Выпуск оконных блоков с тройным остеклением
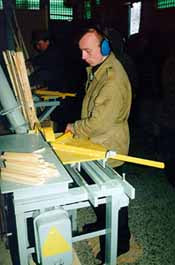
- Сегодня мы постарались собрать здесь всех, кто производит строительные столярные изделия на территории РБ. Известно, что расход энергоресурсов на единицу любой производящейся у нас продукции примерно в 2 раза выше, чем в Европе. Мы, далее, строим такие здания, на обогрев единицы площади которых расходуется в 1,5-2 раза больше тепла, чем в Европе, в том числе и Северной. С другой стороны, своих энергоресурсов в республике имеется всего 10% от потребляемого ею количества. Остальные 90% мы покупаем за валюту. Задача, таким образом, состоит в том, чтобы как можно быстрее сделать все шаги, необходимые для достижения европейского уровня экономии энергоресурсов. В республике кое-что делается в этом направлении, более того, есть информация, что делается несколько больше, чем в остальных странах бывшего СССР. Это не должно нас успокаивать, более того, складывающаяся экономическая и политическая ситуация побуждает нас действовать чрезвычайно оперативно. Необходимые наработки в республике есть, пример - деятельность предприятия, на котором мы с вами находимся.
Однако сегодня, к сожалению, ОАО "Лидастройматериалы" - одно из немногих предприятий республики, которое, не привлекая дорогостоящие западные технологии и оборудование, а пользуясь лишь отечественным, к тому же весьма изношенным, не только превосходит прочие по части энергосбережения, но и производит самое настоящее евроокно, отвечающее всем современным теплозащитнымм требованиям. Да, эта продукция вдвое дороже, чем наши обычные старые окна, но вдвое дешевле того евроокна, которое выпускают "Забудова" и "Барановичидрев". Уже с 1995 г. ОАО "Лидастройматериалы" эксплуатирует построенную им котельную, полностью работающую на отходах деревообработки. Заполнение оконного проема - это не только обрамление и остекление, это еще и окраска и фурнитура.
Мне приятно констатировать, что АО "Лидалакокраска" близка к тому, чтобы на 100% обеспечить потребность стройотрасли республики в лакокрасочных материалах, по качеству не уступающих тем импортным, что сегодня заполонили наши прилавки. Вы увидите экспозицию, подтверждающую, что уже с начала 1998 г. мы сможем комплектовать нашу столярку отечественной фурнитурой, по отдельным показателям не уступающей той, которую мы сейчас покупаем за валюту и стоимость которой, если не ошибаюсь, составляет 25-30% стоимости евроокна. Вот яркие примеры как энергосбережения, так и импортозамещения. Впереди - создание сушильных мощностей, на которых уже фрезерованные пиломатериалы будут проходить все этапы сушки древесины в соответствии с требованиями европейских строительных норм и стандартов. Бичом же нашим является разобщенность наших действий, и наиболее насущной задачей отрасли является их координация.
Наш сегодняшний семинар должен способствовать объединению усилий министерств и отраслей воедино во имя скорейшего получения результата. Именно поэтому и само мероприятие и тематика, которой оно посвящено, привлекают самое пристальное внимание правительства. Нелишне будет напомнить, что с 1 июля 1998 г. в соответствии с зарегистрированным Минюстом РБ приказом министра архитектуры и строительства РБ будет запрещена установка на любых объектах республики столярных изделий без сертификата качества. Более того, будет ставиться задача 100%-ной заводской готовности окон. То есть окно, как это повсеместно имеет место на Западе, должно быть инженерным сооружением. И это также будет зарегистрировано Минюстом РБ. Это требование жизни. Соответствия же требованиям, предъявляемым теми организациями, которые выдают сертификаты, можно достичь, в частности, перенимая опыт, накопленный ОАО "Лидастройматериалы".
Далее слово взял директор ОАО "Лидастройматериалы" П. Н. Новиков.
