Энергосбережение при производстве строительных материалов
Продолжение. Начало в №№ 9, 10, 12-14
Производство извести
Начиная с 70-х годов, производство извести в Республике Беларусь осуществляется мокрым способом. Эта технология, сменившая систему Леполь, в то время имела ряд преимуществ, а часть их сохраняется и сегодня (удобство в гомогенизации шлама и возможность создания необходимого его запаса перед печью, обеспечение стабильного качества и ритмичной работы печи). Мокрая технология производства извести имеет один серьезный недостаток - высокий удельный расход топлива на единицу продукции. Это вызвано испарением во вращающейся печи большого количества влаги, содержащейся в сырье природной и дополнительной, добавляемой при подготовке шлама.
При среднегодовой карьерной влажности мела 25% количество естественной влаги, которую необходимо испарить при любой технологии, составляет 0,54 кг на килограмм извести. При приготовлении шлама его влажность достигает 40-44%, то есть необходимо испарить уже 1,28 кг воды на 1 кг извести.
Все это приводит к тому, что удельный расход условного топлива при мокром способе при использовании печи 3,6х110 м доходит до 360-310 кг/т извести второго сорта.
Учитывая то, что производство всей извести в республике осуществляется по мокрому способу, а эта технология получения цемента и извести на определенных стадиях одинакова, практически все энергосберегающие мероприятия, связанные с производством цемента, могут быть осуществлены и при производстве извести.
Анализ возможных схем перевода производства извести на новые энергосберегающие технологии позволяет рекомендовать использование в качестве сырья природного мела влажностью 23-28% без добавления влаги при приготовлении шлама, перевод вращающихся печей на сухую технологию, позволяющую уменьшить удельный расход топлива с 270-310 до 210-220 килограммов на одну тонну извести, или в среднем на 25% (рис. 1). При этом должна быть произведена модернизация технологической линии, которая заключается в следующем: вращающаяся печь оборудуется теплообменным устройством в виде свободно висящих на расстоянии 25 м от холодного конца печи цепей с размером звена 120 мм, диаметром прутка 25 мм, общая масса цепей - 40 тонн, в том числе 15 тонн из жаростойкой стали; за печью в качестве теплообменника-утилизатора тепла устанавливается шахтная дробилка-сушилка ММТ 1300х2300х750. (Дробилка питается мелом автономно и работает на отходящих газах вращающейся печи); система обеспыливания печи оборудуется дополнительной ступенью циклонов 2,8х14 метров; для преодоления дополнительного гидравлического сопротивления используются резервы дымососа, или увеличиваются его обороты, или дымосос заменяется более мощным.
Схема может быть укороченной, то есть без установки дробилки-сушилки в качестве запечного теплообменника-утилизатора. В этом случае снижаются капитальные затраты, но сокращается экономия топлива в связи с возрастанием температуры уходящих газов. Расход топлива в этом случае уменьшится с 270-310 до 220-230 кг условного топлива на тонну извести, или в среднем на 20%. В настоящее время научные организации Минстройархитектуры работают над созданием новой технологии сухого производство извести (рис. 2).
Рис. 2. Основные стадии технологии: 1 — первичное дробление сырья рыхлительными машинами; 2 — дробление сырья на вальцах грубого помола и выделение камней; 3 — дозировка сырья из бункера запаса валковым дозатором; 4 — совместная сушка и помол сырья в дробилке-сушилке; 5 — осаждение тонкомолотой сырьевой муки в циклоне-осадителе; 6 — двухстадийный нагрев сырьевой муки в циклонных теплообменниках; 7 — диссоциация СаСО3 на СаО и СО2 в реакторе-декарбонизаторе KSV; 8 — трехстадийное охлаждение извести в циклонных теплообменниках; 9 — подача извести на склад готовой продукции; 10 — обеспыливание отходящих газов в циклонах и электрофильтрах.
Технология, предложенная УП "Силикат" и Минским НИИСМ, основана на скоростных процессах тепломассообмена в тонкодисперсных средах на всех стадиях технологического процесса: совместной сушки и помола сырья, нагрева, диссоциации карбонатов и охлаждения готового продукта.
Готовый продукт - высокоактивная, тонкодисперсная, высококачественная молотая известь, пригодная без дополнительной обработки как для автоклавных материалов, так и для строительных целей.
Согласно расчетам, расход условного топлива составит от 177,7 до 188,9 кг на тонну извести, электроэнергии около 40 кВт/ч на одну тонну. Это на 40% меньше в сравнении с традиционной технологией.
