Microtech: технологии будущего сегодня
В последнее время видна устойчивая тенденция к организации отечественных производств компьютеров и комплектующих. Это позволяет не только снижать себестоимость продукции, но и оперативно реагировать на изменения конъюнктуры рынков России и стран ближнего зарубежья, что часто оказывается решающим фактором при выборе поставщика. Плюс к этому территориальная близость дает более широкие возможности по контролю качества. В данном материале мы предлагаем вашему вниманию рассказ об уникальном российском производителе корпусов для сборки ПК — компании Microtech. Все началось с приглашения посетить завод Microtech.
Трехчасовая поездка на машине из центра Москвы — и мы вместе с представителями компании уже в Калуге, стоим у ворот предприятия. Позади 200 км. Согласитесь, это ничтожно мало по сравнению с тысячами до Китая или Тайваня. То, что довелось увидеть, действительно впечатляет, а планы по развитию производства и увеличению мощностей, с которыми нас ознакомило руководство завода, вызывают гордость за отечественного производителя. Да, Microtech — один из немногих подобных примеров, скорее даже исключение из правил, но сам факт, что компания успешно работает и развивается, не может не радовать. В 1998 г. все начиналось с одного производственного корпуса. Сегодня завод расположен уже на трех территориальных площадках. Весь технологический цикл разбит на несколько этапов. Рождение новой модели корпуса происходит в святая святых компании — КБ Microtech. Инженеры прорабатывают все вопросы от дизайна до системы охлаждения. На полках можно видеть десятки, если не сотни, образцов и разработок. Штучные корпуса, как концепт-кары, делаются для выставок и презентаций, причем любой из них может быть запущен в производство. A производство начинается с процесса штамповки. Листовой металл (электроцинк) толщиной 0,5-0,8 мм поступает в огромных полутораметровых рулонах каждый весом около 10 тонн. Для их транспортировки в цех штамповки заведена отдельная железнодорожная ветка! Чтобы получить заготовки необходимого размера, применяется специализированный станок, осуществляющий как продольную, так и поперечную резку. Из полученных заготовок и штампуют необходимые детали корпусов, которых требуется до 20 штук только на один тип шасси. Изготовление простых деталей полностью автоматизировано. Самые же сложные, например, боковые стенки шасси, изготавливаются в несколько проходов посредством десятка различных прессов, каждый из которых выполняет отдельную операцию. Причем, если заказчик пожелает, например, выдавить логотип своей компании на боковой стенке, нет проблем — перенастройка линии займет небольшое время. Но корпус — это не только металл шасси. Как правило, внешний вид компьютера определяют пластиковые детали. Именно они и изготавливаются на участке термопластавтоматов.
Из высококачественного пластика отливаются все необходимые части начиная от кнопок и заканчивая лицевыми панелями. Кстати, в цехе часть оборудования разработана и внедрена самим заводом. Это промышленные холодильники и дробильные станки. Последние предназначены для измельчения литников (технологической пластмассы) и выбракованных изделий, обеспечивая безотходность процесса. Готовые детали бережно упаковываются и поступают на покраску. Металлические части красятся "порошком", который закрепляется под термическим воздействием. Пластик красится обычным методом. Здесь же расположен станок тампопечати. Хотите нанести свое изображение или логотип — нет проблем!
И, наконец, сборочный конвейер, где производится ручная сборка — сборка под строгим контролем ОТК. Требуется совсем небольшое время, чтобы из отдельных частей получить и упаковать готовый компьютерный корпус. Работа на конвейере осуществляется очень быстро, по словам представителей, даже быстрее, чем на заводах в Юго-Восточной Азии. Одним из последних этапов является установка блока питания, который проходит продолжительное тестирование под нагрузкой в термоизолированной камере, где на специальных стеллажах стоят сотни блоков питания. К обеспечению качества в Microtech подходят щепетильно. Ни один готовый корпус не попадет на склад без отметки службы ОТК. И это при том, что контроль качества осуществляется на каждой, даже самой мелкой, операции технологического цикла. Некоторым может показаться, что технологический цикл несложен. Поверьте, это не так. Производство требует колоссальных материальных и интеллектуальных затрат, в том числе связанных с обслуживанием парка оборудования. В качестве примера упомяну лишь об инструментальном цехе. Сложно было поверить в поломку многокилограммовой оснастки, пока мы собственными глазами не увидели расколовшийся металлический штамп толщиной порядка 3 см. Имеющиеся в распоряжении современнейшие электрозионные станки и обрабатывающий центр позволяют изготовить копию в самое короткое время. При этом точность описывается микронами!
