И крупнопанельные дома могут быть «рациональными»
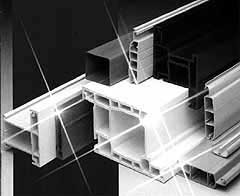
Ударное разрушение. Существует большая группа испытаний, позволяющих оценить механические свойства экструдированных профилей при ударном воздействии со скоростью 2-4 м/сек. Эти испытания проводят на маятниковых копрах. Образец, расположенный на опорах, разрушается под действием свободно падающего маятника, вращающегося вокруг горизонтальной оси. Так как измерение усилий и деформаций при этих скоростях усложняет испытания, обычно определяют работу, затраченную на разрушение (по разности энергий маятника до и после удара по образцу).
В СНГ и других странах это испытание проводят при ударном изгибе образца, свободно лежащего на двух опорах, ударом молота по середине образца (по Шарпи). При этом определяют ударную вязкость по формуле:
a = A/F,
где А - работа, затраченная на разрушение образца, F - площадь поперечного сечения образца в месте надреза.
Испытания при очень малой энергии разрушения ведут при скорости движения маятника 2 м/сек (не стандартизована); наиболее часто используется скорость 2,9 м/сек, при большой ударной прочности материала - 3,8-4,0 м/сек. Для определения влияния концентраторов напряжения на разрушение эластичных материалов испытывают образцы с надрезом на 1/3 толщины.
В США, Англии и других странах используют испытания на ударный изгиб консольно закрепленного образца с надрезом (по Изоду). Достаточно широко проводят специальные испытания на удар: по Динстату (для малых образцов); на ударное растяжение образцов, не разрушающихся при изгибе; на ударный прорыв пленки падающим шаром. Испытание на удар по Динстату состоит в определении работы разрушения при ударе молотом по пластине размером 10х15 мм (толщина 1,5-4,5 мм) вдоль линии ее закрепления в зажиме. На некоторых копрах, помимо устройств для регистрации работы разрушения, устанавливают датчики и электронные регистраторы для измерения деформации образца при ударе и записи кривой "усилие - время".
Хрупкость. Этот показатель характеризует способность материала разрушаться под действием нагрузки без существенной деформации. При испытаниях на хрупкость образец нагружают с постоянной скоростью при различных температурах и определяют, при каких температурах материал начнет разрушаться, не достигнув заданной деформации (ГОСТ 10995-64). Учитывая эластичность материалов и размеры образцов, выбирают такую деформацию, которая обеспечивает наилучшую воспроизводимость результатов.
За температуру хрупкости принимают температуру, при которой разрушается 50% образцов. Схема закрепления образца и нанесения удара при испытании на ударный изгиб по Изоду:
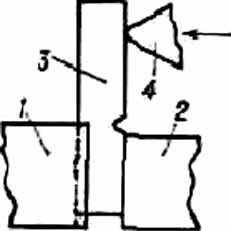
1 - неподвижная опора с пазом для помещения образца; 2 - подвижная опора для крепления образца в пазу неподвижной опоры; 3 - образец; 4 - ребро ударного молота маятника в момент соприкосновения с образцом (стрелкой показано направление удара).
Критерием разрушения служит разделение образца на две части или появление на нем трещин. Температура хрупкости зависит от вида деформации. Большинство методов определения температуры хрупкости основано на проведении испытаний при изгибе. В различных стандартах эти определения проводят: сжатием петли; обматыванием вокруг стержня по винтовой линии (британский стандарт); смятием цилиндра из пленки вдоль продольной оси. Наиболее часто применяют консольный изгиб. При изгибе на одной из поверхностей удается получить в малом объеме образца большие деформации растяжения, которые приводят к его разрушению. Однако размеры деформаций на поверхности образца сильно зависят от его толщины. Для испытания образцов разной толщины используют растяжение. Образцы пленочных материалов, где важно определить хрупкость в разных направлениях, вырезают с различной ориентацией относительно осей анизотропии и определяют показатель для каждого направления. При повышении скорости деформации повышается температура хрупкости. Стандарты АSТМ и ИСО рекомендуют испытания при сравнительно высокой скорости (2 м/сек), английский стандарт - при малой.
ГОСТ предусматривает две скорости (0,075 и 2 м/сек) с тем, чтобы можно было определить не только температуру хрупкости, но и тенденцию ее изменения с изменением скорости (разница между двумя вариантами, предусмотренными ГОСТ, достигает 15-20°С). Испытания проводят в жидкой или воздушной среде.
Теплостойкость. Этот показатель характеризует способность пластмасс сохранять свои механические свойства при непрерывном повышении температуры и выражается температурой, при которой под действием заданной нагрузки деформация достигает определенного значения. Методика определения теплостойкости состоит в следующем. Образец, находящийся под деформирующей нагрузкой, непрерывно нагревают со скоростью 1°С/мин. Температура, при которой деформация достигает заданного значения, характеризует теплостойкость. Кривые "деформация - температура", как правило, не строят.