Гипс, его производство и применение
На изготовление одной тонны гипса требуется почти в 4 раза меньше топливно-энергетических ресурсов, чем на производство одной тонны цемента. При прочих равных условиях строительные материалы и конструкции, изготовленные с применением гипсового вяжущего, выгодно отличаются от материалов, изготовленных с применением вяжущих других видов. Естественно, необходимо расширение номенклатуры изделий из гипса для применения в строительстве (перегородочные панели и блоки, декоративные, звукопоглощающие и мраморовидные плиты, сухие смеси, гипсокартонные листы различных модификаций и др.).
Преимущества гипса наиболее очевидны при его применении для устройства внутренних стен и перегородок. Сравнительные технико-экономические показатели внутренних стен и перегородок из гипса и других материалов даны на 1 м конструкции в табл. 1.
Таблица 1
Применение штукатурных смесей на основе гипса взамен цементно-известковых позволяет сократить расход топлива на изготовление исходных материалов на 170 кг и цемента до 600 кг на каждые 100 м2 оштукатуренной поверхности. Сухие гипсовые смеси могут быть использованы для устройства наливных самонивелирующихся оснований под полы взамен цементных стяжек. Экономия в этом случае составит до 2 тонн цемента на 100 м2 основания и до 240 кг условного топлива.
К энергосберегающим мероприятиям также следует относить широкое применение гипсокартонных листов повышенной огнестойкости (0,6 часа) и влагостойких листов. Первые могут широко применяться при строительстве зданий с деревянным каркасом и мансардном строительстве. Вторые - для устройства перегородок в помещениях с высокой относительной влажностью воздуха взамен энергоемких кирпичных, обеспечивая тем самым снижение массы зданий. Одной из возможностей более широкого применения гипсового вяжущего взамен цементного, известкового и других является использование фосфогипса, отхода химического производства (в республике в отвалах химического завода запасы фосфогипса составляют более 20 млн тонн). Целесообразность его использования диктуется не только экономическими, но и экологическими соображениями.
Применение фосфогипса ограничивалось тем, что он не может быть использован без предварительной обработки. В настоящее время имеются отечественные технологические решения по нейтрализации фосфорной кислоты и соединений фтора, содержащихся в фосфогипсе. Разработанная технология позволяет получить гипсовое вяжущее марок Г7-Г13 с нормальными сроками схватывания.
Производство стекла и изделий из него
В зависимости от ассортимента выпускаемой продукции, а также климатических условий на варку стекла расходуется до 60-80% энергии, потребляемой предприятием. Поэтому снижению энергоемкости процессов варки стекла следует уделять особое внимание. Тепловой КПД лучших отечественных пламенных стекловаренных печей составляет 25-28% против 50% лучших зарубежных. Энергия топлива, расходуемая на обогрев стекловаренной печи, распределяется по трем основным статьям:
- собственно варка стекла (20-25%),
- потери тепла через поверхность печи (53-60%),
- потери тепла с отходящими газами (20-22%).
Повышение эффективности использования тепла заключается в увеличении доли первой статьи за счет существенного уменьшения удельного веса двух остальных.
Анализ информационных материалов, отечественного и зарубежного опыта позволяет сделать вывод о наличии весьма разнообразных технических средств и решений, реализация которых будет способствовать энергосбережению в стекольной отрасли.
1. Размер частиц в шихте имеет большое значение для стекловарения. Желательно иметь размер частиц всех видов сырья примерно одинаковых размеров (0,1-0,4 мм).
При подготовке шихты необходимо предусматривать удаление частиц более 0,4 и менее 0,1 мм, что значительно ускорит процесс стекловарения. Например, время, затрачиваемое на растворение частиц песка размером 0,4 мм, примерно в 4 раза меньше, чем для растворения частиц песка размером 0,8 мм.
Удаление частиц размером меньше 0,1 мм позволит улучшить химический состав стекломассы по содержанию красящих окислов железа и хрома, а также тугоплавких окислов и ускорить ее осветление.
2. Тепловая мощность отечественных ванных печей для выпуска листового стекла составляет 115-140 кВт/м 2, что обеспечивает выход стекломассы до 1500 кг в сутки с 1 м 2 отапливаемой части ванной печи. Для увеличения объема стекломассы до 2000-2500 кг/м 2 в сутки необходимо тепловую мощность печей поднять до 200-240 кВт/м 2. Это может быть достигнуто за счет увеличения расхода газа и других мероприятий для повышения температуры как газового пространства печи, так и стекломассы. При этом удельный расход топлива снизится на 3-5%.
