и поперечной перемычкой балки.
Из этих четырех типов первый является типичным для применяемого сечения продольных коробчатых балок, в то время как три остальные являются характерными для зоны пересечения с поперечной балкой.
Проверка на усталость усложняется тем фактом, что напряжения во вставках зависят как от местных, так и от общих воздействий. Напряжения в соединениях, возникающие фактически из-за изгиба поперечной балки, систематически накладываются на результаты локальных воздействий, в то время как напряжения, возникающие из-за изгиба коробчатых балок, незначительные для автодорожных коробчатых балок, являются очень существенными для железнодорожных коробчатых балок.
С целью достижения удовлетворительного поведения при усталостной нагрузке был принят ряд предварительных стратегий, начиная с концептуальных стадий, для того чтобы ограничить пики напряжений.
Вот те из них, которые стоит отметить.
При конструировании сварных продольных соединений между наклонными перемычками и верхней пластиной автодорожных и железнодорожных коробчатых балок особое внимание было уделено доступности элементов, последовательности монтажа и подготовке кромок.
Поперечное стыковое сварное соединение между листами настила коробчатых балок и поперечными балками было размещено на расстоянии 500 мм от перемычки поперечной балки посредством увеличения ширины листов настила поперечной балки в соответствии с расположением коробчатых балок. Для ограничения концентрации напряжений кромка пересечения была выполнена дугообразной (радиусом 300 мм), при этом при большой разнице в толщине листов настила была соблюдена постепенность перехода от одной толщины к другой. Краям стыкующихся кромок была придана Х-образная конфигурация.
Продольные ребра жесткости прерываются, и их сваривают с перемычками Т-образным швом для обеспечения непрерывности перемычек поперечной балки.
В ребрах жесткости перемычек рядом с сечением присоединения выполняют обширные вырезы для снижения локального изгиба сварного соединения между перемычкой поперечной балки и листом настила.
Пересечение нижней части коробчатой балки, перемычек поперечных балок сохраняет их непрерывность, при этом непрерывность нижней части коробчатых балок внутри поперечной балки достигается специальными сварными вставками.
Проверка на усталость стыка между криволинейными нижними частями коробчатых балок и поперечной балкой не представляет особых проблем, поскольку местные нагрузки оказывают на них незначительное влияние, и их можно оценить по стандартной классификации деталей.
С другой стороны, из-за наличия в настоящее время трех других специальных деталей, а также сложности напряженного состояния и взаимовлияния местных и общих воздействий, оценка усталостных напряжений, возникающих в верхнем фланце, не может быть выполнена с использованием существующих данных. Для этого нужно выполнить специальные исследования.
Данные исследования, проведенные на полномасштабных образцах, касались как стыков между железнодорожной коробчатой балкой и поперечной балкой, так и между автодорожными коробчатыми балками и поперечной балкой.
Проектирование полномасштабных образцов
При разработке образца пересечения железнодорожных коробчатых балок с поперечной балкой максимально учитывались перепускная рампа и, если были противоречия, методологические и эксплуатационные требования.
В первую очередь следует учитывать, что размеры концентраторов напряжения, вызывающих возникновение усталостных трещин, в основном не зависят от основных размеров; поэтому образцы должны быть изготовлены в натуральную величину, так как невозможно полагаться на результаты усталостных испытаний на уменьшенных образцах.
В зоне крепления верхних ортотропных панелей расположены три специальные детали, которые должны быть надлежащим образом представлены в образцах.
Для достоверного воспроизведения картины действующих напряжений, являющихся результатом сложного сочетания циклической глобальной и локальной нагрузок, имеющих разную частоту, в процессе испытания должна была быть пересмотрена возможность применения ряда независимых усталостных нагрузок. Глобальные поперечные и продольные напряжения у места сварки имеют одинаковый порядок величин, одинаковую частоту и совпадают по фазе.
После определения уровней напряжения, ожидаемых в критических деталях, пробные нагрузки и частоты определяются габаритами и статической схемой образца, который должен быть выбран для ограничения деформации самого образца и всей конструкции от усталостных нагрузок.
Все специальные детали сконцентрированы в граничных областях балок, поэтому образец должен воспроизводить только наиболее удаленные части верхней части поперечного сечения, а его ширина может быть ограничена.
Вышеописанные соображения привели к формированию образца с габаритными размерами приблизительно 8х2х3 м, чтобы обеспечить наилучшее воспроизведение реального напряженного состояния в исследуемой зоне пересечения с применением имеющегося лабораторного оборудования, испытательной аппаратуры и приводов.
