Экономия энергоресурсов в строительстве
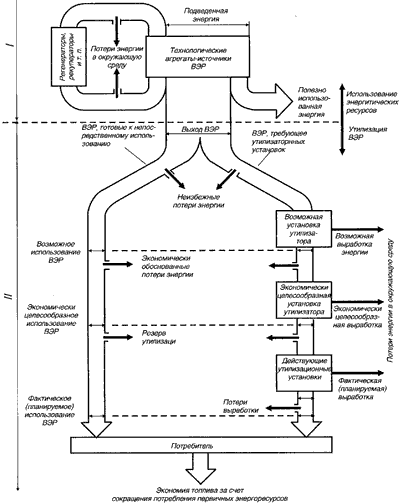
Энергосбережение на промышленных предприятиях
Эффективное решение задач по экономии электрической энергии на промышленных предприятиях обеспечивается в увязке с технологией производства. В основу этих мероприятий закладываются следующие принципы:
- оптимальный энергетический режим с максимальной производительностью технологического оборудования с минимальными удельными расходами энергии;
- изменение технологии производства с полным или частичным сокращением энергоемких переделов или процессов.
Ниже приведены мероприятия, обеспечивающие экономию электроэнергии на промпредприятиях.
8.1. Сети внешнего и внутреннего энергоснабжения:
- перевод внутренних и внешних сетей на повышенное напряжение и реконструкция сетей.
8.2. Трансформаторы:
- установление экономичных режимов работы трансформаторов с определением числа одновременно включенных, обеспечивающих минимум потерь электроэнергии в этих трансформаторах;
- размещение цеховых трансформаторов в зоне центра электрических нагрузок.
8.3. Электродвигатели:
- снижение удельных расходов электроэнергии за счет увеличения средней нагрузки рабочих машин;
- сокращение холостого хода и применение ограничителей холостого хода рабочих машин;
- замена незагруженных электродвигателей электродвигателями меньшей мощности (замена целесообразна, если средняя нагрузка электродвигателя составляет менее 45% номинальной мощности).
8.4. Промышленные электропечи:
- повышение массы садки и совершенствование подготовки шихты (подбор оптимальных составов с использованием крупного лома, среднего и мелочи);
- снижение электрических потерь (подбор оптимальной плотности тока, уменьшение сопротивления электрических контактов и др.);
- снижение тепловых потерь (увеличение стойкости футеровки, улучшение качества футеровки, снижение потерь с охлаждающей водой, уменьшение потерь тепла с отходящими газами);
- сокращение простоев печей;
- оптимизация электрических и технологических режимов работы печей;
- увеличение мощности печей;
- автоматизация управления режимом печей.
8.5. Экономия электроэнергии в системах пневмотранспорта. Сокращение расходов электроэнергии при выработке сжатого воздуха* можно осуществить по следующим направлениям:
- регулирование производительности компрессоров при существенных колебаниях расхода сжатого воздуха;
- отключение лишних компрессоров при снижении расходов сжатого воздуха;
- снижение номинального рабочего давления компрессорной установки с учетом требований различных потребителей (применение редукторов, инжекторов и регуляторов давления);
- внедрение в поршневых компрессорах прямоточных клапанов вместо кольцевых (снижение удельного расхода электроэнергии в среднем на 13-15%);
- резонансный наддув поршневых компрессоров (сокращение удельного расхода электроэнергии на 3-5%);
- осуществление подогрева сжатого воздуха перед пневмопре-емниками (теплоизоляция воздуховодов);
- контроль за утечками сжатого воздуха;
- замена сжатого воздуха другими энергоносителями;
- замена пневмоинструмента электроинструментом (в среднем экономия электроэнергии составляет 7-10%);
- замена сжатого воздуха вентиляторным дутьем.
* В среднем на выработку 1000 м3 сжатого воздуха требуется около 100-120 кВтч (а при старых компрессорах до 160 кВтч)
8.6. Насосные установки:
- повышение КПД насосов до паспортных данных;
- улучшение загрузки насосов и совершенствование регулирования их работы;
- уменьшение сопротивления трубопроводов;
- сокращение расхода и потерь воды (установка расходомеров);
- внедрение оборотного водоснабжения (экономия электроэнергии 15 - 20%);
- совершенствование систем охлаждения (уменьшение объемов потребляемой воды в 2-3 раза с соответствующим снижением расходов электроэнергии).
8.7. Вентиляция:
- замена старых вентиляторов новыми, более экономичными;
- внедрение рациональных способов регулирования производительности вентиляторов (применение многоскоростных электродвигателей - экономия энергии составляет 20-25%);
- блокировка вентиляторов тепловых завес с устройствами откры-вания и закрывания ворот;
- отключение вентиляционных установок во время технологических и организационных перерывов (экономия электроэнергии до 20%);
- внедрение автоматического управления вентиляционными установками.
8.8. Электросварочные установки:
- перевод сварки с постоянного на переменный ток (снижение удельных расходов электроэнергии на 1 кг наплавленного металла для ручной сварки на 2,9 кВтч/кг, для автоматической и полуавтоматической сварки под слоем флюса - 2,0 кВтч/кг);
- замена ручной дуговой сварки механизированными и автоматизированными способами сварки (снижение удельных расходов электроэнергии на 1 кг наплавленного металла при переменном токе на 0,17 кВтч/кг и при постоянном токе на 0,65 кВтч/кг);
- переход на точечную контактную сварку (снижение расхода электроэнергии в 2-2,5 раза);
- замена ручной дуговой сварки на контактную шовную сварку (снижение расхода электроэнергии на 15%);
- ограничение холостого хода сварочных трансформаторов или преобразователей (экономия электроэнергии до 15% в зависимости от режима ее работы);
- применение электродов с покрытием, в которое введен железный порошок (снижение удельного расхода электроэнергии на 8%);
-замена электродной сплошной проволоки на порошковую (снижение удельного расхода электроэнергии на 8-12%);
- применение полуавтоматической и автоматической сварки в среде углекислого газа (повышение производительности труда):
- применение автоматической дуговой сварки под слоем флюса с применением присадки в виде металла в порошке (снижение удельных расходов электроэнергии на 30-40%);
- применение электрошлаковой сварки на переменном токе (при соединении деталей толщиной более 30-40 мм).