3. Тепловой КПД стекловаренных пламенных печей отечественной промышленности не превышает 25-28%. Этот показатель можно повысить до 50% и более путем применения их эффективной теплоизоляции, утилизации тепла отходящих газов.
3.1. На ряде стекольных заводов успешно применяется для изоляции сводов и стен печей вспученный вермикулит или другие материалы с содержанием AI 2О 3 до 40%. Достаточно высокая температура применения вермикулита (до 1100°С) и низкая насыпная плотность (120 кг/м 3) позволяют отнести его к эффективным теплоизоляционным материалам для стекловаренных печей. Толщина слоя вермикулита обычно принимается 80-120 мм. Укладка производится по герметичной огнеупорной обмазке толщиной 15-20 мм. Теплоизоляция свода и стен вспученным вермикулитом проста в устройстве и обеспечивает экономичную эксплуатацию стекловаренных печей.
Температура наружной поверхности свода снижается с 250°С до 90°С. Удельный расход топлива сокращается в среднем на 10%.
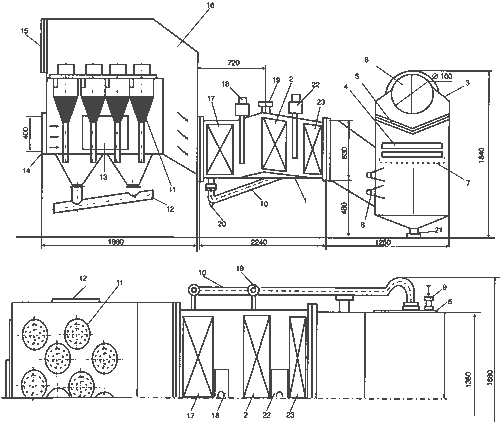
Рис. 3: 1 — экономайзер; 2, 17, 23 — трубные пучки; 3 — барботажный аппарат; 4 — коллектор; 5 — жалюзийный сепаратор; 6 — выход очищенного газа; 7 — распределительная решетка; 8 — коллектор с форсунками; 9 — подвод холодной воды; 10 — соединительный трубопровод; 11 — циклон; 12 — отвод уловленной пыли; 13, 15 — люк; 14 — подвод газа; 16 — циклонный аппарат; 18, 22 — обдувочное устройство; 19 — выход горячей воды; 20 — дренаж; 21 — слив конденсата.
3.2. Рекомендуется применение разработанного институтом "Белгипростром" комплекса по утилизации тепла и очистке отходящих газов стекловаренных печей (рис. 3). За счет их тепла осуществляется нагрев воды для горячего водоснабжения производства. Комплекс также обеспечивает эффективную многоступенчатую очистку отходящих газов от пыли, содержащей соединения свинца, цинка, калия, мышьяка, бора, бериллия, стронция и других вредных веществ. Объем отходящих газов - 9,2 тыс. м 3/час. Температура на входе 400-500°С, на выходе - 60°С. Степень очистки газов - 99,3%.
4. Повышение температуры факела способствует сжиганию топлива с минимальным коэффициентом избытка воздуха. Практически осуществить это довольно трудно, так как при этом возможно неполное сгорание топлива с вытекающими отсюда отрицательными последствиями. Следует отрегулировать процесс горения таким образом, чтобы коэффициент избытка воздуха не превышал 1,05-1,1. Для этого необходимо исключить или хотя бы сократить до минимума подсос холодного воздуха в регенераторы и печь. Повышению температуры факела способствует также увеличение температуры подогрева воздуха, идущего на горение, что связано с повышением эффективности работы регенераторов за счет использования эффективных насадок.
Повышению эффективности использования энергии факела способствует увеличение степени его черноты. Как известно, излучательная способность факела природного газа значительно ниже излучательной способности факела мазута (соответственно 0,2-0,25 и 0,5-0,60). Видимо, этим и объясняется понижение производительности стекловаренных печей при переводе их с жидкого топлива на газ. Возможным, но нежелательным путем является использование комбинированного газомазутного отопления стекловаренной печи.
5. Большое значение в интенсификации процесса теплопередачи от факела к шихте и стекломассе имеет повышение степени покрытия факелом зеркала стекломассы, приближение факела к нему, улучшение смешения топлива с воздухом. Поэтому следует применять нижний подвод топлива, плоскофакельный и веерообразный способы сжигания топлива, горелки с предварительным смешением топлива и воздуха, регулирование длины факела с использованием сжатого воздуха.