Так как зона исследования ограничена сварным соединением между продольной и поперечной балками, образец состоит из съемной верхней части, воспроизводящей соединение и являющейся эффективным образцом для испытания, а также из соответственно ограниченной неподвижной части.
Местные воздействия, производимые железнодорожными осями, моделируются посредством вертикальной усталостной нагрузки, действующей на распределительные элементы, котороые воспроизводят железнодорожную суперструктуру. Глобальные поперечные воздействия возникают в соединении через поперечные усталостные силы сжатия F, приложенные к верхним листам в соответствии с сеткой поперечной балки. Глобальные продольные воздействия, по причине изгиба железнодорожной балки, воспроизводятся через схему консоли с вертикальной усталостной нагрузкой Р на свободный конец образца. Консоль, представляющая из себя простое устройство для передачи нагрузки и не являющаяся предметом данного исследования, является, очевидно, элементом неподвижной части образца.
Перед непосредственным изготовлением образца его габариты и напряженное состояние в соединении, вызванное испытательными нагрузками Р, P1 и F, были проверены посредством сложного числового анализа методом конечных элементов с применением кода Cosmos/M для данного анализа. Для целей анализа образец моделировался с применением 4 узлов трехмерных элементов оболочкового типа (элементы Shell 4 из списка обозначений Cosmos).
Испытания
Испытания, проведенные в ISMES (Институт экспериментальных моделей и конструкций, Бергамо), рассматривали четыре образца, оснащенные соответствующим образом.
Деформации в процессе испытаний измерялись электрическими тензодатчиками, а смещения - с применением индуктивных экстензометров.
По причине сложности образцов усталостным испытаниям предшествовало предварительное статическое испытание, позволившее представить напряженное состояние, полученное при анализе методом конечных элементов. Это испытание состояло в приложении трех статических нагрузок (Р=1500 кН, F=1500 кН и Pi=250 кН), каждой в отдельности и в комбинации P+F и P+F+Pi. Номинальные напряжения у краев сварного шва были выведены экстраполяцией результатов, измеренных в близлежащих точках, согласно нормативным критериям.
Усталостные испытания с постоянной амплитудой, подробно описанные ниже, проводились с одновременным приложением трех усталостных нагрузок Р, F и Pi. Так как продольные и поперечные глобальные воздействия имеют одинаковое происхождение (то есть они связаны с проходом поездов), циклические нагрузки Р и F были приложены в фазе с низкой частотой, в то время как нагрузка Pi, моделирующая локальные воздействия, была приложена с высокой частотой.
Когда был достигнут предварительно заданный процент (25%, 50%, 75%, 90%) от ожидаемого количества циклов, наиболее значимые сварные соединения каждого образца были подвергнуты неразрушающему контролю на стадиях проектирования, после сварки и во время испытаний.
Каждый образец был сконструирован в мастерской с применением одинаковых методов, в частности, процедур и положений сварки, регламентированных проектом и техническими условиями сварки. После сварки все соединения были тщательно обследованы как визуально, так и с применением магнитографических и ультразвуковых методов, а сварные стыковые соединения были также обследованы рентгеновским методом.
Итальянский институт сварки, специалисты которого осуществили неразрушающий контроль, выпустил инструкции по сварке мостовых конструкций, о которых идет речь.
В процессе испытаний все сварочные соединения были полностью обследованы визуальным, магнитографическим и ультразвуковым методами на каждой заранее регламентированной стадии. Изменения реакции конструкции в сочетании с периодическими проверками позволили идентифицировать образование любых усталостных трещин.
Как общепринято для мостов, критерий, выбранный для определения усталостного разрушения, был макроскопическим. Образец считался разрушенным, а испытание - законченным при появлении заметной трещины и определяемой потере жесткости соединения, зарегистрированных тензодатчиками в исследуемой зоне. Тем не менее первое визуальное появление растрескивания не было зарегистрировано. В целях вышеописанной оценки трещина рассматривалась как значительная, когда ее длина была равной или более 10 мм (или толщине элемента конструкции), в зависимости от того, что больше.
Результаты экспериментов
Общая схема испытания, как и организация нагружения и комплект инструментов, описанный ранее, оставались неизменными для всех образцов, в то время как уровни нагрузки для каждого испытания менялись. Вследствие полученных результатов некоторые геометрические параметры образцов были модифицированы в соответствии с конструктивными требованиями, подкрепленными испытаниями. В соответствующих разделах сообщаются наиболее приемлемые геометрические и испытательные параметры для каждого образца.