В процессе посещения нам удалось побеседовать с директором завода Microtech Евгением Владимировичем Куликовым и взять у него интервью.
Василий Запотылок: Добрый день, Евгений Владимирович! Мы только что посмотрели завод, побывали на трех производственных площадках — впечатляет! Расскажите, пожалуйста, историю становления предприятия.
Евгений Куликов: Предприятие с момента основания сохраняет высокие темпы развития. Объем выпускаемой продукции регулярно удваивается — это не голословное утверждение, а факт, подтвержденный цифрами (сейчас это свыше 1 млн корпусов в год), что позволяет нам быть высокоэффективными как по экономическим, так и по производственным показателям. Сначала весь технологический цикл размещался на площадке №1, где мы сейчас с Вами и находимся. Для первоначальных объемов выпуска этого было достаточно. Но их увеличение потребовало в 2000 г. принять решение о приобретении производственной площадки №2, а в 2003 г. — производственной площадки №3. На них расположились цеха металлообработки и литья пластмасс соответственно. Таким образом, в техпроцесс были интегрированы все три производственные площадки. Однако сейчас уже ведется разработка проекта строительства нового производственного комплекса, который будет в 4 раза превосходить все существующие производственные мощности завода!
В.З.: Какова же сейчас территория предприятия?
Е.К.: Общая территория, на которой расположены три наши основные площадки, составляет более 81.000 м2.
В.З.: Сколько человек работает на заводе? Можно ли назвать Microtech градообразующим предприятием?
Е.К.: Это слишком громкие слова. Население города Калуги составляет около 350 тыс. чел., на нашем же предприятии на данный момент работает чуть более 1000 сотрудников. Однако есть одна особенность. На рынке труда города доминируют заводы оборонной промышленности, поэтому с точки зрения "гражданского" высокотехнологичного бизнеса активно и уверенно развивающийся Microtech — это очень крупное предприятие.
В.З.: Расскажите, пожалуйста, подробнее об ассортименте выпускаемой продукции?
Е.К.: Весь ассортимент продукции производится на трех типах шасси: STEP, PROXIMA и ULTRA. Широта же модельного ряда достигается путем установки различных комплектующих и декоративных фронтальных панелей. Есть большой выбор блоков питания, корпуса оснащаются специальным воздуховодом по спецификации Intel. Такой подход удовлетворяет запросы подавляющего большинства потребителей.
В.З.: Microtech выпускает не только стандартные корпуса, но и ОЕМ-партии по индивидуальным заказам…
Е.К.: Да, на данный момент порядка 40% объема выпускаемой продукции составляют ОЕМ-продукты для крупных сборщиков. Для них мы предоставляем ряд дополнительных возможностей. Это и изготовление лицевых панелей по эскизам заказчика, и персонификация как лакокрасочным покрытием, так и штамповкой на боковой стенке корпуса. Возможны и более серьезные конструктивные изменения.
В.З.: Сколько занимает перенастройка производства под индивидуальный заказ?
Е.К.: Если говорить об обычных условиях ОЕМ-проекта, где шасси остается стандартным, то на разработку и изготовление новой лицевой панели уйдет несколько недель. При условии выбора из уже готовых разработок это вопрос дней. Что касается организации производства, то мы стараемся не делать складских запасов и используем прямую поточную организацию производства. Тем не менее, даже с учетом временных затрат на переработку материалов по циклам от постановки рулона металла на линию резки до появления готового корпуса пройдет не более суток.