6. Использование галоидных соединений позволяет снизить температуру появления жидкой фазы на 150-200°С и соответственно получить существенный (до 15-20%) прирост производительности стекловаренных печей. (Однако применение химических ускорителей плавления увеличивает токсичность выбросов из печи.)
7. Рекомендуется применение при производстве плоского стекла эффективного флоат-способа, который характеризуется меньшим удельным расходом энергии. При современном производстве листового стекла флоат-методом стекловаренные ванные печи должны иметь производительность до 800 т/сутки. При этом методе лента стекла формируется на расплаве олова в флоат-ванне, которая состоит из бассейна с расплавленным оловом и свода (рис. 4). Пространство между бассейном и сводом по всей длине флоат-ванны заполнено смесью азота и водорода, выполняющей функцию защитной атмосферы и предохраняющей олово от окисления.
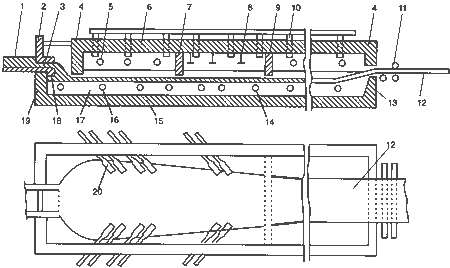
Рис. 4: 1 — стекломасса; 2 — шибер; 3 — сливной лоток; 4, 13, 19 — стены ванны; 5, 16 — регуляторы температуры; 6 — свод; 7, 9 — перегородки; 8, 14 — нагреватели; 10 — трубопровод; 11 — тянульное устройство; 12 — лента стекла; 15 — бассейн; 17 — расплавленное олово; 18 — стекло; 20 — растягивающий ролик.
8. Полезно применение гранулированной шихты, в которую вводится щелочь в виде едкого натра, что позволяет повысить прочность гранул до 17 кг/см 2. В результате уменьшаются потери шихты при транспортировке. Кроме того, частичная замена соды едким натром позволит повысить производительность печи, снизить температуру варки на 25-30°С при улучшении качества стекломассы и сократить расход топлива на 5%.
9. Экономит топливо и замена кальцинированной соды каустической, которую вводят в шихту в виде 50%-ного водного раствора. Шихта имеет 5-7% влаги. Специальная установка с автоматической системой позволяет вводить каустик за 30 секунд в любом периоде цикла смешивания. При этом расход топлива при хорошем качестве стекла уменьшается на 5%.
10. Дает экономию применение газотурбинных установок, в которых используется тепло отходящих газов стекловаренных печей для получения пара высокого давления. Вырабатываемая электроэнергия используется на производстве. В зависимости от типа стекловаренных печей затраты на электроэнергию при такой утилизации тепла могут быть снижены на 25%.
11. В целях экономии топлива может осуществляться интенсификация теплообмена в рабочем пространстве печи. Для этого используется система сжигания мазута с вводом форсунок под горелками, что позволяет снизить расход топлива на 10%. Эта система может быть применена в печах с площадью от 53 до 66 м 2. Кроме этого, печи оборудуются дополнительным электроподогревом мощностью 375, 700 или 850 кВт. Повышение энергетической эффективности варки обусловлено конструкцией форсунок, которые обеспечивают необходимый угол раскрытия пламени и оптимальную степень распыления. Это позволяет снизить расход воздуха на распыление на 25-50% (при расходе условного топлива 1520 кг/час расход воздуха снижается до 4,2-5,6 м 3/мин).
12. К новым тенденциям развития стекловарения относится переход на электроварку. Этот метод много лет успешно применяется в европейских странах. Средний удельный расход электроэнергии в электроварочной ванне производительностью 12 т/сут. и установленной мощностью 650 кВт при нормальных производственных условиях составляет 1 кВт/ч на кг стекла.
Преимущества этих электропечей сводятся к следующему:
- при одинаковой производительности варки электропечи могут быть значительно меньшими по размерам, чем печи, работающие на топливе;
- доля капитальных вложений в затратах на варку стекла, производимого в электропечах, ниже, чем производимого в обычных ванных печах;
- электроварочные печи легче поддаются автоматизации технологического процесса;
- улучшаются экономические показатели.
13. В отдельных случаях во избежание роста тепловых потерь из-за увеличенного соотношения общей поверхности стенок электроплавильной ванны и ее емкости применяется трехсекционная ванна (при этом печь сохраняется как единое целое). Расход энергии в этой печи составляет 0,95 кВт/ч на 1 кг расплавленного стекла.