В целях реального воспроизведения действительных эксплуатационных условий локальная нагрузка Pi, моделирующая ось нагрузки поезда, была приложена к двум рельсам, каждый из которых был прикреплен к настилу через три узла суперконструкции. Это позволило исследовать не только усталостное поведение железнодорожных суперконструкций, непосредственно приваренных или прикрепленных с помощью болтов к стальной плите, но также их влияние на усталостную прочность элементов самого стального листа. Из-за отсутствия промежуточных поперечных балок между диафрагмами продольные элементы жесткости железнодорожных коробчатых балок, приваренные к диафрагме и к перегородке поперечной балки, имели пролет, приблизительно равный 240 см.
В исследуемом образце узлы суперконструкции одного рельса были приварены непосредственно к листу настила, в то время как аналогичные узлы другого рельса были прикреплены болтами.
Специальное оборудование, расположенное на ребре рельса позволило определить нагрузки, передаваемые суперконструкции и оценить влияние распределения нагрузки в рельсах, тем самым подтверждая правильность теоретических прогнозов. Действительно, когда нагрузка располагается в соответствии с промежуточным узлом суперконструкции, эффективная отдача непосредственно нагруженного листа составляет 47,5% общей нагрузки, что является довольно хорошим результатом в сравнении с теоретическим значением 50%. Испытание на усталость с постоянной амплитудой проводили посредством одновременного приложения всех трех усталостных нагрузок Р, F и Pi. Нагрузку Р варьировали от минимума 75 кН до максимума 1500 кН с частотой 0.5 Гц, нагрузку F изменяли от минимума 75 кН до максимума 1500 кН с частотой 0,5 Гц и нагрузку Pi изменяли от 12,5 до 250 кН с частотой 5 Гц.
Диапазон продольных напряжений в основном соединении под воздействием только одной нагрузки Р был равен 150 Н/мм2.
Во время испытания в исследуемой области усталостная трещина появилась в стыковом шве между верхними листами железной дороги и поперечной балкой (тип сварного соединения Sz) по истечении примерно 230 тысяч циклов усталостной нагрузки Р. Трещина увеличивалась до тех пор, пока не распространилась на всю толщину листа, и тогда испытание было остановлено по истечении 270 тысяч циклов нагрузки Р.
Впоследствии трещина была отремонтирована, а испытание продолжено с одной только локальной нагрузкой P1, чтобы также оценить поведение элемента жесткости по отношению к элементу жесткости сварного соединения. После полного количества циклов нагрузки P1, примерно равного 6х 106, усталостное разрушение соединения появилось в сварном шве на нижней поверхности элемента жесткости, в месте, где диапазон напряжений, вызванных нагрузкой P1, был равен 85 Н/мм2.
В процессе испытания усталостные трещины возникали в сварном креплении узлов суперконструкции. Такие трещины важны, но не в прямом смысле, а лишь применительно к изучению влияния суперконструкции на усталостное сопротивление. Поэтому как только эти трещины обнаруживали, их ремонтировали, и испытание продолжалось в нормальном режиме. Такого рода трещины возникают при общем воздействии. В действительности, в процессе испытания с применением только локальной нагрузки Рз, такие трещины не появлялись.
Поведение болтового крепления суперконструкции было более удовлетворительным: в процессе испытаний не было зафиксировано никаких трещин.
Образец A2 был идентичен образцу A1. Снова узлы суперконструкции одного рельса были приварены непосредственно к листу настила, в то время как аналогичные узлы другого рельса были прикреплены болтами.
Усталостное испытание с постоянной амплитудой проводили посредством одновременного приложения всех трех усталостных нагрузок Р, F и Pi. Нагрузку Р варьировали между 75 и 1000 кН с частотой 1,0 Гц, нагрузку F изменяли от 75 до 1500 кН с частотой 1,0 Гц, нагрузку же Р1 изменяли от 12,5 до 250 кН с частотой 5 Гц. Диапазон продольных напряжений в основном сварном соединении под воздействием только одной нагрузки Р был равен 110 Н/мм2.
Во время испытания в шве между верхними листами железной дороги и поперечной балки (тип сварного соединения S2) по истечении примерно 460 тысяч циклов усталостной нагрузки Р были замечены макротрещины. Трещина распространилась на всю толщину листа, и тогда испытание было остановлено по истечении 700 тысяч циклов нагрузки Р.