В.З.: Есть ли у корпусов Microtech отличительные, "фамильные" черты?
Е.К.: Все наши корпуса собственной разработки, поэтому у них уникально все, насколько это возможно с точки зрения уникальности, ведь данная продукция регламентирована соответствующими стандартами. Наши корпуса разработаны с учетом всех передовых технологий, их отличает эргономичность и высокое качество изготовления. Мы никогда не экономим на сырье. Корпуса выполняются из высококачественного металла толщиной 0,5-0,8 мм, а позиции крепежных элементов шасси выполнены таким образом, что они связывают абсолютно все плоскости изделия, поэтому диагональный перекос изделия исключен даже при некотором силовом воздействии. Плюс для ОЕМ-продуктов производится предварительная подготовка для вторичной сборки, включающая целый спектр дополнительных услуг.
В.З.: А что вы можете сказать по поводу сертификации, отмечена ли продукция Microtech наградами?
Е.К.: Наша продукция имеет сертификаты TUV, Ростест (РСТ). Мы регулярно участвуем в различных выставках, неоднократно отмечены дипломами CeBIT и "Комтек".
В.З.: Как обстоят на предприятии дела с разработкой новых изделий, учитываются ли мнения реальных пользователей и заказчиков?
Е.К.: Разработка новых изделий и модернизация существующих носит перманентный характер. В ситуации сложной конкуренции просто необходимо адекватно оценивать рынок и выпускать конкурентоспособные продукты. Катализатором же развития и является обратная связь, пожелания наших клиентов. Все это и ложится в основу технического задания, поступающего в группу разработки новых изделий. Далее КБ оценивает возможности внесения изменений в стандартные модели для обеспечения всех требований. Если это невозможно, то происходит разработка нового изделия. После завершения разработки согласуется дизайн, утверждается бизнес-план и с точки зрения целесообразности принимается окончательное решение о запуске в производство. Собственно, таким путем и прошли все разработки, которые мы сейчас имеем. Что касается модернизации, то в настоящий момент завод осуществляет один из ее этапов по расширению установочных возможностей для вентиляторов большего диаметра и новых моделей блоков питания.
В.З.: Имеются ли у компании разработки корпусов стандарта BTX?
Е.К.: Наша компания очень внимательно следит за всеми тенденциями рынка. Поэтому у нас есть разработка ВТХ, готовая к серийному производству с учетом всей цепи оснастки. А тестовые модели корпусов формата ВТХ мы удачно демонстрируем уже два года подряд на выставке CeBIT в Ганновере. Сроки же запуска в производство пока не определены.
В.З.: Получается так, что выпуск корпусов ВТХ откладывается из-за слабого интереса к ним самого рынка?
Е.К.: Это вопрос не к производственному подразделению компании, хотя вы совершенно правы: процесс пока тормозится только рынком, который видит в переходе на ВТХ излишние затраты.
В.З.: Из окна вашего кабинета прекрасно видно новый складской комплекс. Можно подробнее рассказать о планах развития завода?
Е.К.: Складские помещения как раз и построены на зарезервированной территории для строительства нового промышленного комплекса. Таким образом, мы уже приступили к ее освоению. Все это делается для увеличения объема производства, направленного на сохранение темпа удвоения количества выпускаемой продукции. Кстати, в следующем сезоне планируется очередное удвоение выпуска до 2 млн корпусов в год. Что касается мощностей для развития, то сейчас происходит реализация нашего проекта, который подразумевает приобретение парка дополнительного оборудования. Также мы планируем увеличить отдачу от оборудования путем изменения сменности работы, повышения уровня автоматизации. Все эти мероприятия, по нашим расчетам, позволят выйти на планируемые мощности.
В.З.: Перестройка производства происходит без остановки технологического цикла?
Е.К.: Да, это текущий процесс, параллельный с выпуском продукции.
В.З.: Немаловажным вопросом является вопрос обеспечения качества выпускаемой продукции.