14. Снижение расхода топлива и электроэнергии обеспечивается за счет широкого использования в качестве сырья боя стеклотары. Это дает возможность снизить температуру варки, а также сократить количество вредных выбросов.
Леонид СОКОЛОВСКИЙ,
начальник главного управления строительной науки и нормативов Министерства архитектуры и строительства РБ
Производство извести
Начиная с 70-х годов, производство извести в Республике Беларусь осуществляется мокрым способом. Эта технология, сменившая систему Леполь, в то время имела ряд преимуществ, а часть их сохраняется и сегодня (удобство в гомогенизации шлама и возможность создания необходимого его запаса перед печью, обеспечение стабильного качества и ритмичной работы печи). Мокрая технология производства извести имеет один серьезный недостаток - высокий удельный расход топлива на единицу продукции. Это вызвано испарением во вращающейся печи большого количества влаги, содержащейся в сырье природной и дополнительной, добавляемой при подготовке шлама.
При среднегодовой карьерной влажности мела 25% количество естественной влаги, которую необходимо испарить при любой технологии, составляет 0,54 кг на килограмм извести. При приготовлении шлама его влажность достигает 40-44%, то есть необходимо испарить уже 1,28 кг воды на 1 кг извести.
Все это приводит к тому, что удельный расход условного топлива при мокром способе при использовании печи 3,6х110 м доходит до 360-310 кг/т извести второго сорта.
Учитывая то, что производство всей извести в республике осуществляется по мокрому способу, а эта технология получения цемента и извести на определенных стадиях одинакова, практически все энергосберегающие мероприятия, связанные с производством цемента, могут быть осуществлены и при производстве извести.
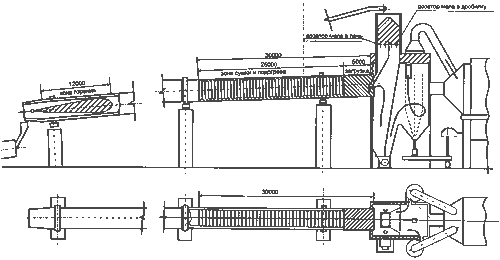
Схема может быть укороченной, то есть без установки дробилки-сушилки в качестве запечного теплообменника-утилизатора. В этом случае снижаются капитальные затраты, но сокращается экономия топлива в связи с возрастанием температуры уходящих газов. Расход топлива в этом случае уменьшится с 270-310 до 220-230 кг условного топлива на тонну извести, или в среднем на 20%. В настоящее время научные организации Минстройархитектуры работают над созданием новой технологии сухого производство извести (рис. 2).
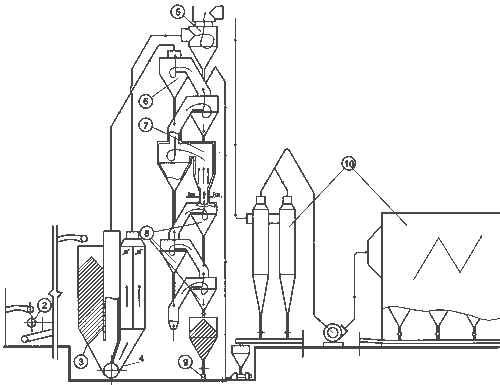
Технология, предложенная УП "Силикат" и Минским НИИСМ, основана на скоростных процессах тепломассообмена в тонкодисперсных средах на всех стадиях технологического процесса: совместной сушки и помола сырья, нагрева, диссоциации карбонатов и охлаждения готового продукта.
Готовый продукт - высокоактивная, тонкодисперсная, высококачественная молотая известь, пригодная без дополнительной обработки как для автоклавных материалов, так и для строительных целей.
Согласно расчетам, расход условного топлива составит от 177,7 до 188,9 кг на тонну извести, электроэнергии около 40 кВт/ч на одну тонну. Это на 40% меньше в сравнении с традиционной технологией.
Гипс, его производство и применение
На изготовление одной тонны гипса требуется почти в 4 раза меньше топливно-энергетических ресурсов, чем на производство одной тонны цемента. При прочих равных условиях строительные материалы и конструкции, изготовленные с применением гипсового вяжущего, выгодно отличаются от материалов, изготовленных с применением вяжущих других видов. Естественно, необходимо расширение номенклатуры изделий из гипса для применения в строительстве (перегородочные панели и блоки, декоративные, звукопоглощающие и мраморовидные плиты, сухие смеси, гипсокартонные листы различных модификаций и др.).
