Прогресс в экструзии строительных ПВХ профилей: экструдеры
Прогресс в технологии экструдирования профилей для различных отраслей экономики, а особенно для строительства, обусловил в последние 2 года возможность резко повысить производительность экструзионных линий, улучшить качество строительных профилей (особенно ПВХ профилей), применять новые полимерные и натуральные материалы, выпускать профили, сложность сечений которых делала ранее их выпуск невозможным. Это относится как к оконным ПВХ профилям, так и к отделочным профилям (siding, cladding), прочим.
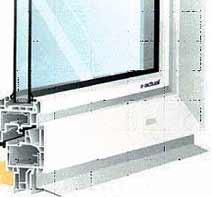
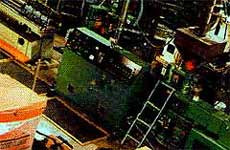
Потребителя сейчас не устраивает относительное однообразие профилей в начале 21 века. Прогресс в данных отраслях машиностроения и полимерах вполне отвечает новым требованиям, что наглядно демонстрирует, например, прошедшая международная полимерная выставка "Kunststoffe 98" в Дюссельдорфе.
В настоящее время более 80% ПВХ профилей для строительства производится на двухшнековых экструдерах. Но повышенная производительность таких экструдеров вызывает и повышенные усилия на опорные подшипники и повышенное трение на внутренних стенках рабочих цилиндров экструдеров. Фирма "Battenfeld" разработала особую геометрию шнеков полностью устраняющую эти негативные явления, что и было отмечено медалью от администрации VDMA.
Фирма "Cincinnati-Milacron" решила эту проблему, разработав новую конструкцию четырехступенчатой коробки передач привода рабочих шнеков, при которой большая производительность по ПВХ профилям достигается при сравнительно низких оборотах шнеков (26 об/мин) для экструдера Argos 93. В этом случае и перерабатываемое сырье - ПВХ компаунд обретет оптимальные реологические характеристики. В итоге этого усовершенствования эктрудер с параллельными шнеками Argos 93 этой фирмы приобрел производительность для ПВХ профилей - 380 кг в час, для труб - 600 кг в час. К тому же, коэффициент L/D (отношение длины шнека к его диаметру), равный 26, обеспечивает наилучшее время резиденции ПВХ компаунда в рабочем цилиндре и наилучшую его гомогенизацию и теплопередачу вследствие увеличения площади поверхности теплообмена между металлическими стенками цилиндра и расплавом ПВХ.
По этому же пути идет и производитель экструзионного оборудования "Krauss-Maffei".
Его новые профильные экструзионные линии на основе новых двухшнековых параллельных экструдеров имеют производительность большую, по сравнению с предыдущими моделями, - на 40%. При L/D = 26 и диаметрах шнеков 75, 90, 114, 130 и 160 мм в этих экструдерах также наилучшим образом происходит гомогенизация расплава ПВХ, теплообмен, а также уменьшена скорость сдвига, что наилучшим образом сказывается на качестве ПВХ профилей. К тому же, в них применен новый электромотор постоянного тока с крутящим моментом, большим на 50%, по сравнению с предыдущими моделями. В них все коробки передач снабжены двойными зубчатыми трансмиссиями с плавающими зубчатыми шестернями, адекватно воспринимая резкие перепады продольной нагрузки на валы, что не позволяет резко меняться характеру переработки ПВХ компаунда в экструдере. Поперечные кольцевые электромуфты передают вращающий момент от мотора к валам рабочих шнеков и снижают уровень шума. Повышенное вращающее усилие позволяет шнекам беспроблемно перерабатывать ПВХ компаунд даже при полном питающем бункере. Уменьшить перегруз материала в питающей воронке при запуске можно в этом случае как с помощью дозирующей системы с электронным управлением, так и регулируя питающий шнек вручную.
"Универсальность" - любимый лозунг еще одного производителя экструзионной техники для ПВХ профилей - итальянского концерна "L. Bandera".
В последний год он разработал новую серию экструдеров 2B с повышенным значением вращающего момента для экструдирования больших профилей, особенно оконных, достигающих веса 1450 грамм / линейный метр. Но, несмотря на это, линия настраивается очень легко, как и для маленьких и легких профилей. Трехступенчатая планетарная коробка передач передает вращающее усилие на вал каждого шнека через кольцеобразное зубчатое колесо. Большие продольные усилия воспринимают упорные роликовые подшипники, совмещенные с опорами на картере коробки.
Новая геометрия шнеков экструдера увеличивает производительность экструзионной линии без увеличения скорости вращения шнеков и способствует снижению скорости сдвига расплава ПВХ компаунда в рабочем цилиндре экструдера и улучшению его операционных свойств. Повышение скорости экструдирования ПВХ профилей возможно благодаря применению мощных электромоторов, коэффициенту L/D = 20 и крутящему моменту на каждый шнек не менее 25000 Nm.