Наиболее распространены методы определения теплостойкости: по Мартенсу (ГОСТ 15089-69) - консольный изгиб при напряжении 5 МН/м2 (50 кгс/см2); по Вика - вдавливанием цилиндра сечением 1 мм'2 под действием нагрузки 10 или 50 Н (1 или 5 кгс) на глубину 1 мм; двухопорный изгиб при одном из нескольких стандартизованных напряжений (ГОСТ 12021-66, А8ТМ, ИСО). Теплостойкость существенно зависит от нагрузки: чем больше нагрузка, тем ниже теплостойкость. Поэтому часто оценивают поведение материалов при различных нагрузках. Предусмотренные ГОСТ 12021-66 три нагрузки позволяют оценить не только теплостойкость, но и характер ее падения с увеличением нагрузки. Теплостойкость широко применяют при контрольных испытаниях, когда надо следить за изменением температурных границ стабильности материала, то есть при отверждении, пластификации.
Упруго-гистерезисные свойства и релаксация напряжений. Для определения динамического модуля и механических потерь в пластмассах широко применяют методы, основанные на возбуждении в образце резонансных механических колебаний малой амплитуды.
Наиболее распространен метод определения динамического модуля сдвига при свободных крутильных колебаниях образца (в виде полоски или цилиндра) на крутильном маятнике, а также испытания при изгибных колебаниях свободно лежащего или закрепленного в зажиме образца или образца с системой подвешенных на нем маятников для определения динамического модуля упругости и потерь. Модуль определяют, измеряя резонансные частоты и размеры образца. Определения механических потерь пластмасс при больших амплитудах высокоскоростного ударного воздействия не получили широкого распространения.
Испытания на релаксацию напряжений наиболее часто проводят при постоянной деформации растяжения или сжатия (последний вид нагружения нередко оказывается предпочтительным, так как в этом случае можно исследовать малые количества материала и избежать методических трудностей, связанных с креплением образцов).
Для исследования релаксационных свойств образец деформируют на заданное значение, которое затем поддерживают строго постоянным; падение напряжения регистрируют во времени. Релаксационные свойства материала наиболее полно характеризуются семейством кривых "напряжение - время", полученных при разных значениях деформаций и температуры. Кривые "напряжение - время" выражают аналитически и графически.
Аппаратура для испытаний на релаксацию напряжений должна отвечать следующим требованиям: силоизмеритель должен обладать максимальной жесткостью, чтобы не искажать кривую релаксации напряжений, а нагружающее устройство должно обеспечивать максимально быстрое приложение нагрузки, свободное от инерционных перегрузок (для определения релаксации напряжений при малых временах). Образцы для испытания, рабочие органы испытательных машин и условия испытания обычно выбирают в зависимости от вида деформации, как при определении вида зависимости "напряжение - деформация". Для испытания на релаксацию напряжения используют релаксометр осевого сжатия и универсальные испытательные машины с электронным силоизмерителем. Хотя испытания на релаксацию напряжений пока не стандартизованы, их широко применяют как при разработке пластмасс, так и при инженерной оценке (например, при испытании уплотняющих ПВХ профилей).
Ползучесть и длительная прочность. Под ползучестью понимают увеличение деформации материала со временем под действием постоянной нагрузки или напряжения. Ползучесть проявляется как частный случай общей зависимости деформации от напряжения температуры и времени.
Для общей характеристики материалов обычно ограничиваются определением ползучести при растяжении и сжатии. Ползучесть при растяжении и постоянной нагрузке используют для оценки жестких материалов, а при постоянном напряжении - для оценки материалов, сильно деформирующихся (более чем на 10%) при нагружении. Постоянство напряжений поддерживают приспособлениями, автоматически уменьшающими нагрузку пропорционально уменьшению поперечного сечения образца. Испытательная нагрузка при исследовании ползучести составляет 10-90% (наиболее часто 25-40%) от значения прочности, полученного при кратковременных испытаниях на растяжение. Испытания при растяжении производят на таких же образцах, какие используют при кратковременных статических испытаниях.
В связи с сильной зависимостью ползучести от температуры, колебания последней должны быть минимальными (иногда (0,5°С). Для испытания пластмасс на ползучесть можно использовать серийные приборы РПУ-1 (растяжение при температурах до 300 °С при максимальных постоянных нагрузках соответственно 10 и 1 кн (1000 и 100 кгс)) и установки с изменяющейся в ходе опыта нагрузкой для испытаний при программируемом нагружении.
Под длительной прочностью (долговечностью) понимают напряжение, которое вызывает разрушение материала за данное время. Длительную прочность обычно определяют одновременно с ползучестью (если последняя представляет интерес). Требования к условиям испытаний и к образцам в обоих случаях одинаковы. Отличие состоит: в размере нагрузки, которая обычно несколько выше, чем при определении ползучести (так как требуется разрушить материал); в необходимости фиксировать момент разрушения; в количестве образцов - их требуется больше, чем при испытании на ползучесть вследствие большего разброса данных.
Таким образом определяются прочностные свойства столь популярных сейчас на рынке стройматериалов экструдированных ПВХ профилей; при определении фирмы-поставщика такого товара потребителю неплохо убедиться в компетентности производителя в вопросе прочности ПВХ профилей по вышеприведенным параметрам, чтобы не потратить средства впустую.
Владимир КОВАЛЬ belprod@belsonet.net
Строительство и недвижимость. Статья была опубликована в номере 40 за 1999 год в рубрике материалы и технолгии