Е.К.: Вопрос качества — это один из самых важных вопросов, который непосредственно касается конкурентоспособности, поэтому в компании существует служба качества, которая напрямую подчинена президенту компании. Сотрудники службы качества находятся в каждой смене каждого производственного цеха, работают достаточно требовательно и жестко, что не позволяет некачественной продукции попасть в изделие, а тем более покинуть сборочный конвейер.
В.З.: Как проходит подбор поставщиков и какие требования предъявляются к ним?
Е.К.: Отбор поставщиков происходит достаточно жестко. Как я уже говорил, мы используем только высококачественное сырье. Этим объясняется их преимущественно европейская и азиатская география. Например, металл мы получаем из Голландии, Кореи и даже из Японии. Все поставщики были отобраны временем по двум критериям: должному уровню качества и пунктуальностью исполнения обязательств. Для нас важны не только технологические свойства материалов, но и внешний вид продукта, определяемый сырьем. Поэтому все сырье ненадлежащего качества отправляется обратно поставщику — это наша позиция. Мы предпочитаем долгосрочное сотрудничество с компаниями, которые уже успели завоевать хорошую репутацию.
В.З.: Есть ли какие-то особенности организации производства компьютерной техники в России?
Е.К.: Microtech — предприятие, где полностью реализован технологический цикл по выпуску компьютерной продукции, что уникально не только для города Калуги, но, пожалуй, и для всей России в целом. Поэтому особенности есть. Часть оборудования была разработана и изготовлена
самостоятельно: линия рулонной резки металлов, различные средства автоматизации, как, например, автоматический укладчик готовой продукции в цехе сборки и т.д. Это способствует снижению цены без потери качества.
В.З.: Т.е. Microtech занимается не только производством корпусов, но и необходимого оборудования?
Е.К.: Совершенно верно, мы имеем инструментальное производство, которое расположено на двух площадках. Имеем парк оборудования, который позволяет нам самостоятельно выпускать необходимую оснастку. Это связано с процессом непрерывного обновления продукции, о котором мы говорили ранее. Существует бригада для разработки нестандартного оборудования автоматизации производства своими силами. Но здесь мы всегда проводим грань экономической целесообразности. Некоторые вещи, нужные нам, выгоднее приобрести, и мы их покупаем. Некоторые элементы, которые можно купить, не обладают всем перечнем необходимых свойств, поэтому мы вынуждены их модернизировать. А некоторых элементов просто не существует. Мы их придумываем, разрабатываем, изготавливаем и запускаем в производство. Что это дает, кроме снижения себестоимости? Гибкость и оперативность!
В.З.: "Microtech: технологии будущего сегодня" — красиво или объективно?
Е.К.: Объективно, и это абсолютная правда. Скажу более: лозунг сначала воплотился в жизнь, и только потом был озвучен. Эта фраза пришла сама по себе, потому что это и есть суть нашей работы.
В.З.: Спасибо за то, что согласились ответить на наши вопросы. Желаем Вам дальнейших производственных успехов.
В заключение хочется сказать, что качество корпусов, изготавливаемых компанией, и их конечная стоимость говорят сами за себя. Microtech на деле опровергает миф о том, что российский производитель не способен производить конкурентоспособную продукцию в сфере высоких технологий.
Василий Запотылок, vasily@techlabs.by
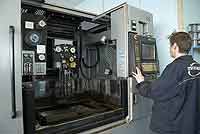
Из высококачественного пластика отливаются все необходимые части начиная от кнопок и заканчивая лицевыми панелями. Кстати, в цехе часть оборудования разработана и внедрена самим заводом. Это промышленные холодильники и дробильные станки. Последние предназначены для измельчения литников (технологической пластмассы) и выбракованных изделий, обеспечивая безотходность процесса. Готовые детали бережно упаковываются и поступают на покраску. Металлические части красятся "порошком", который закрепляется под термическим воздействием. Пластик красится обычным методом. Здесь же расположен станок тампопечати. Хотите нанести свое изображение или логотип — нет проблем!