8.9. Освещение
К основным мероприятиям по экономии электроэнергии при освещении промышленных предприятий и объектов жилищно-гражданского назначения можно отнести:
- уменьшение продолжительности работы источников света;
- применение энергоэффективных источников с меньшей установленной мощностью, но большей светоотдачей (приложение 7);
- внедрение систем управления и экономичных систем запуска источников света;
- уменьшение затрат на обслуживание осветительных установок при повышении качества этого обслуживания;
- использование энергоэкономичных источников, систем с направленным световым потоком;
- изменение времени начала рабочего дня с привязкой к световому климату региона;
- перераспределение поступившего в здание светового потока без потери уровня инсоляции;
- правильное размещение зданий относительно природного и архитектурного ландшафтов;
- правильное расположение зеленых насаждений относительно здания;
- точное определение рабочих и подсобных помещений в самом здании, а также рабочих зон в помещениях;
- применение "пакетного" способа освещения вместо отдельных линий, расположенных вдоль цеха (экономия электроэнергии до 30% от общей присоединенной мощности);
- не допускать завышения установленной мощности осветительных установок;
- поддержание номинальных уровней напряжения в осветительной сети.
Энергосбережение при производстве машиностроительной продукции
Основные направления экономии электроэнергии на предприятиях машиностроения приведены ниже.
1. Рациональная организация технологических процессов.
2. Использование современных технологических режимов и методов работы оборудования, в том числе:
- внедрение скоростного фрезирования, сверления и шлифования (снижение удельных расходов электроэнергии на 25 - 30%);
- высадка и электровысадка деталей вместо их обработки на металлорежущих станках (экономия электроэнергии до 50%);
- сушка обмоток электрических машин током вместо сушки в сушильных камерах печей (сокращение расходов электроэнергии до 6 раз);
- замена подшипников скольжения на шариковые (сокращение расхода электроэнергии до 12%);
- обеспечение своевременной смазки технологического оборудования (экономия электроэнергии до 10%);
- исключение работы на станках тупым инструментом (сокращение расхода электроэнергии на обработку изделий до 30%).
3. Использование оборудования с улучшенными характеристиками.
4. Прямое использование электроэнергии в технологии.
5. Сокращение объема металла, снимаемого при обработке (удельный расход электроэнергии может быть снижен на 15-20%).
6. Замена асинхронных двигателей синхронными.
Утилизация вторичных энергоресурсов
Под ВЭР понимается энергетический потенциал продукции, отходов, побочных и промежуточных продуктов, образующихся в технологических агрегатах (установках), которые не используются в самом агрегате, но могут быть частично или полностью использованы для энергоснабжения других агрегатов или технологических процессов.
Основными источниками образования ВЭР в различных отраслях промышленности выступают технологические агрегаты, как правило, недостаточно совершенные с энергетической точки зрения. Это приводит к большим потерям энергии первичного топлива в отдельных случаях до 50-60%,
Увеличение удельных затрат на добычу и транспорт органического топлива обусловливает экономическую эффективность утилизации низкопотенциальных ВЭР.
Рациональное использование ВЭР является одним из крупнейших резервов экономии топлива, способствующим снижению топливо-и энергоемкости промышленной продукции. ВЭР могут использоваться без изменения энергоносителя или с изменением его через выработку теплоты, электроэнергии или механической работы в различных утилизаторах.
Утилизация тепла дымовых газов, образующихся при сжигании в тепловых агрегатах с применением жидкого и твердого топлива, представляет собой сложную техническую проблему, так как они имеют невысокий энергетический потенциал (температура их находится в пределах 80-300 °С), они сильно запылены и загрязнены. В них содержатся различные химические примеси, которые вызывают коррозию газоходов и оборудования. В отечественной и зарубежной практике имеется достаточный опыт использования низкопотенциальных ВЭР: теплоты отходящих газов с температурой до 300 °С, сточных вод и вентиляционных выбросов.
По виду энергии ВЭР могут быть разделены на три группы:
1. Топливные ВЭР. Это химическая энергия отходов технологических процессов, не используемых для дальнейшей технологической переработки (непосредственное использование горючих материалов в качестве топлива).
2. Тепловые ВЭР. Это физическая теплота отходов производства, теплота отходящих газов, теплота отработанных горячей воды и пара и др. (использование теплоты, получаемой в утилизационных установках).
3. ВЭР избыточного давления. Это потенциальная энергия газов и жидкостей, избыточное давление которых необходимо снижать перед последующим их использованием (использование механической или электрической энергии, вырабатываемой в утилизационных установках или станциях за счет ВЭР).
Для эффективного использования ВЭР на каждом предприятии должен быть проведен комплекс работ, включающий в себя составление энергетического баланса, в котором выделяется потенциал энергосбережения за счет использования ВЭР, и возможные пути его реализации.
Принципиальная схема использования ВЭР приведена на рисунке.Леонид СОКОЛОВСКИЙ,начальник главного управления строительной науки и нормативов Минстройархитектуры Республики Беларусь
Строительство и недвижимость. Статья была опубликована в номере 21 за 2001 год в рубрике энергетика