Преимущества гипса наиболее очевидны при его применении для устройства внутренних стен и перегородок. Сравнительные технико-экономические показатели внутренних стен и перегородок из гипса и других материалов даны на 1 м конструкции в табл. 1.
Таблица 1
Конструкции перегородок и внутренних стен | Полная трудоемкость, чел./час. | Полная энергоемкость, кг усл. топлива |
Панели гипсобетонные толщиной 80 мм из гипсовых плит размером 600х300х80 мм | 0,7 | 8 |
Межкомнатные из гипсокартонных листов со звукоизоляционным слоем из минераловатных плит: - на металлическом каркасе построечной сборки, - на деревянном каркасе заводского изготовления | 1,55 0,87 | 3-3,5 1,55 |
Кирпичные оштукатуренные толщиной в 0,5 кирпича (120 мм) | 4,3 | 15 |
Панели из тяжелого бетона толщиной 80 мм | 2,8 | 19 |
К энергосберегающим мероприятиям также следует относить широкое применение гипсокартонных листов повышенной огнестойкости (0,6 часа) и влагостойких листов. Первые могут широко применяться при строительстве зданий с деревянным каркасом и мансардном строительстве. Вторые - для устройства перегородок в помещениях с высокой относительной влажностью воздуха взамен энергоемких кирпичных, обеспечивая тем самым снижение массы зданий. Одной из возможностей более широкого применения гипсового вяжущего взамен цементного, известкового и других является использование фосфогипса, отхода химического производства (в республике в отвалах химического завода запасы фосфогипса составляют более 20 млн тонн). Целесообразность его использования диктуется не только экономическими, но и экологическими соображениями.
Применение фосфогипса ограничивалось тем, что он не может быть использован без предварительной обработки. В настоящее время имеются отечественные технологические решения по нейтрализации фосфорной кислоты и соединений фтора, содержащихся в фосфогипсе. Разработанная технология позволяет получить гипсовое вяжущее марок Г7-Г13 с нормальными сроками схватывания.
Производство стекла и изделий из него
В зависимости от ассортимента выпускаемой продукции, а также климатических условий на варку стекла расходуется до 60-80% энергии, потребляемой предприятием. Поэтому снижению энергоемкости процессов варки стекла следует уделять особое внимание. Тепловой КПД лучших отечественных пламенных стекловаренных печей составляет 25-28% против 50% лучших зарубежных. Энергия топлива, расходуемая на обогрев стекловаренной печи, распределяется по трем основным статьям:
- собственно варка стекла (20-25%),
- потери тепла через поверхность печи (53-60%),
- потери тепла с отходящими газами (20-22%).
Повышение эффективности использования тепла заключается в увеличении доли первой статьи за счет существенного уменьшения удельного веса двух остальных.
Анализ информационных материалов, отечественного и зарубежного опыта позволяет сделать вывод о наличии весьма разнообразных технических средств и решений, реализация которых будет способствовать энергосбережению в стекольной отрасли.
1. Размер частиц в шихте имеет большое значение для стекловарения. Желательно иметь размер частиц всех видов сырья примерно одинаковых размеров (0,1-0,4 мм).
При подготовке шихты необходимо предусматривать удаление частиц более 0,4 и менее 0,1 мм, что значительно ускорит процесс стекловарения. Например, время, затрачиваемое на растворение частиц песка размером 0,4 мм, примерно в 4 раза меньше, чем для растворения частиц песка размером 0,8 мм.
Удаление частиц размером меньше 0,1 мм позволит улучшить химический состав стекломассы по содержанию красящих окислов железа и хрома, а также тугоплавких окислов и ускорить ее осветление.
2. Тепловая мощность отечественных ванных печей для выпуска листового стекла составляет 115-140 кВт/м 2, что обеспечивает выход стекломассы до 1500 кг в сутки с 1 м 2 отапливаемой части ванной печи. Для увеличения объема стекломассы до 2000-2500 кг/м 2 в сутки необходимо тепловую мощность печей поднять до 200-240 кВт/м 2. Это может быть достигнуто за счет увеличения расхода газа и других мероприятий для повышения температуры как газового пространства печи, так и стекломассы. При этом удельный расход топлива снизится на 3-5%.
3. Тепловой КПД стекловаренных пламенных печей отечественной промышленности не превышает 25-28%. Этот показатель можно повысить до 50% и более путем применения их эффективной теплоизоляции, утилизации тепла отходящих газов.
