Бетонирование туннеля при помощи техники Peri и Putzmeister
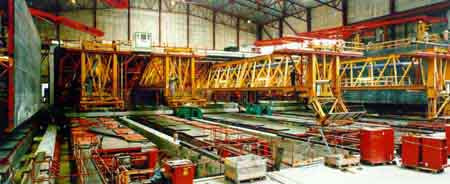
В состав транспортной системы войдут четырехполосная автомагистраль и двухпутевая железная дорога. 16-километровый отрезок транспортной системы, проходящий по искусственному полуострову, соединит Копенгаген и Орезунд. Из этого участка пути 3,7 км приходится на подземный туннель, 4 км - на надземные пути на искусственном острове, 7 845 м - на мосты, соединяющие остров со шведским берегом. При строительстве подземного туннеля "Drogden" потребовалось выполнение большого объема работ по бетонированию его стенок (около 700 000 м3 бетона). Эта сложная в конструктивном, техническом и технологическом отношении задача была решена за счет использования специальных опалубочных систем немецкой фирмы "Peri" и бетононасосов немецкой фирмы "Putzmeister".
"Плавающая" вертикальная опалубка
Проектировщики из фирм "Peri" и "Putzmeister" подсчитали, что для ускорения темпов работ по строительству туннеля необходимо возведение 160 монолитных железобетонных сегментов длиной 22, 25 м, шириной 42 м и высотой 8,5 м. Из этих сегментов должен был быть составлен гигантский железобетонный элемент длиной 178 м и весом 60 000 тонн. Из 20 таких элементов и предполагалось составить стенки подземного туннеля. Сегменты изготавливались на двух производственных линиях одного из заводов железобетонных изделий в Копенгагене. Особенностью такого производства являлась необходимость соблюдения высокой точности размеров элементов. Профили сегментов должны были иметь отклонения от заданных размеров, не превышающие 5 мм. В противном случае возникли бы сложности с герметизацией стенок туннеля. Также предполагалось, что бетонные конструкции будут установлены с минимальным количеством анкерных креплений. Изготовление бетонных элементов, отвечающих этому требованию, стало возможным за счет использования специальных опалубок с высотой стенок от 8,5 м. Для обеспечения абсолютной водонепроницаемости бетонных конструкций отверстия, предназначенные для установки анкеров, в процессе изготовления бетонных элементов замазывались двухкомпонентным клеевым раствором. Изготовление бетонных элементов велось с учетом требуемой геометрии стенок туннеля. Толщина бетонных плит варьировалась: уменьшалась в верхней отметке и увеличивалась в середине. В бетонных плитах также были предусмотрены отверстия для вентиляционных ниш. Для наилучшей укладки бетонных элементов они изготавливались с определенными скосами, соответствующими наклону стенок туннеля. Каждая из плавающих опалубок использовалась более 50 раз.
Опалубочные установки - комплексная система изготовления
Для решения наиболее сложных задач по изготовлению элементов по бетонированию туннеля применялись "тяжелые" опалубочные установки фирмы "Peri" весом 1 155 тонн. Из-за дефицита времени, отведенного для производства работ по бетонированию, использовался метод наиболее быстрого изготовления монолитных железобетонных изделий. Каждая опалубочная установка открывалась и закрывалась механизированным гидравлическим способом. Нижняя плита и боковые стенки опалубки фиксировались в постоянном положении, а верхняя часть поднималась и опускалась по ступенчатой технологии. Внутренняя структура опалубки использовалась для формообразования бетонной "трубы" туннеля, в которой предполагалось впоследствии разместить подземную автомагистраль и железнодорожные пути. В процессе изготовления бетонных элементов были использованы специальные фермы длиной 50 м, высотой 4 м и весом 52 тонны. Их задача заключалась в том, чтобы не допустить контакта железобетонных сегментов и внутренней оболочки опалубки. Во время процесса бетонирования, который длился в различных случаях от 32 до 40 часов, собственный вес сегментов и опалубки, составляющий в совокупности 8 050 тонн, давил на основание опалубки. Этот вес равномерно распределялся на 250 единичных стоек.
После того как сегменты из бетона набирали проектную прочность, основание и боковые стенки опалубки снимались. После этого сегменты и внутренняя часть опалубки перемещались по передвижной ленте-транспортеру, которая приводилась в действие гидравлическим методом. Когда 380-тонный корпус сооружения достигал следующей отметки разреза бетона, внутренняя часть опалубки изымалась из готового сегмента туннеля и начиналось изготовление следующего сегмента. После того как было завершено изготовление типовых сегментов, опалубочная установка перенастраивалась на производство сегментов с другой конфигурацией поперечного сечения. Производство этих бетонных изделий также осуществлялось по рассмотренной выше технологии.