Особый подход к решению этой проблемы демонстрирует фирма "Welex" (США).
Тяжелые профили (к ним относятся и оконные ПВХ) профили производятся со все более возрастающей производительностью с помощью дополнительной установки специального шестеренчатого насоса перед экструзионной фильерой. Этот узел придает расплаву ПВХ отличные реологические характеристики, одновременнй градиент скорости в любой точке сечения профиля и устраняет спиральную составляющую скорости частицы расплава ПВХ при выходе из рабочего цилиндра, что в конечном итоге приводит к повышенному качеству поверхности строительных ПВХ профилей. Подобные насосы широко применяются в серийных экструдерах Mark 1 фирмы "Welex" с диаметрами шнеков от 35 до 90 мм и L/D от 24 до 30.
"Welex" также применяет в некоторых своих экструдерах особые статические миксеры, для устранения "памяти" вязкоэластичной деформации расплава ПВХ при выходе из рабочего цилиндра, которая значительно ухудшает качество поверхности строительных ПВХ профилей, что представляет порой неразрешимую проблему для фирм-новичков в экструзии строительных ПВХ профилей (особенно это относится к восточноевропейским и отечественным (СНГ) фирмам).
Фирма "Davis-Standard" (США) недавно продемонстрировала в действии профильную экструзионную линию на основе серийно выпускаемого двухшнекового экструдера "Gemini 94"с параллельными шнеками для производства оконных ПВХ профилей с производительностью 5 м/мин тяжелого оконного профиля. Данный экструдер оснащается воздушной, масляной или водяной системами охлаждения усовершенствованного цилиндра, что благотворно сказывается на качестве поверхности оконного ПВХ профиля. Кроме того по-новому нарезаются зубья приводных шестерен, что позволяет валам воспринимать большую продольную нагрузку и крутящий момент, не увеличивая конструкцию опорных подшипников. (На фото - серийный двухшнековый экструдер "Gemini 94").
Новые системы контроля улучшают производительность экструзии ПВХ профилей и их качество.
Новый тип лазерного сканера для контроля качества экструдируемых строительных ПВХ профилей предлагает фирма "Scantron" (Англия).Эта система позволяет почти вдвое увеличить производительность профильных экструзионных линий без ухудшения качества профиля.
Сечение ПВХ профиля, выходящего из экструзионной фильеры, постоянно сканируется плоскостью лазерной развертки.
В соответствие с требуемым заданием или обнаруженными дефектами, регулируются главные операционные характеристики линии (скорость вращения рабочих шнеков, скорость вытягивания профилей, температурное регулирование процесса) через hardware встроенного процессора. (На фото - пример работы лазерной контрольной системы при экструдировании трубного профиля). Вся система настроена на максимальное снижение отходов ПВХ.
"Krauss-Maffei" усовершенствовал систему своих встроенных на экструзионных линиях микропроцессоров С4. Теперь, кроме увеличения скорости обработки данных, в hardware включен высокоскоростной модем, через который абсолютно все данные экструзии поступают на главный сервер цеха, могут отслеживаться как оператором, так и автоматически, анализируются ошибки и исполнительным механизмам выдаются команды для их устранения. Таким образом, один инженер-оператор может вполне управлять работой огромного цеха, состоящего из десятков мощных ПВХ экструзионных линий, отслеживая главные параметры работы линии on-line control - вращающий момент шнеков, температура и давление расплава ПВХ по зонам, тянущее усилие вытяжных устройств.
Учитывая, что высокая производительность экструзии строительных профилей делает ручной контроль за экструзионной линией непрактичной, Институт Пластмасс в Аахене разработал систему непрерывного контроля за качеством экструдируемого ПВХ профиля на основе трех видеокамер, расположенных в пространстве после экструзионной фильеры под углом 120° друг к другу. Видеосигнал передается на микропроцессор, возможные отклонения обрабатываются, предлагается несколько вариантов решения неполадок с помощью операционных мер, и вся эта информация передается на центральный сервер к оператору.
Для усиления точности контроля фирма "Welex" (США) применяет в своих контрольных системах цифровую обработку данных в сетях постоянного тока. Цифровая передача показывает свое превосходство в определении экструзионных параметров (температура, давление, скорость и напряжение сдвига) по сравнению с аналоговыми системами (как, например, в машинах фирмы "Nissel" (Япония)).
Остается только пожалеть, что те несколько экструзионных фирм в СНГ, которые производят строительные ПВХ профили (в основном оконные), пока не имеют возможности (и главное - желания) следовать этим новинкам, чтобы противостоять в конкурентной борьбе с импортерами этой продукции из Европы. Только в одной Германии таких фирм - 68, все они увеличивают темпы производства ПВХ профилей и не стремятся уступить рынок стройматериалов в СНГ кому-либо.
Владимир КОВАЛЬ, belprod@belsonet.net
Строительство и недвижимость. Статья была опубликована в номере 06 за 1999 год в рубрике технологии