- Предприятие работает уже 21 год, - сказал он, - первоначально это был завод керамзитового гравия, лесопильный и столярный цеха появились потом. Общая производственная площадь составляет 13 м2. На сегодняшний день личный состав работающих насчитывает 535 человек, из них 42 - временные. Главной целью периода перестройки было выживание, сохранение коллектива во что бы то ни стало. Однако мы все время смотрели вперед, и с этого года начался рост наших показателей. Мы сохранили профиль предприятия, обслуживающего строительную отрасль, так как были уверены, что ее активная деятельность возобновится, ведь государство, которое не строит, не может долго существовать. Вопросы реорганизации и техперевооружения решались нами в комплексе. Первоначально мы покупали тепло на соседнем предприятии, котельная которого вот-вот остановится. Приняв решение строить свою котельную, мы изучили много вариантов. Первоначально был заказан и уже оплачен проект бешенковичского варианта котельной. Вариант хороший, но его нельзя было вписать в наши производственные мощности. Плюс невысокая степень механизации и автоматизации. Состав смены - 4-5 человек. Тогда-то мы и пошли на французский вариант, но, прежде чем его выбрать, мы с главным энергетиком проехали 1500 км по Франции, побывали на многих действующих котельных. В первую очередь нас беспокоили вопросы экологии, и мы посетили котельную, находящуюся в 20 км от швейцарской границы. Котельная стоит в центре города, претензий со стороны Швейцарии нет. За одну ночь мы с главным энергетиком сделали необходимые расчеты и приняли решение: котельную брать! Кредит в размере $400000 был выделен благодаря усилиям Европейского банка реконструкции и развития и "Инвестбанка". Строительство котельной мы вели хозспособом и закончили за 6 месяцев. За год работы котельная производства французского АО КОН дала нам 6 млрд рублей чистой прибыли. Благодаря эксплуатации этой котельной энергоемкость нашей продукции не превышает 5,2%, а если бы ее не построили, этот показатель составлял бы 13%. Потребность в опилках составляет 0,5 м3/Гкал. Мы не прекратили реализацию опилок и щепы Речицкому гидролизному заводу, а, наоборот, увеличили процентов на 20. Дело в том, что в качестве топлива мы теперь используем и те отходы, которые первоначально вывозили на свалку, - кору. Еще и деньги платили за то, чтобы у нас был принят этот древесный мусор. Теперь мы ежегодно экономим для республики 2 600 000 м3 природного газа.
Для производства настоящего евроокна нужна линия склейки, нужна немецкая фурнитура. Короче, рынок создан для Запада! Экономя валюту, мы создали участок филенчатых дверей. 60% действующего там оборудования изготовлено собственными силами. Первоначально мы рассчитывали выпускать 25 дверей в сутки, сейчас этот участок дает 50-70 дверей.
Результатом выполнения второй очереди реконструкции будет возможность осуществления сушки пиломатериалов. Необходимый кредит уже взят, более того, эти деньги уже уплачены за сушильные камеры. Фундаменты готовы, можно монтировать оборудование. Однако в связи с забастовкой водителей грузовиков во Франции меня попросили о месячной отсрочке поставки, и я пошел на это. Отсрочка оканчивается 7 декабря. Производительность заказанных сушильных камер фирмы "Котильд" (Франция) такова: 2 вместо 19 отечественных.
Участок филенчатых дверей начал приносить нам прибыль (рынок сбыта - Россия). Поэтому кредит, взятый для приобретения котельной, возвращен на год раньше срока.
Мы задумались: почему это мы должны один к одному делать западное окно? Почему бы не разработать свое, белорусское, взяв за основу скандинавский вариант? Уже теперь, когда это решение принято и выполняется, мы убеждаемся, посещая скандинавские стенды на строительных выставках: не считая непринципиальных изменений, конструкции изделий-аналогов остаются теми же, что и были.
Итак, сегодня мы предлагаем классические двери из массива, оконные блоки раздельно-спаренной конструкции с тройным остеклением по образцам скандинавских стран. Термосопротивление такого окна составляет 0,7 м2•.оС/Вт.
С 15 марта этого года на нашем предприятии прекращен выпуск окон с раздельными створками. В тот же день мы приступили к выпуску окон с тройным остеклением.
Немаловажно в конструкции данного окна то, что она не вступает в противоречие с архитектурой старых зданий. Наши окна можно использовать при их реконструкции. Поэтому население охотно берет эти окна в розницу. Еще одно преимущество: все 3 стекла - одного размера.
Первый заместитель министра промышленности РБ В. Г. Галко посвятил свое сообщение вопросу расширения ассортимента и повышению конкурентоспособности фурнитуры столярных изделий.
- Мы далеки от утверждения, что изготавливаемая предприятиями Минпрома РБ фурнитура не отличается от западных образцов, - подчеркнул Владимир Григорьевич, - но мы стремимся к достижению подобного качества. Совместный семинар предприятий Минстройархитектуры РБ и Минпрома РБ, прошедший осенью прошлого года в рамках выставки "Будпрагрэс-96" (см. "СиН" № 37 от 1 октября 1996 г. - Прим. авт.), побудил многие минпромовские предприятия к серьезному осознанию проблемы. В соответствии с поручением Совмина РБ была разработана программа "Фурнитура", по которой мы и работаем в настоящее время. Стало ясно, что при производстве метизов необходимо руководствоваться соответствующими евронормами. В настоящее время у нас выпускается около 170 наименований и типоразмеров строительной фурнитуры. Ее производством заняты 53 предприятия.
Например, к двум традиционным производителям замков - Минскому и Барановичскому заводам автоматических линий в последнее время присоединились Оршанский инструментальный завод, рогачевский "Диапроектор", оршанский станкостроительный завод "Красный борец". Мы поддерживаем здоровую конкуренцию всех этих предприятий.
Владимир Григорьевич призвал представителей предприятий, производящих столярку, к установлению и постоянному поддержанию обратной связи с изготовителями фурнитуры, что явилось бы залогом развития обеих отраслей. Все замечания и пожелания строителей должны фиксироваться в договорной документации, а в перспективе - в технических условиях и СТБ на метизы.
Сергей ЗОЛОТОВ
Строительство и недвижимость. Статья была опубликована в номере 47 за 1997 год в рубрике энергетика