3.1. На ряде стекольных заводов успешно применяется для изоляции сводов и стен печей вспученный вермикулит или другие материалы с содержанием AI 2О 3 до 40%. Достаточно высокая температура применения вермикулита (до 1100°С) и низкая насыпная плотность (120 кг/м 3) позволяют отнести его к эффективным теплоизоляционным материалам для стекловаренных печей. Толщина слоя вермикулита обычно принимается 80-120 мм. Укладка производится по герметичной огнеупорной обмазке толщиной 15-20 мм. Теплоизоляция свода и стен вспученным вермикулитом проста в устройстве и обеспечивает экономичную эксплуатацию стекловаренных печей.
Температура наружной поверхности свода снижается с 250°С до 90°С. Удельный расход топлива сокращается в среднем на 10%.
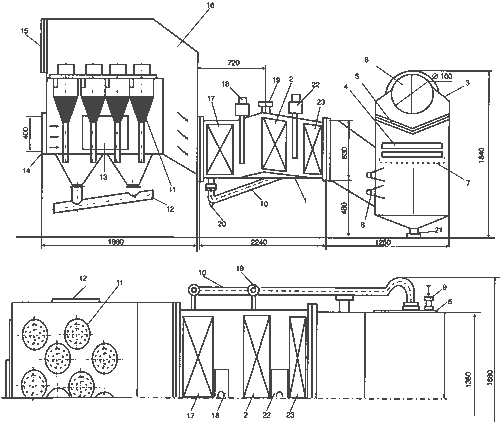
Рис. 3: 1 — экономайзер; 2, 17, 23 — трубные пучки; 3 — барботажный аппарат; 4 — коллектор; 5 — жалюзийный сепаратор; 6 — выход очищенного газа; 7 — распределительная решетка; 8 — коллектор с форсунками; 9 — подвод холодной воды; 10 — соединительный трубопровод; 11 — циклон; 12 — отвод уловленной пыли; 13, 15 — люк; 14 — подвод газа; 16 — циклонный аппарат; 18, 22 — обдувочное устройство; 19 — выход горячей воды; 20 — дренаж; 21 — слив конденсата.
3.2. Рекомендуется применение разработанного институтом "Белгипростром" комплекса по утилизации тепла и очистке отходящих газов стекловаренных печей (рис. 3). За счет их тепла осуществляется нагрев воды для горячего водоснабжения производства. Комплекс также обеспечивает эффективную многоступенчатую очистку отходящих газов от пыли, содержащей соединения свинца, цинка, калия, мышьяка, бора, бериллия, стронция и других вредных веществ. Объем отходящих газов - 9,2 тыс. м 3/час. Температура на входе 400-500°С, на выходе - 60°С. Степень очистки газов - 99,3%.
4. Повышение температуры факела способствует сжиганию топлива с минимальным коэффициентом избытка воздуха. Практически осуществить это довольно трудно, так как при этом возможно неполное сгорание топлива с вытекающими отсюда отрицательными последствиями. Следует отрегулировать процесс горения таким образом, чтобы коэффициент избытка воздуха не превышал 1,05-1,1. Для этого необходимо исключить или хотя бы сократить до минимума подсос холодного воздуха в регенераторы и печь. Повышению температуры факела способствует также увеличение температуры подогрева воздуха, идущего на горение, что связано с повышением эффективности работы регенераторов за счет использования эффективных насадок.
Повышению эффективности использования энергии факела способствует увеличение степени его черноты. Как известно, излучательная способность факела природного газа значительно ниже излучательной способности факела мазута (соответственно 0,2-0,25 и 0,5-0,60). Видимо, этим и объясняется понижение производительности стекловаренных печей при переводе их с жидкого топлива на газ. Возможным, но нежелательным путем является использование комбинированного газомазутного отопления стекловаренной печи.
5. Большое значение в интенсификации процесса теплопередачи от факела к шихте и стекломассе имеет повышение степени покрытия факелом зеркала стекломассы, приближение факела к нему, улучшение смешения топлива с воздухом. Поэтому следует применять нижний подвод топлива, плоскофакельный и веерообразный способы сжигания топлива, горелки с предварительным смешением топлива и воздуха, регулирование длины факела с использованием сжатого воздуха.
6. Использование галоидных соединений позволяет снизить температуру появления жидкой фазы на 150-200°С и соответственно получить существенный (до 15-20%) прирост производительности стекловаренных печей. (Однако применение химических ускорителей плавления увеличивает токсичность выбросов из печи.)