Скорость строительства и его качество
Уже во время изготовления первого монолитного железобетонного элемента для оборудования туннеля стало ясно, что новая технология позволяет значительно ускорить процесс бетонирования. Большую роль здесь сыграло и то, что при проектировании железобетонных конструкций учитывались все требования, предъявляемые к строительству подземных транспортных сооружений. В соответствии с этими же требованиями был осуществлен выбор опалубочной техники. Применение установок "Peri" позволило избежать временных затрат, связанных с производством работ по монтажу железобетонных конструкций. Что касается окончательного монтажа изготовленных монолитных сегментов, то для его выполнения также привлекались специалисты из фирмы "Peri". На выбор опалубочной системы повлиял и такой фактор, как итоговое качество строительных работ. А этот критерий подтверждался тем, что техника "Peri" имеет сертификаты, соответствующие западноевропейским строительным нормам. Тендерная документация, представленная фирмой "Peri" на конкурс, включала в себя 800 чертежей конструкций, описание технологии монтажа, эксплуатации и ремонта конструкций на 750 страницах и 300 страниц, посвященных сертификации качества предлагаемой техники.
Концепция поэтапного бетонирования
Успешное выполнение строительства туннеля стало возможным за счет оптимального сочетания двух важных составляющих: опалубок "Peri" и бетононасосов фирмы "Putzmeister". Возможности совместной работы этих двух видов техники были рассмотрены еще на планировочной стадии проекта. Проектировщики совместно с ассистентами по обслуживанию машин "Putzmeister" были проинформированы по поводу технических возможностей транспортировки и распределения бетонной смеси. До начала строительства были еще раз изучены характеристики предлагаемого бетона, а также определена квалификация персонала, занимающегося эксплуатацией и сервисным обслуживанием машин "Putzmeister". В итоге была разработана концепция поэтапного бетонирования, включающая в себя многочисленные факторы: круглосуточное техническое обслуживание бетононасосов, определение степени риска их повреждений, расчет экономической эффективности предлагаемого решения, расчет износостойкости машин и другие важнейшие параметры. Вся эта информация была предоставлена инженерно-техническим службам заказчика для изучения и принятия окончательного решения. Минимальные затраты на техническое обслуживание машин "Putzmeister" и максимальная эффективность их использования стали основными критериями, повлиявшими на выбор, сделанный заказчиками.
Все работы по бетонированию туннеля характеризовались высокой степенью их механизации. В частности, для автоматизированной подачи бетона на требуемую высоту были использованы шесть стационарно действующих машин типа BSA 2109 D, которые устанавливались в специальных звукоизолирующих контейнерах с ваннообразными основаниями. Четыре бетононасоса работали постоянно, в то время как две остальные машины начинали функционировать только по команде интегрированного аналитического центра системы, оснащенного гидравлическими трубопроводами и транспортировочными шлангами. Эта мера безопасности позволила своевременно ликвидировать дефекты бетонирования, допущенные стационарно работающими машинами.
Подготовка бетона и доведение его до требуемой консистенции производились в высокомощных бетономешалках, рассчитанных на подготовку 10 000 литров бетонной смеси каждая. Специальные устройства, встроенные в бетономешалки, регулировали количество добавок в бетонную смесь. Для того чтобы обеспечить последующую укладку трубопроводов и других компонентов инженерных сетей, из монолитного бетона были изготовлены специальные корпуса шириной 100 и длиной 80 м. В этих корпусах с шагом 29 м были установлены разделительные мачты, отделяющие рабочее пространство от опалубки. Кроме них, еще две мачты были установлены снаружи сооружения. С их помощью обеспечивалась укладка дополнительных трубопроводов.
Монолитная технология строительства
Разделительные мачты должны были использоваться довольно длительное время. Для того чтобы мачты не повредили бетонные корпуса, применялись дополнительные противовесы. Часть расстояния в свету между двумя стационарно установленными мачтами занимали портальные краны.
Специальный блок управления контролировал работу бетононасосов. Благодаря гидравлически управляемой задвижке бетонная смесь направлялась по точно заданной траектории. При бетонировании опалубочные установки, снабженные шлангами, соединялись с разделительными мачтами при помощи гидравлически управляемых трубопроводов типа DVH 5/2. Эти трубопроводы фиксировались в зоне установки радиальных разделительных элементов. Благодаря такому решению при армировании можно было достичь радиусов 6 и 7 м. Данная концепция бетонирования позволила быстро выполнить конструктивные элементы, ограничивающие пределы рабочего помещения. Все 16 радиальных разделительных элементов, которые образовали специальную конструкцию, свободно контактирующую с внутренней частью опалубки, и шесть стационарно установленных мачт обеспечили возможность монолитного бетонирования.
Как только радиальные разделительные элементы были закреплены на основании опалубки, с него открепили разделительные мачты и гибкие трубопроводы. После удаления гибких трубопроводов при помощи вертикальных опалубок были отлиты мачты из бетона. Для обеспечения максимальной надежности и безопасности такого метода бетонирования при проходке бетононасосов стандартные шланги длиной 8,5 м были заменены на более короткие шланги длиной 4 и 6 м. Во время процесса бетонирования специалистами фирмы Putzmeister осуществлялось круглосуточное сервисное обслуживание бетононасосов и разделительных мачт. Благодаря всему комплексу рассмотренных выше мер бетонирование подземного туннеля было выполнено на высоком качественном уровне.
Елена ИНОЗЕМЦЕВА
Строительство и недвижимость. Статья была опубликована в номере 49 за 1997 год в рубрике техника