И, наконец, сборочный конвейер, где производится ручная сборка — сборка под строгим контролем ОТК. Требуется совсем небольшое время, чтобы из отдельных частей получить и упаковать готовый компьютерный корпус. Работа на конвейере осуществляется очень быстро, по словам представителей, даже быстрее, чем на заводах в Юго-Восточной Азии. Одним из последних этапов является установка блока питания, который проходит продолжительное тестирование под нагрузкой в термоизолированной камере, где на специальных стеллажах стоят сотни блоков питания. К обеспечению качества в Microtech подходят щепетильно. Ни один готовый корпус не попадет на склад без отметки службы ОТК. И это при том, что контроль качества осуществляется на каждой, даже самой мелкой, операции технологического цикла. Некоторым может показаться, что технологический цикл несложен. Поверьте, это не так. Производство требует колоссальных материальных и интеллектуальных затрат, в том числе связанных с обслуживанием парка оборудования. В качестве примера упомяну лишь об инструментальном цехе. Сложно было поверить в поломку многокилограммовой оснастки, пока мы собственными глазами не увидели расколовшийся металлический штамп толщиной порядка 3 см. Имеющиеся в распоряжении современнейшие электрозионные станки и обрабатывающий центр позволяют изготовить копию в самое короткое время. При этом точность описывается микронами!
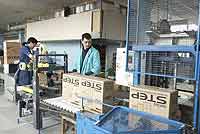
Василий Запотылок: Добрый день, Евгений Владимирович! Мы только что посмотрели завод, побывали на трех производственных площадках — впечатляет! Расскажите, пожалуйста, историю становления предприятия.
Евгений Куликов: Предприятие с момента основания сохраняет высокие темпы развития. Объем выпускаемой продукции регулярно удваивается — это не голословное утверждение, а факт, подтвержденный цифрами (сейчас это свыше 1 млн корпусов в год), что позволяет нам быть высокоэффективными как по экономическим, так и по производственным показателям. Сначала весь технологический цикл размещался на площадке №1, где мы сейчас с Вами и находимся. Для первоначальных объемов выпуска этого было достаточно. Но их увеличение потребовало в 2000 г. принять решение о приобретении производственной площадки №2, а в 2003 г. — производственной площадки №3. На них расположились цеха металлообработки и литья пластмасс соответственно. Таким образом, в техпроцесс были интегрированы все три производственные площадки. Однако сейчас уже ведется разработка проекта строительства нового производственного комплекса, который будет в 4 раза превосходить все существующие производственные мощности завода!
В.З.: Какова же сейчас территория предприятия?
Е.К.: Общая территория, на которой расположены три наши основные площадки, составляет более 81.000 м2.
В.З.: Сколько человек работает на заводе? Можно ли назвать Microtech градообразующим предприятием?
Е.К.: Это слишком громкие слова. Население города Калуги составляет около 350 тыс. чел., на нашем же предприятии на данный момент работает чуть более 1000 сотрудников. Однако есть одна особенность. На рынке труда города доминируют заводы оборонной промышленности, поэтому с точки зрения "гражданского" высокотехнологичного бизнеса активно и уверенно развивающийся Microtech — это очень крупное предприятие.
В.З.: Расскажите, пожалуйста, подробнее об ассортименте выпускаемой продукции?
Е.К.: Весь ассортимент продукции производится на трех типах шасси: STEP, PROXIMA и ULTRA. Широта же модельного ряда достигается путем установки различных комплектующих и декоративных фронтальных панелей. Есть большой выбор блоков питания, корпуса оснащаются специальным воздуховодом по спецификации Intel. Такой подход удовлетворяет запросы подавляющего большинства потребителей.
В.З.: Microtech выпускает не только стандартные корпуса, но и ОЕМ-партии по индивидуальным заказам…
Е.К.: Да, на данный момент порядка 40% объема выпускаемой продукции составляют ОЕМ-продукты для крупных сборщиков. Для них мы предоставляем ряд дополнительных возможностей. Это и изготовление лицевых панелей по эскизам заказчика, и персонификация как лакокрасочным покрытием, так и штамповкой на боковой стенке корпуса. Возможны и более серьезные конструктивные изменения.