7. Рекомендуется применение при производстве плоского стекла эффективного флоат-способа, который характеризуется меньшим удельным расходом энергии. При современном производстве листового стекла флоат-методом стекловаренные ванные печи должны иметь производительность до 800 т/сутки. При этом методе лента стекла формируется на расплаве олова в флоат-ванне, которая состоит из бассейна с расплавленным оловом и свода (рис. 4). Пространство между бассейном и сводом по всей длине флоат-ванны заполнено смесью азота и водорода, выполняющей функцию защитной атмосферы и предохраняющей олово от окисления.
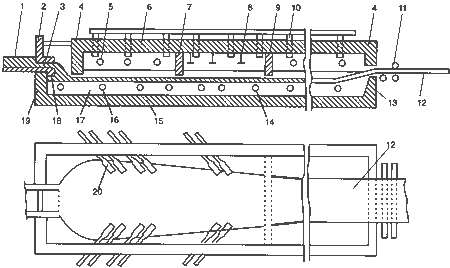
Рис. 4: 1 — стекломасса; 2 — шибер; 3 — сливной лоток; 4, 13, 19 — стены ванны; 5, 16 — регуляторы температуры; 6 — свод; 7, 9 — перегородки; 8, 14 — нагреватели; 10 — трубопровод; 11 — тянульное устройство; 12 — лента стекла; 15 — бассейн; 17 — расплавленное олово; 18 — стекло; 20 — растягивающий ролик.
8. Полезно применение гранулированной шихты, в которую вводится щелочь в виде едкого натра, что позволяет повысить прочность гранул до 17 кг/см 2. В результате уменьшаются потери шихты при транспортировке. Кроме того, частичная замена соды едким натром позволит повысить производительность печи, снизить температуру варки на 25-30°С при улучшении качества стекломассы и сократить расход топлива на 5%.
9. Экономит топливо и замена кальцинированной соды каустической, которую вводят в шихту в виде 50%-ного водного раствора. Шихта имеет 5-7% влаги. Специальная установка с автоматической системой позволяет вводить каустик за 30 секунд в любом периоде цикла смешивания. При этом расход топлива при хорошем качестве стекла уменьшается на 5%.
10. Дает экономию применение газотурбинных установок, в которых используется тепло отходящих газов стекловаренных печей для получения пара высокого давления. Вырабатываемая электроэнергия используется на производстве. В зависимости от типа стекловаренных печей затраты на электроэнергию при такой утилизации тепла могут быть снижены на 25%.
11. В целях экономии топлива может осуществляться интенсификация теплообмена в рабочем пространстве печи. Для этого используется система сжигания мазута с вводом форсунок под горелками, что позволяет снизить расход топлива на 10%. Эта система может быть применена в печах с площадью от 53 до 66 м 2. Кроме этого, печи оборудуются дополнительным электроподогревом мощностью 375, 700 или 850 кВт. Повышение энергетической эффективности варки обусловлено конструкцией форсунок, которые обеспечивают необходимый угол раскрытия пламени и оптимальную степень распыления. Это позволяет снизить расход воздуха на распыление на 25-50% (при расходе условного топлива 1520 кг/час расход воздуха снижается до 4,2-5,6 м 3/мин).
12. К новым тенденциям развития стекловарения относится переход на электроварку. Этот метод много лет успешно применяется в европейских странах. Средний удельный расход электроэнергии в электроварочной ванне производительностью 12 т/сут. и установленной мощностью 650 кВт при нормальных производственных условиях составляет 1 кВт/ч на кг стекла.
Преимущества этих электропечей сводятся к следующему:
- при одинаковой производительности варки электропечи могут быть значительно меньшими по размерам, чем печи, работающие на топливе;
- доля капитальных вложений в затратах на варку стекла, производимого в электропечах, ниже, чем производимого в обычных ванных печах;
- электроварочные печи легче поддаются автоматизации технологического процесса;
- улучшаются экономические показатели.
13. В отдельных случаях во избежание роста тепловых потерь из-за увеличенного соотношения общей поверхности стенок электроплавильной ванны и ее емкости применяется трехсекционная ванна (при этом печь сохраняется как единое целое). Расход энергии в этой печи составляет 0,95 кВт/ч на 1 кг расплавленного стекла.
14. Снижение расхода топлива и электроэнергии обеспечивается за счет широкого использования в качестве сырья боя стеклотары. Это дает возможность снизить температуру варки, а также сократить количество вредных выбросов.
Леонид СОКОЛОВСКИЙ,
начальник главного управления строительной науки и нормативов Министерства архитектуры и строительства РБ
Строительство и недвижимость. Статья была опубликована в номере 15 за 2001 год в рубрике энергетика