И снова трещины возникли в сварной суперконструкции, которую затем ремонтировали, в то время как в суперконструкции с болтовым креплением не было выявлено никаких разрушений.
Образец А3: на основе предшествующих результатов испытаний образцов A1 и A2, а также в связи со специальными требованиями по практической эксплуатации железных дорог, было решено внести некоторые изменения в ортотропные панели железнодорожных коробчатых балок с целью сокращения локальной деформируемости панели и диапазона напряжений на верхней поверхности коробчатых балок. Такого рода модификации заключались в увеличении толщины верхнего листа с 12 до 16 мм и введении промежуточной поперечной балки между диафрагмами. В данном образце, в отличие от предыдущих, все узлы суперконструкции крепили с помощью болтов.
Образец A4, как и в случае с образцом А3, также представлял собой верхний лист настила толщиной 16 мм с промежуточной поперечной балкой между диафрагмами.
Суперконструкция сварного железнодорожного полотна была усовершенствована по сравнению с конструкциями, примененными в образцах A1 и А2. Действительно, в целях улучшения усталостного поведения листы настила супеконструкции и узлы суперконструкции того же типа, что и применявшиеся ранее, были приварены к продольным стальным полосам, которые, в свою очередь, были приварены к листу настила непрерывными продольными угловыми швами. Величины усталостных нагрузок были те же, что и для образца А2, но диапазон продольного напряжения в стыковом шве при приложении отдельно нагрузки Р был равен 96 Н/мм2. Усталостное разрушение образца произошло по истечении 1750 тыс. циклов из-за трещины в прикреплении к ребру поперечной балки.
Выводы
Усталостное испытание сложного сварного соединения между железнодорожным полотном и поперечной коробчатой балкой ставило целью проверку поведения многочисленных деталей конструкции.
На элементе жесткости, приваренном к соединениям листов настила, а также элементе жесткости, приваренном к соединениям диафрагмы, никогда не возникало каких-либо трещин, несмотря на жесткие усталостные условия, которым они были подвергнуты со стороны диапазонов напряжения и количества циклов. Поэтому можно считать, что они полностью прошли испытания с положительными результатами.
Результаты показывают, что с точки зрения усталостной прочности, сварное соединение между верхней поверхностью железнодорожного полотна и поперечными коробчатыми балками может быть причислено к классу 63. Такая классификация, в соответствии с инструкциями по определению кривых S-N, делает ссылку на диапазон номинального продольного нормального напряжения, вызванного общими нагрузками в верхней части железнодорожной коробчатой балки, и не зависит от пиков локальных напряжений. Более того, такая классификация, на основании конкретной методологии испытаний, косвенно объясняет некоторые взаимодействия локальных и общих воздействий.
Как уже было подчеркнуто, результаты испытаний оказали промежуточное воздействие на разработку элементов конструкции. По существу, точная усталостная классификация этого сложного сварного соединения, наряду с рассмотрениями влияния локальных деформаций листов на эксплуатационные свойства железнодорожного полотна, обусловила увеличение толщины верхнего листа железнодорожной коробчатой балки с 12 до 16 мм и размещение нескольких промежуточных поперечных балок между диафрагмами, тем самым сократив максимальные диапазоны напряжений, вызванных как локально, так и глобально, прохождением стандартных поездов в пределах спектра усталостных железнодорожных нагрузок.
Проверки на усталость, проведенные с использованием данных, полученных в экспериментах, показали, что срок службы при усталостном нагружении соединения больше требуемого срока службы конструкции (200 лет). Проведение экспериментов также обеспечило возможность изучения влияния метода крепления железнодорожной суперконструкции на срок службы при усталости панели настила. Действительно, были изучены различные решения крепления с применением болтов и сварки. С болтовым соединением проблем не возникло, что доказало безопасность его применения. С другой стороны, сварные соединения продемонстрировали значительные различия в зависимости от типа применяемых сварных швов; на практике решение с применением непрерывных продольных угловых сварных швов доказали свое убедительное преимущество. Конечно, эти последние выводы не являются категорическими и могут лишь указать путь к последующим исследованиям, необходимым в дальнейшем для переработки и улучшения решений по сварке для непосредственного крепления железнодорожной суперконструкции к настилу.Подготовил Сергей ЗОЛОТОВ
Строительство и недвижимость. Статья была опубликована в номере 21 за 2001 год в рубрике новости