В.З.: Сколько занимает перенастройка производства под индивидуальный заказ?
Е.К.: Если говорить об обычных условиях ОЕМ-проекта, где шасси остается стандартным, то на разработку и изготовление новой лицевой панели уйдет несколько недель. При условии выбора из уже готовых разработок это вопрос дней. Что касается организации производства, то мы стараемся не делать складских запасов и используем прямую поточную организацию производства. Тем не менее, даже с учетом временных затрат на переработку материалов по циклам от постановки рулона металла на линию резки до появления готового корпуса пройдет не более суток.
В.З.: Есть ли у корпусов Microtech отличительные, "фамильные" черты?
Е.К.: Все наши корпуса собственной разработки, поэтому у них уникально все, насколько это возможно с точки зрения уникальности, ведь данная продукция регламентирована соответствующими стандартами. Наши корпуса разработаны с учетом всех передовых технологий, их отличает эргономичность и высокое качество изготовления. Мы никогда не экономим на сырье. Корпуса выполняются из высококачественного металла толщиной 0,5-0,8 мм, а позиции крепежных элементов шасси выполнены таким образом, что они связывают абсолютно все плоскости изделия, поэтому диагональный перекос изделия исключен даже при некотором силовом воздействии. Плюс для ОЕМ-продуктов производится предварительная подготовка для вторичной сборки, включающая целый спектр дополнительных услуг.
В.З.: А что вы можете сказать по поводу сертификации, отмечена ли продукция Microtech наградами?
Е.К.: Наша продукция имеет сертификаты TUV, Ростест (РСТ). Мы регулярно участвуем в различных выставках, неоднократно отмечены дипломами CeBIT и "Комтек".
В.З.: Как обстоят на предприятии дела с разработкой новых изделий, учитываются ли мнения реальных пользователей и заказчиков?
Е.К.: Разработка новых изделий и модернизация существующих носит перманентный характер. В ситуации сложной конкуренции просто необходимо адекватно оценивать рынок и выпускать конкурентоспособные продукты. Катализатором же развития и является обратная связь, пожелания наших клиентов. Все это и ложится в основу технического задания, поступающего в группу разработки новых изделий. Далее КБ оценивает возможности внесения изменений в стандартные модели для обеспечения всех требований. Если это невозможно, то происходит разработка нового изделия. После завершения разработки согласуется дизайн, утверждается бизнес-план и с точки зрения целесообразности принимается окончательное решение о запуске в производство. Собственно, таким путем и прошли все разработки, которые мы сейчас имеем. Что касается модернизации, то в настоящий момент завод осуществляет один из ее этапов по расширению установочных возможностей для вентиляторов большего диаметра и новых моделей блоков питания.
В.З.: Имеются ли у компании разработки корпусов стандарта BTX?
Е.К.: Наша компания очень внимательно следит за всеми тенденциями рынка. Поэтому у нас есть разработка ВТХ, готовая к серийному производству с учетом всей цепи оснастки. А тестовые модели корпусов формата ВТХ мы удачно демонстрируем уже два года подряд на выставке CeBIT в Ганновере. Сроки же запуска в производство пока не определены.
В.З.: Получается так, что выпуск корпусов ВТХ откладывается из-за слабого интереса к ним самого рынка?
Е.К.: Это вопрос не к производственному подразделению компании, хотя вы совершенно правы: процесс пока тормозится только рынком, который видит в переходе на ВТХ излишние затраты.
В.З.: Из окна вашего кабинета прекрасно видно новый складской комплекс. Можно подробнее рассказать о планах развития завода?
Е.К.: Складские помещения как раз и построены на зарезервированной территории для строительства нового промышленного комплекса. Таким образом, мы уже приступили к ее освоению. Все это делается для увеличения объема производства, направленного на сохранение темпа удвоения количества выпускаемой продукции. Кстати, в следующем сезоне планируется очередное удвоение выпуска до 2 млн корпусов в год. Что касается мощностей для развития, то сейчас происходит реализация нашего проекта, который подразумевает приобретение парка дополнительного оборудования. Также мы планируем увеличить отдачу от оборудования путем изменения сменности работы, повышения уровня автоматизации. Все эти мероприятия, по нашим расчетам, позволят выйти на планируемые мощности.
В.З.: Перестройка производства происходит без остановки технологического цикла?
Е.К.: Да, это текущий процесс, параллельный с выпуском продукции.
В.З.: Немаловажным вопросом является вопрос обеспечения качества выпускаемой продукции.
Е.К.: Вопрос качества — это один из самых важных вопросов, который непосредственно касается конкурентоспособности, поэтому в компании существует служба качества, которая напрямую подчинена президенту компании. Сотрудники службы качества находятся в каждой смене каждого производственного цеха, работают достаточно требовательно и жестко, что не позволяет некачественной продукции попасть в изделие, а тем более покинуть сборочный конвейер.
В.З.: Как проходит подбор поставщиков и какие требования предъявляются к ним?
Е.К.: Отбор поставщиков происходит достаточно жестко. Как я уже говорил, мы используем только высококачественное сырье. Этим объясняется их преимущественно европейская и азиатская география. Например, металл мы получаем из Голландии, Кореи и даже из Японии. Все поставщики были отобраны временем по двум критериям: должному уровню качества и пунктуальностью исполнения обязательств. Для нас важны не только технологические свойства материалов, но и внешний вид продукта, определяемый сырьем. Поэтому все сырье ненадлежащего качества отправляется обратно поставщику — это наша позиция. Мы предпочитаем долгосрочное сотрудничество с компаниями, которые уже успели завоевать хорошую репутацию.
В.З.: Есть ли какие-то особенности организации производства компьютерной техники в России?
Е.К.: Microtech — предприятие, где полностью реализован технологический цикл по выпуску компьютерной продукции, что уникально не только для города Калуги, но, пожалуй, и для всей России в целом. Поэтому особенности есть. Часть оборудования была разработана и изготовлена
самостоятельно: линия рулонной резки металлов, различные средства автоматизации, как, например, автоматический укладчик готовой продукции в цехе сборки и т.д. Это способствует снижению цены без потери качества.
В.З.: Т.е. Microtech занимается не только производством корпусов, но и необходимого оборудования?
Е.К.: Совершенно верно, мы имеем инструментальное производство, которое расположено на двух площадках. Имеем парк оборудования, который позволяет нам самостоятельно выпускать необходимую оснастку. Это связано с процессом непрерывного обновления продукции, о котором мы говорили ранее. Существует бригада для разработки нестандартного оборудования автоматизации производства своими силами. Но здесь мы всегда проводим грань экономической целесообразности. Некоторые вещи, нужные нам, выгоднее приобрести, и мы их покупаем. Некоторые элементы, которые можно купить, не обладают всем перечнем необходимых свойств, поэтому мы вынуждены их модернизировать. А некоторых элементов просто не существует. Мы их придумываем, разрабатываем, изготавливаем и запускаем в производство. Что это дает, кроме снижения себестоимости? Гибкость и оперативность!
В.З.: "Microtech: технологии будущего сегодня" — красиво или объективно?
Е.К.: Объективно, и это абсолютная правда. Скажу более: лозунг сначала воплотился в жизнь, и только потом был озвучен. Эта фраза пришла сама по себе, потому что это и есть суть нашей работы.
В.З.: Спасибо за то, что согласились ответить на наши вопросы. Желаем Вам дальнейших производственных успехов.
В заключение хочется сказать, что качество корпусов, изготавливаемых компанией, и их конечная стоимость говорят сами за себя. Microtech на деле опровергает миф о том, что российский производитель не способен производить конкурентоспособную продукцию в сфере высоких технологий.
Василий Запотылок, vasily@techlabs.by
Компьютерная газета. Статья была опубликована в номере 19 за 2006 год в рубрике железо